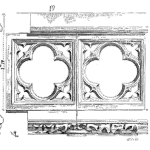
Reliability Role in Safety and Liability
The reliability engineer may have many roles within an organization.
You may be specialized and focused only on the analysis of field data. Or you may be a member of the organization’s strategic leadership team.
You might support one or more product development teams, or work with a team of reliability professionals supporting just one subsystem.
The actual work you do taps into your skills and abilities and it also expects you to consider the viability of the product or system as well.
You’re role spans beyond the specific tasks and includes your ability to ask questions and assist the entire organization or your local team to focus on what could go wrong.
We bring unique tools and techniques to the organization that enables decisions. Decisions concerning warranty, spares, and readiness of a design for production. We impact major decisions with our information.
Plus, we bring a balance and conscious to the team concerning the impact of potential failures.
Importance of safety
In many organizations, safety is the explicit top priority.
In other organizations, it is important when recognized. In any organization, the safety of the product in customer’s hands, or on their factory floor is paramount to the business and to us. Reliability engineers tend to focus on how items fail, which places us in the unique position to see the potential consequences of failures and how they impact safety.
If a consumer product has a battery charging system that causes a fire, it doesn’t take too many such incidents to cause a product recall or market rejection.
If a surgical tool shatters while in use, causing harm to the patient, that device is likely to not remain on the market. In each case, the breach of safety may have been isolated and rare events. The same holds for items that do not have as dramatic failures, rather cause near misses.
A product may have a 10% field failure rate per year and do just fine. Yet even a 0.01% safety incident rate may be too many events and force a recall or shut down.
Safety is important.
And, our role as a reliability professional includes identifying safety concerns and doing something about it.
The ethical role concerning liability
Given our position and duties as a reliability professional we are often asked to:
- Gather and analyze data, often focused on failures either in testing or in use
- Report or communicate the data and analysis so other may clearly understand the information
- Help decision makers fully understand the meaning, assumptions, and ramifications of the analysis
It is our moral duty to not distort or unduly influence the meaning of the data.
It is what it is and letting the data ’speak’ clearly is the goal of our analysis.
When there is a safety issue involved, we may have to make clear and convincing arguments for action to mitigate or remove the safety problem, which taps into our ability to first correctly analyze the data, and second to clearly communicate the results.
Working as a reliability professional, we often ask the right questions
FMEA – what are the potential failure modes, causes and what are we going to do to minimize, avoid, or mitigate the highest risk failures?
FMEA is a tool that allows the team to prioritize potential failure modes for attention. It allows us to work with our team to fully understand what could go wrong. Concerning safety, we should ask how each failure may initiate a chain of events that leads to a safety issue. For example, if the current limiting device on a battery charger fails, may that lead to overheating and ignition of the battery?
Design Reviews – Is the design ready given the range of potential environments, missions, and assembly/supply chain variations that are likely to occur? Is the design robust and thus unlikely to fail in a hazardous manner?
Design reviews often focus on the ability to achieve specific functions. The engineering teams may focus on design improvements concerning efficiency, elegance, cost or other priorities. The reliability professional may ask about robustness and how the design may respond to expected variation or abuse.
Suppliers provide components and subsystems for the product and provide unique ways the product may fail. If a supplier’s component fails will that create an unsafe situation? We need to understand not only how the supplied parts work within the system but also how the part’s failure impacts the system and the safety of the system.
Maintenance processes may include the overriding of safety panels, hatches, or other safety related devices meant to protect those operating or near the equipment from injury. How will maintenance activities change the ability of a product to cause harm? How will the equipment respond to overrides of critical safety features? How will the operating process change?
Consequence of failure involves thinking through how a failure may manifest. Do we have evidence that a material defect will result in a device being unsafe for use? If so, what are the controls and steps to prevent such defects? Our questions and investigations may help prevent latent defects from creating safety liability in the future.
How do we safely retire the product includes the decommissioning and disposal of the product or system. This may include the handling of hazardous materials, high energy storage cells, or other inherently dangerous devices as they become isolated from the system. The first concern is the safety of the team dismantling the equipment followed by the proper handling of environment damaging materials.
This is just a short list of quick examples of the types of questions and associated areas reliability professionals become involved in. It is clear we operate and influence decisions across the entire organization and lifecycle.
It is our responsibility to work and communicate clearly to help our entire team make well informed and ethical decisions.
Related:
Safety Factor (article)
The Liability Part of Reliability Engineering (article)
Leave a Reply