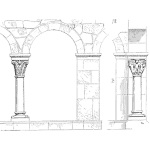
Resilience has been lost – and it’s our fault. We need to get it back.
As the Covid pandemic transitions to endemic (I am optimistic) we will get back to a “new normal”. No one really knows what the “new normal” will be like (yet), but it’s safe to say that it won’t be the same as the “old normal”.
After 22 months of Covid restrictions and uncertainty (and still counting) we are all a bit different. We haven’t been able to grieve lost friends and relatives, we haven’t socialized with friends or even family, we’ve lost income, we’ve lost businesses, lost homes, our mental health has been assailed, relationships are strained, addictions (alcohol, etc.) are increased, education has been delayed or stopped, and medical conditions are likely worse. Many resigned from their old jobs after being furloughed (or let go). Many more are working on their own in the gig economy.
After adapting to working from home, many see no need to go back. Office space will go unused, while commutes disappear or shorten and time lost traveling was regained. At work people adapted to new ways, distancing, fewer contractors, fewer (or no) visitors, etc. Some changes worked well and saved money, some just added stress and made things more difficult.
When people return to work they are not going to be the same. One client reports that his staff is very demotivated and “listless”. Many of us have “languished” and our spirit has been sucked out of us. It has happened before with other pandemics and eventually, we will all adjust, but in the short term, business and lives must go on.
Demotivated and demoralized people need a boost – we all do! One way that businesses can motivate employees is by showing that they care about their future. A way of doing that is with training and education. Help the employee learn and become better at their job and enhance their credentials. Training all but disappeared during Covid. Trainers moved content online in the hope that it would sell during times when they couldn’t get in front of classes. Uptake for online (self-paced) and live-virtual training has been slow, but it is growing. There are three price points: high (live face to face), medium (live virtual), and low (online pre-recorded). Training has never been a place where companies spend extravagantly. You can expect we will all need to get used to the lower-priced pre-recorded training that is now abundantly available. You can bet that will be a favorite among accountants who are forced to loosen up a bit and provide for at least some training.
Cost-cutting before Covid had trimmed fat from most businesses and their processes. Supply chains were lean as can be with just-in-time deliveries and “to the second” scheduling. Covid has been a wake-up call about excessive penny-pinching. With that fat went resilience. What happens to “just-in-time” when lead times double or triple? You need more on its way and you still need guaranteed delivery times. That problem will be slow to resolve. Until the whole planet is vaccinated and Covid is under control everywhere, supply chains will be disrupted. Those lower-cost sources of parts and materials that we love in the supply chain world are also in lower wealth economies where Covid will linger for longer. Moving sources from Asia to Mexico will work here in N America, but it will also take time. Resiliency will slowly recover.
Disrupted supply chains slow down everything including parts we may need for our repair work. If we can reduce the number of repairs, we can alleviate some of that stress on the supply chain. Of course, we need better reliability and that means better proactive maintenance programs. We can get smarter and help save ourselves a bit of trouble. As a bonus, perhaps the main driver for the smarter organizations, we also get added asset availability and with it, we get an increased ability to produce. That also helps anyone depending on our companies in the supply chain, provided we can get what we produce to our customers. Oh yes, fleets can also benefit from this same strategy.
Inflation is up and failures of our excessively lean supply chains are largely to blame. It needs to be fixed and the solution requires a multi-faceted approach. Supply chains can heal, they need better forecasting as well as more availability of transport. Forecasting for parts (maybe 80% of your purchasing effort even if the dollar value is low) can be dramatically improved but in-company spares, inventory management, and purchasing processes must be integrated with maintenance planning. Maintenance planning needs to be focused on the long term as well as the shorter-term jobs coming up. If your planners are still chasing parts for you, then you are way behind on this front.
Chances are that your planners need a bit of education on long-range forecasting. If you educate your maintainers and operators in reliability (basic stuff, not the math), then you can begin to get benefit from more proactive programs, more careful operation on systems, and better collaboration to keep things running.
Covid created a global problem. It’s not just medical – it has impacted just about everything and we need to think bigger and more holistically to solve the problems that will linger long after the virus has faded from its fear-inducing status!
Good post.