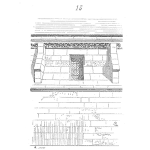
This is a guest post by Cristian Campos
In manufacturing environments, especially in high-volume production processes, it is important to ensure the highest Machine availability rate for critical equipment as a crucial factor in achieving the expected output goals. The more the availability value there is, the better the plant’s capacity to achieve production requirements since the time available for each piece of equipment will be maximized.
Availability issues identified; How to start?
It is important for organizations with low performance to evaluate the availability values for the critical equipment by defining a goal and tracking the performance and availability trend against that defined target, and if it applies, create, and implement a plan to obtain results more quickly by executing the following steps based on the results obtained in its application in a real case.
Steps to improve machine availability
- Step 1: status ‘Like new’:
This step proposes to identify the baseline conditions for the equipment and make the necessary interventions in the equipment to reestablish ‘factory settings’ or have new-like conditions possible. When the equipment brings factory settings or values, it is essential to set them. If there are damaged or worn parts or they must be replaced. Any other adjustment recommended by the manufacturer or identified by process experts should be considered in this step.
- Step 2: Downtime causes:
It is essential to define the top three downtime causes for each equipment category (Pareto analysis can be used in this step) based on available historical data. The objective of this analysis is to have a quick idea about the issues to prioritize to have a significant improvement in the availability value. A strong recommendation for this analysis is important to include the equipment operator’s feedback and the vendor recommendations included in the equipment manual.
- Step 3: Troubleshooting checklist:
Once the top three main downtime causes have been identified, use a checklist with instructions to address the downtime causes during a troubleshooting activity. This recommendation will allow all the technicians to address the issues and reduce the operation’s time out, reducing the impact of different technical levels within the technician’s group. Additionally, the checklist should be part of the equipment documentation in the maintenance area.
- Step 4: Training:
A training system should be in place to assure that all the technicians involved are adequately trained and have the required technical level to address any downtime issue and therefore reduce the downtime. Additionally, a troubleshooting checklist can be used as a guide for training purposes.
- Step 5: Critical spare parts list:
It is important to define a list of critical spare parts and as well as having those parts available when needed. Downtimes caused by a lack of a spare can be easily eliminated with this recommendation.
- Step 6: Equipment Failure Modes Analysis:
If the equipment under analysis has a formal Equipment Failure Modes Analysis document, it is important to execute an assessment to define if any update is required after the analysis has been made. If there is no formal Equipment Failure Modes Analysis document, the recommendation is to create a preliminary failure modes file based on the top three downtime causes results. It is essential to have documentation that could help the maintenance group to be more efficient and then increase availability values. The Equipment Failure Modes Analysis will be another input for the training process.
Regarding documentation, if more documents need to be updated with the information resulting from the quick list of recommendations, it is important to do so.
Once availability value has been increased? What is next?
This list is a recommended sequence of steps to execute a preliminary availability improvement project to have quick positive results in equipment performance; accelerating initial results is the primary purpose of this sequence. Besides the performance improvement, the people in the operations organization need to see results as part of the motivation to continue the process successfully. Once the initial results are measurable, the next step is to execute a formal maintenance improvement analysis such as RCM, RCA, or equivalent to achieve sustainable results with a strong methodology if necessary.
Leave a Reply