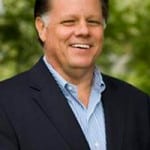
When is the best time to do an RCM analysis on your equipment?
While RCM Blitz™ can be applied at any time in the asset lifecycle, the best time to do an RCM analysis is in the design phase of a capital project. Reliability Centered Design is much more than a thorough RCM analysis on a critical asset, it also uses other reliability tools that should be applied at each gate of your capital process such as Reliability Block Diagrams, Criticality Analysis, and Spare Parts Assessment. While many companies have been reluctant to spend the extra money to add RCM to their capital process, those that have report an insignificant addition of 1-3% in the total cost of the project. The savings for building reliability into your capital process are recognized early on as Installation, accreditation and start-up phases of your project will be quicker/more successful than other project launches.
Why can’t we just use a library of failure modes to develop the maintenance strategy for our equipment?
All Failure Modes Libraries are built using common or engineered Failure Modes that one would expect to experience with a given component or part. While each of these Failure Modes is valid, they are rarely the Failure Modes that you are experiencing at your facility. Simply put, these are the same Failure Modes a OEM would use to create the maintenance plan in the manual that comes with your asset. While some of these Failure Modes might apply and deliver a list of basic PM (Preventive Maintenance) and PdM (Predictive Maintenance, Condition Based Maintenance, On-Condition Maintenance) tasks, they will NOT deliver the level of reliability you are looking for. RCM when properly applied addresses the Failure Modes that result from the context in which operate the asset and the environment in which it operates. It is these Failure Modes that result in significant repetitive and random cause failures that have a direct impact on the operational capability of the equipment as well as the safety and environmental performance of your facility.
Why do so many companies struggle to implement a successful, sustained RCM program?
If you ask the companies themselves, there are several answers to this question each amounts to nothing more than an excuse. If you failed to develop a sustained reliability effort you failed at one or more of the following:
Leadership – A good Reliability Program, or RCM effort requires a strong leader. I’m not talking about a Military General here but someone who understands the concepts of Reliability well enough to develop a plan and who can influence people in key roles to help fulfill that plan.
Structure – In order to get the most from your equipment, you need the foundation elements of a good Asset Management Program in place. A CMMS that has a complete listing of your equipment hierarchy to the component level that meets ISO 14224 standards. A criticality analysis performed to the component level with a distribution of numbers equal to the square root of the number of assets at your facility. And lastly, people who are trained to be able to plan and schedule the work required to maintain your equipment.
Discipline – Last, but not least is Discipline! We must have the discipline to identify and complete the work we identify on a daily, weekly, monthly, and annual basis. And, we must stick to the principals of Reliability Centered Maintenance that say when a Potential Failure has been identified through Condition Monitoring, we will plan, schedule and replace the item before secondary damage occurs. Discipline in terms of RCM also includes the application of precision maintenance techniques when replacing failed items. We will from here on out take the time to make sure our rotating equipment is properly aligned and balanced, we will ensure our trades people have the proper training and tools to perform their jobs to the highest standards. Lastly, Discipline is sticking to the plan put together by your leaders. Its very easy to get excited about a good RCM program and the next thing you know someone is wanting to do twice as many RCM’s as planned and the next thing you know your up to your ears in tasks that need to be implemented. It’s important to remember, the work we identify and perform through RCM sets our organization up to be successful. So, if someone wants more, we will need the resources to do more.
Is RCM Blitz™ a shortcut RCM process?
No. RCM Blitz™ fully complies to the SAE RCM standards (JA-1011, JA-1012) meaning it follows the 7 step traditional RCM process
What makes RCM Blitz™ different from other Traditional RCM Methodologies?
When we look at traditional RCM methodologies, the 7 steps are identical. What we did to make RCM Blitz™ quicker and therefore more tolerable was to design a database that allows for live facilitation of the RCM process while simultaneously entering the information into each field. The database, which allows the user to upload ISO 14224 compliant asset hierarchy makes the transition from asset to component to Failure Mode seamless making the transfer of information from the RCM database to your CMMS much easier when it comes to implementation.
1. Would you explain, “A criticality analysis performed to the component level with a distribution of numbers equal to the square root of the number of assets at your facility. “? That’s interesting
2. How do you classify parts’ failure rate functions according to inpsection, monitoring, PM, repair, replacement, or nothing at all?
3. How do you classify failure rate functions a la Nowlan and Heap if parts are not tracked to get (a sample of) life data?