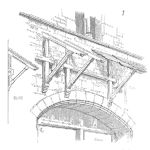
My first major product design review was much less than I thought it would be. This was a new inkjet printer platform and the checkpoint review assessed the teams work and readiness to move to the next stage of development. A team of over 200 engineers and managers meet for 4 hours.
The electrical, mechanical, software, and other engineering managers each showed a series of template-based slides. Each spoke for about 20 to 30 minutes. Marketing, quality, manufacturing, and other groups also had a turn at the podium. Most said little other than everything was ok and there were a few minor challenges.
It wasn’t informative to me. There wasn’t much discussion. Very few questions.
Where was the review? The cross-examination? The technical assessment using some, any criterion?
Later I learned there were weeks of preparation for this meeting. I just wasn’t involved.
Development phase gate process and reviews
The stage gate process for product or process design and development includes regular reviews or evaluations. The checkpoints often include the current design’s status on meeting the wide range of design specifications and the team’s readiness as they move to the next stage of development.
Every development team may name the stages differently. Yet, most organizations follow the logical progression of
- Phase 1: Market Research
- Phase 2: Concepts
- Phase 3: Design & Development
- Phase 4: Manufacturing Development
- Phase 5: Final Design and Start of Production
There may be additional phases for product improvement and retirement.
The details of each phase vary slightly depending on the industry, market, product complexity, and team size and experience. In general, each phase increases the resource investment involved with the product.
The ISO 9001 standard outlines four steps for the design process
- Design and Development Planning
- Design Input
- Design Output
- Design Verification
Which is generic and focuses only on the design and development process. Many organizations use concurrent engineering which primarily overlaps the manufacturing development activities with the design & development activities. In practice, there is a lot of work across the organization occurring in parallel to create even a simple product.
Various tools connect reliability into the process
Reliability engineering has a role within every element of the process and the organization may employ a wide range of tools.
Some tools have specific output and fit within one phase or step, while others occur iteratively through multiple stages of the process.
Tools to estimate reliability goals tend to fit in the market research and concepts phase, whereas FMEA enjoys a role in every phase.
Keep in mind that many of the tools we associate with reliability engineering are not only accomplished by reliability professionals. Mechanical engineers, for example, use design of experiments and geometric dimensioning and tolerancing on a regular basis. It is when the tool has an element or consideration of product reliability that it becomes a reliability engineering tool.
The idea is to fit the right tool within a development phase that provides sufficient results for that phase. For example, we do not need to work out detailed stress/strength or derating calculations during the marketing and concept phase. Generally, in the concept or early design phase, we think through and document a reliability plan.
The plan includes the specific tools to solve specific problems or accomplish tasks going forward. At a high level, this includes setting or refining the goals, identifying and resolving risks, and estimating future reliability performance.
Related:
Introduction to Design for Reliability (article)
Understanding the Design Process (article)
Meditation and Design for Reliability (article)
Fred,
Do you have more solidified examples… the ones that receive challenging comments and hitting critical points during the phase cycles. I understand these may only be available in the courses you offer however I do think they will be much appreciated…
Just my two cents…
Best Regards as ever.
Tinghui Xin
HI Tinghui, thanks for the comment. I do not have a course that includes a lot of detail on design reviews.
I’ll write in my other blog, accendoreliability.com under articles about better or best practices for engineering or technical reviews.
The full team review covers a lot of material and is a great summary of the overall status of the project. And, it often is preceded by numerous very detailed and valuable engineer to engineer reviews.
Cheers,
Fred
Interesting that product design application developers are at least trying to fill the market space in reliability engineering calculations. Who does this is Electronics engineering design?
Altium? Cadence? Mentor Graphics?
It would be great is the big ME or EE package would include reliability elements in their packages – they do not as far as I know beyond design functionality.
Cheers,
Fred
Hi Peter, thanks for the comment. Yes a few package are including reliability elements, which unfortunately is not widely used. cheers, Fred