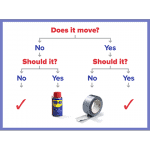
Addressing The Root Cause Of Failures Will Unlock The Potential Of The Business
You walk into the plant on Monday morning. You are immediately confront by the production manager stating “Press 201 is down. The mechanics are saying it is the clutch again.” You feel an overwhelming sense disbelief. You ran overtime last weekend and replaced clutch at a cost of $30,000. How is it the clutch is failing again?
This scenario may sound familiar. It happens all the time, across many different industries and plants. So what exactly happened? The root cause was not properly diagnosed, and the clutch was replaced. Based on the short life of the new clutch, the root cause was likely something else that is affecting the clutch.
So How Do You Determine The Root Cause?
By using Root Cause Analysis you can end the re-occurring issues that arise in your plant. Root Cause Analysis is used to determine the underlying cause or causes of a failure so that steps can be taken to manage those causes and avoid future occurrences of the failure.
Performing a Root cause analysis can be a quick simple task or a in depth difficult task depending on the complexity of the issue being addressed.
Levels of Root Cause Analysis
Organizations will typically have multiple levels of Root Cause Analysis based on the losses and impact. Depending on the losses and complexity of the problem, the Root Cause Analysis may be separated into the following levels;
- Level 1 – Typically performed by the operators on the line to address minor production issues.
- Level 2 – Typically performed by maintenance and operations to address minor failures.
- Level 3 – Typically performed by engineering, maintenance, operations and management to address significant failures.
Obviously, the people performing the Root Cause Analysis must be trained in the techniques of Root Cause Analysis. Additionally there are typically RCA champions which facilitate and assist with conducting Root Cause Analysis.
The Steps to Performing a Root Cause Analysis
So how does a team conduct a Root Cause Analysis? The steps to completing a Root Cause Analysis are quite simple. Yet, it is critical that each step is fully completed.
- Assemble a team; this may or may not apply depending on the complexity of the issue. But I highly recommend it for every RCA as having multiple sets of eyes on the problem will increase the likelihood of truly determining the root cause.
- Define the Problem; this is used to clearly define the issue and determine what is in scope. Typically you would ask certain questions to define the problem. These questions include; How often does it occur?; When & Where did it occur?; Who is affected by the problem?; What is the effect / impact on the company?; The outcome of asking these questions is a problem statement. The better defined the problem, the easy it will be to solve the root cause.
- Investigate and gather data; using the problem statement as a guide, go gather the data to properly identify the root cause of the issues. Gather factual information using the 5W-1H (who, what, when, where, which and how) framework. You can also use a fishbone diagram to assist with identifying possible causes and grouping them.
- Data Analysis; with all the data, we must determine what the root cause of the issue is. A 5-Why, a Fishbone Diagram or a Cause Effect analysis can be used to assist in analyzing the data (click the links to get both templates for free). Which one you choose to utilize depends heavily on the complexity of the problem. 5-Why and Fishbones can be used for the simple to mid complexity problems. A Cause-Effect analysis may be needed for the complex problems.
- Determine solutions; Now that we know the cause of the issue, we must determine possible solutions to the problem. Brainstorming is a great tool for this. At this point it is critical to come up with a variety of solutions to address the root cause. Cost, ease of implementation, etc. should not be a concern at this point.
- Choose the Best Solution; the solution should be chosen based on the cost to put in place, ease of implantation and effectiveness of the solution. Carefully weigh each of the criteria to select the right solution
- Implement; with the solution chosen, begin to put in place the solution. Whether the solution is updating procedures, or making changes to the equipment, the cause will not be addressed unless action is taken.
- Validate; after a predetermined time, confirm that the solution was successful in addressing the root cause of the issue.
Tools In Root Cause Analysis
I want to provide an example of two tools that greatly increase the effectiveness of the RCA process. These tools do not take the thinking out of the root cause analysis, but help the process
- Fishbone (Ishikawa) – is a tool that displays the various ways factors affect a situation. It breaks down root causes that potentially contribute to a particular effect. Each cause or reason is for imperfection is a source variation. Causes are usually grouped into major categories to identify these sources of variation;
- Man: Anyone involved in the process
- Method: How the process is performed and the specific requirements for doing it, such as policies, procedures, instructions, rules, regulations and laws
- Material: Material / parts used in the process
- Machine: Any equipment, computers, tools, etc. required to do the job
- Measurement: Data generated from the process that are used to evaluated it effectiveness or quality
- Environment: the conditions, such as time, temperature, and culture in which the process is completed
- 5-Why – is a structured approach to root cause analysis problems and applying corrective actions. The 5 whys is a cause chain, which is a natural logical progression for thinking through a problem. Generally it takes 5 whys to get to the end of the chain, but sometimes the root cause will be identified in 3, or 7. You continue until asking why until waking why provides no value to the prevention of reoccurrence. You should also be able to start at the root cause, and follow through the chain saying therefore after each of the contributing causes. If it does not make sense when you follow it upwards with therefore, there may be an issue one of the contributing root causes
Initiating Root Cause Analysis
When should a Root Cause Analysis be initiating? You should not wait until a failure occurs to determine if a root cause analysis should be complete and who will be responsible for it. The best organizations have pre-defined triggers established that state who will be conducting a RCA when a certain trigger is met.
These triggers may include downtime, quality issues or not staring up from a maintenance outage on time. Regardless what triggers are established, be sure to adhere to them.
Tracking Outcomes
In my experience, where most root cause analysis programs fail, is not in the training or the ability to determine the root cause. The failure in the program comes in implementing the recommendations from the root cause analysis.
To overcome this, all outcomes and actions from the root cause analysis should be tracked and reviewed regularly. This will ensure that none of the actions are missed and the root cause analysis program delivers results to the business.
Do you have triggers established to start a root cause analysis and who will be responsible for the root cause analysis? If not what are you waiting for?
Remember, to find success, you must first solve the problem, then achieve the implementation of the solution, and finally sustain winning results.
I’m James Kovacevic
HP RELIABILITY
Solve, Achieve, Sustain
Follow @HPReliability
Image by Brett Jordon Does It Move Chart
Leave a Reply