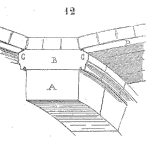
Decision Focus and Value
Last week I discussed how the aspects of the structure of an organization relate to product reliability. Related to that, this week the discussion will remain on the level of a reliability organization but will look at something a bit more intangible – how decision-making policy and practice affects product reliability.
Reliability Organization
An essential element of a successful reliability program is the notion that all reliability activity relates to decisions. If you are performing a HALT because it is listed in the product development guidelines, or because it was carried over from the last program’s plan, and the HALT results are not part of the design improvement decision-making process, then you probably should not be doing so. If the HALT results yield little or no information (e.g., it is just being checked off the list as accomplished), then the HALT itself provides little or no value.
If the performance of a HALT is on the plan because the new product has new materials, vendors, or design elements, then it may reveal weaknesses. If that list of weaknesses is made available to the design team members and they are permitted and encouraged to improve the design based on that input, then the HALT data can provide input to decisions about design improvements. The value that the HALT plays here is related to reduced field failures from design improvement opportunities discovered by such highly accelerated life testing.
If the HALT is done too late to permit any decisions to improve the product, it has no value. If the HALT is done to facilitate decision making concerning design improvements, it may have great value. [Hobbs 2000]
Another example of decision making is life testing to estimate the expected durability of a product. At some point in most product development processes, there is a meeting to decide whether the product is ready for production and shipment. One element of this decision is the ability of the design to meet or exceed product reliability objectives.
As an example, say a motor is the key element that will determine the life of the product and currently there is uncertainty concerning the motor’s expected reliability performance. Therefore the team decides to conduct an accelerated life test. If the test provides a meaningful estimate before the decision point on readiness, it adds value. If the ALT provides results a few months after products start shipping, it adds little value for the readiness decision before launch.
During product development or maintenance planning two basic questions are often asked:
- What will fail?
- When will it fail?
The various reliability tools provide information to address these two basic questions. If that information is meaningful and timely (before the decision point), then the reliability tasks have value. Performing reliability tasks simply to be doing reliability activities is unlikely to add value for decision makers. Purposefully using reliability engineering tools to support decisions is very likely to add value.
Leave a Reply