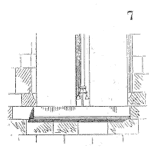
The “D” is 8D stands for “disciplines”, and the 8D process is a problem-solving methodology employing eight sequential disciplines or steps that can be applied to a wide range of industries, situations, and disciplines.
The 8D process was developed in the late 1980’s by the Ford Motor Company to give its engineers a standardized method for dealing with design and manufacturing problems. Ford’s predecessor to 8D was called “TOPS”, Team Oriented Problem Solving. This is a fitting name to the methodology since it strongly emphasizes a team-based approach. In fact, the first of the eight D’s is “Assemble the Team”.
The second D is “Describe the Problem”. As former president of General Motors, Charles Kettering tersely said, “A well-stated problem is half solved.” At this step of the process, the failure is analyzed, the data is collected, and the observations are made. This critical fact-finding phase sets the stage for the rest of the process.
The third D is the “Interim Containment Response”. These are the steps to “stop the bleeding”. Recalls, onsite sorting and 100% inspection typically fall under the umbrella of containment. In industries where a very high level of customer satisfaction is paramount, containment is often the most critical step in the process. While containment actions don’t fix problems, they do shield the customer from further effects of the supplier’s shortcoming.
The fourth D is “Root Cause Analysis”. This is where tools like capability analysis, the Ishikawa diagram, control charting, 5 Why Analysis, and Measurement System Analysis tie together the inputs of a process to the unintended outputs. By identifying the true root causes, your efforts moving forward to improve the process will yield your intended results.
The fifth D is “Determine the Corrective Action Plan”. This is the step where your understanding of the process, and your knowledge of improvement tools and strategies come together to permanently reduce or even eliminate the defect. It’s not good enough to just have a clear picture of the problem, you must have access to potential solutions as well. This access comes through experience, benchmarking, supplier support, established improvement strategies and a host of other sources.
The sixth D is closely related to the fifth, “Implement Corrective Actions”. Even though the corrective action for a defect is accessible, it may take different types of effort to implement the right solution. This is where project management techniques, soft skills, and networking pay off most in the 8D process. Negotiating, planning, training and communicating often complement the “hard” skills of problem solving to fully implement the solution.
The seventh D is “Implement Preventive and Parallel Actions”. This is where the hard work you investing into the first six D’s is multiplied by applying the same improvement across multiple product lines, machines or departments.
And lastly, the eighth D is “Thank the Team”. Successfully implementing a corrective action is truly a reason to celebrate and to acknowledge the contributions of others. It is common at this step to make a presentation of the improvement project to the executive team. Acknowledging others’ contributions also feeds the culture of continuous improvement and encourages those same people to take on new challenges.
A deeper dive into the 8 D’s, plus dozens of tips and tools like this are available in the online classes “Root Cause Analysis and the 8D Corrective Action Process”.
Leave a Reply