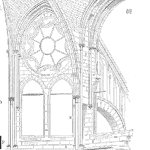
Polyethylene is one of the most commonly used engineering plastics.
Its chemical resistance properties and ease of fabrication make it popular in the chemical industries. Its molecular structure provides the key to its versatility.
Keywords: HDPE, long chain macromolecule, thermoplastic, plastic welding.
What is polyethylene?
Polyethylene (PE) is a plastic. It is made by combining single carbon atoms together to create long chains of carbon atoms. The long chains are called macromolecules.
Attached to each carbon atom are usually two hydrogen atoms. Figure 1 shows how the macromolecule of polyethylene is arranged.
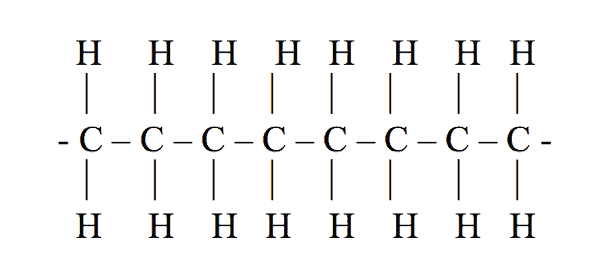
PE belongs to the family of plastics called thermoplastics. These plastics have weak forces that attract the macromolecules together. The other family of plastics is the thermosets.
In these the hydrogen atoms are occasionally replaced with other atoms that attach to neighboring chains, locking them together. The thermoplastics can be melted and reshaped but the thermosets can only be used once.
The process of using solvents and heat to convert from single atoms to a string of thousands of atoms long is called polymerization.
During polymerization, many carbon chains are created at the one time. When PE is molten the long chains are mobile but upon cooling, the long chains intertwine and lock together. Much like when spaghetti is boiled and let cool.
The density of PE depends on the process used to make it. One method produces low-density (LDPE) while a high density (HDPE) results from the other.
The plastic’s density can be further modified to produce medium density (MDPE) and ultra high molecular weight (UHMWPE) products. The properties of each type of PE depend on the shape and length the carbon chains and how closely they compact.
The structure of polyethylene
The carbon chain length and extent of branching greatly affect the properties of the plastic. Figure 2 shows the different structures of the macromolecules for LDPE and HDPE.
The amount of side-chain branching varies the closeness that molecules can come together. Closely compact chains give more rigid and solid plastics.
Occasionally the molecules will lie side by side. This creates a harder clump known as a crystalline alignment.
Plastics with high amounts of crystalline arrangements are harder and stronger but more brittle. UHMWPE chains have few branches and are 10 – 20 times longer than HDPE. This permits the development of many more crystalline areas than the lower density PEs.
Randomly arranged chains without order make an amorphous structure. Examples of each structure are shown in Figure 3.
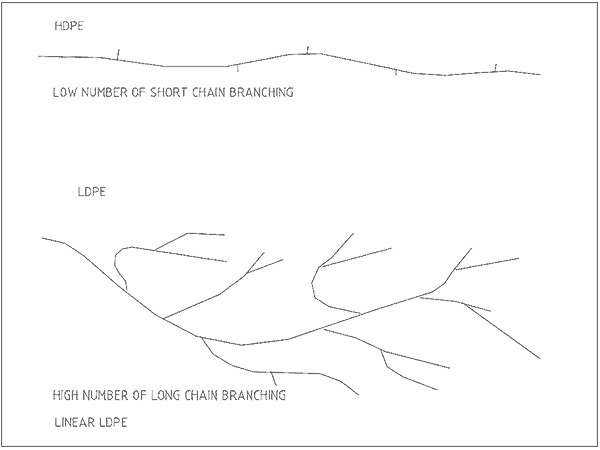
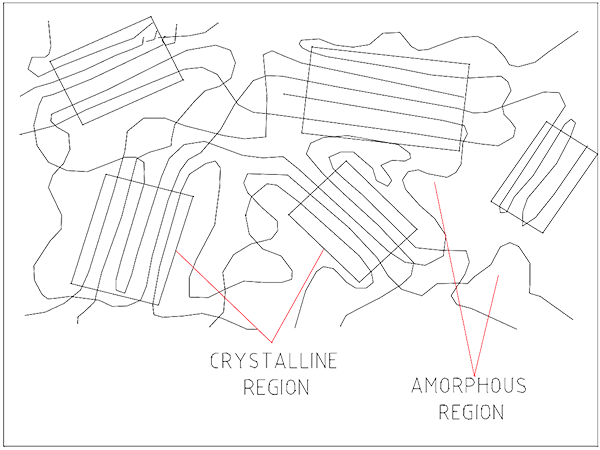
Properties and uses
The degree of branching and crystallinity in PE produce variations in behavior and properties.
Table 1 gives an overview of the differences between types of PE.
Type | Density Specific Gravity | Distort Temp °C | Tensile Strength N/mm2 | Abrasion Resist |
---|---|---|---|---|
LDPE | 0.91 – 0.92 | 40 – 50 | 170 | Soft |
MDPE | 0.93 – 0.94 | 60 – 70 | 275 – 450 | |
HDPE | 0.94 – 0.96 | 70 – 90 | Over 625 | |
UHMWPE | > HDPE | > HDPE | > HDPE | Excellent |
The lower density PE’s have good toughness (ability to deform without breaking) and excellent elongation (ability to stretch) with LDPE stretching up to 6 times its original length before breaking.
This makes them a useful plastic for molding and extruding in shapes of bottles, tanks, sheets, and pipes. UHMWPE is used for machinery parts where a high wear, low friction material is required.
In its natural form, PE is clear and goes white and translucent as the amount of crystallinity increases. It is used in stretch films, plastic bags, and plastic bottles. Coloring agents can be added.
It degrades from ultraviolet radiation. When used in sunlight 2 – 3% carbon black powder is added. Life expectancies in outside conditions of over 25 years are attainable.
Chemical resistance properties of PE are excellent, covering a wide range of chemicals. Check compatibility with the supplier.
Environmental stress cracking
A major consideration with the use of PE is its tendency to exhibit environmental stress cracking (ESC).
ESC is sudden failure induced by internal stresses from outside loads or fabrication strains. Often involving containment of liquid hydrocarbons and man-made soaps and oils. ESC decreases as carbon chain entanglement increases.
It is more likely in HDPE than LDPE. ESC tests are available and recommended if using PE to store previously undocumented chemicals.
Welding polyethylene
Since PE is a thermoplastic it can be melted and joined. When welding, the temperature is raised above the melting point (110 – 135oC) to a temperature of about 250oC using a hot air gun for hand welding or a heated plate for butt- welded pipes.
When hand welding PE a filler rod is pushed into the melt. When butt-welding pipe the two ends are heated and pushed together for 10 to 15 seconds.
At the melted surface the carbon chains intertwine and cool. Successful welds need a sufficiently high temperature and pressure at the melted surfaces for a long enough time to let the carbon chains mesh well.
A ‘cold weld’ occurs if the melt temperature is too low. A weak failure prone weld results which break away from the parent material.
Mike Sondalini Maintenance Engineer
Thanks for overview.
Wikipedia has some information. And other free drill down links on this subject?
I didn’t know that polyethylene was a thermoplastic that could be welded. I think it’s pretty amazing that we have developed materials like this that are so versatile. It’s important that we understand how polyethylene is made and what it’s properties are so we can potentially make use of it as we build and improve different things.
Hi Bernard, yes the world of polymers is pretty broad and versatile. I used to work at Raychem Corp. and we did some magically things with polymers. There’s a lot to learn out there. have fun. cheers, Fred