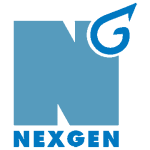
Root Cause Analysis (RCA) is a systematic process for identifying the underlying causes of problems and preventing their recurrence. An effective RCA not only resolves the current issue but also provides insights for improving processes and systems. This comprehensive guide explores the detailed steps involved in performing an expert-level RCA.
[Read more…]