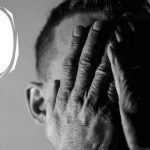
Over the last few decades, advancements in technology have dramatically changed the maintenance and reliability industry. Organizations have invested heavily in automation and technology to reduce staff overhead, improve product quality and increase safety. One thing that hasn’t changed much in the last few decades is preventive maintenance, or PM. PM is all about performing routine maintenance to improve equipment reliability, performance and cost-effectiveness. If applied correctly, PM has the capacity to transform an organization’s maintenance approach and lead to significant improvements in equipment reliability. However, there are many mistakes that can ruin an organization’s PM program.
The following are seven preventive maintenance mistakes to avoid:
1. Not setting standard intervals for maintenance
Not setting standard intervals is one of the biggest preventive maintenance mistakes, because going too long in between PM tasks can lead to equipment damage. The repairs may end up costing you more than ongoing maintenance would have. Establishing appropriate frequencies for your scheduled maintenance is essential for optimizing equipment performance, reliability and longevity.
2. Not capturing enough data
Regular PM inspections and other maintenance activities can provide you with insight into problems that are occurring. You can mine the data to determine what you need to do in your PM program. You can also identify systems or sub-systems that are experiencing failure and then come up with a game plan to address those issues in your PM program. Maintenance software enables you to measure performance by helping you keep track of data, such as the percentage of completed PM tasks, the number of breakdowns occurring, or the number of times you’ve had to repair specific equipment.
3. Not Applying PM to all of your equipment
Omitting key equipment in your PM program can leave a company vulnerable to failure. PM should be scheduled for not only process-critical equipment, but also all support and infrastructure items. Failing to maintain facilities support equipment can lead to major downtime events. Regular preventive maintenance will reduce many, but not all, failures. Emergency maintenance may be needed to handle random failures, and this data needs to be captured and preventive measures included in future PMs.
4. Vague instructions
PM tasks should clearly explain what the maintenance technician has to measure, what condition they have to look for, and what they should do if they find an unsatisfactory condition while performing a PM task. If you want the job to be done right, you need to be as specific as possible, including attaching needed drawings, pass/fail criteria, condition monitoring, etc.
5. Not allowing maintenance technicians to provide comments when performing a PM task
When you have someone perform a PM task, give him or her the opportunity to provide comments about what they found when performing the inspection. It’s important to collect feedback from maintenance technicians if you want to optimize your PM program. This data can be used to correct instructions and refine scheduling.
6. Poor schedule compliance
Companies complaining that their PM programs are ineffective often don’t complete PM tasks on time. In order to develop a successful PM program, it’s essential to complete the right tasks at the right time. PMs are often assigned the lowest priority when in fact they should be considered high priority work. Companies should build scheduled downtime into their equipment operational schedules to provide adequate time for completing PMs.
7. Not knowing the difference between failure finding tasks and PM tasks
Many organizations lump failure finding tasks with PM tasks as if they were one in the same but they are not. Failure finding tasks are time-based inspections of equipment that are performed to determine whether a failure has already occurred, while PM tasks are intended to prevent an item from failing. Failure finding tasks deserve to be in a category of their own.
Preventive maintenance tasks enable you to spot problems early on and repair equipment rather than be required to replace it down the line. The full replacement of equipment is often an unnecessary expense that can be avoided if you have an effective PM program in place.
DPSI develops maintenance management software that streamlines the PM process by automating many tasks and capturing important data. Our knowledgeable staff can help your organization learn how to pinpoint preventive maintenance mistakes and how to avoid them using our CMMS/EAM systems. Contact DPSI today for more information or to set up a free trial of on-premise or cloud-hosted maintenance management software.
Leave a Reply