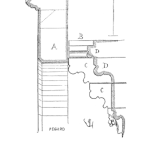
Favorite Questions and Answers from my Course “Statistical Process Control (SPC) Using Microsoft Excel”, Pt 1
Teaching manufacturing-related skills online offers a host of intangible benefits such as:
- Interacting with professionals around the world,
- Helping learners take the next step in their careers,
- Witnessing the “a ha” moments of the learners taking my classes, and
- Sharing the knowledge I’ve accumulated (and continue to accumulate) in my career.
And in one specific piece of the teaching process, I can experience all four benefits simultaneously, that is, answering student questions.
In this first article of a three-part series, I will share with you some of my favorite questions and answers from “Statistical Process Control (SPC) Using Microsoft Excel”, a course 7,800+ students from 126 countries have taken over the past since I launched it nearly 7 years ago.
Question:
“Hi Ray, I am bit confused does process range normally refers to the entire +-6 sigma or just +-3 sigma? I thought 6 sigma represents approximately 99.9999..%?” – Howard P.
Answer:
Hi Howard … Awesome hearing from you and thank you for taking my class.
As a general rule, the “expected range” for a process is its mean +/- 3*sigma. In other words, for a process output (weight, volume, length, etc.) that displays an underlying normal distribution, 99.7% of the observed values will fall within 3 sigmas of the mean. So a lot of people call the +/- 3*sigma range, the “typical” or “expected” process range. A +/- 3 sigma process also equates to a Cpk of 1.0.
But using the same raw data and summary stats, you could also calculate a +/- 4 sigma, +/-5 sigma, … range. Practitioners of the Sign Sigma management philosophy often refer to a range that roughly equates to a +/- 6 sigma process.
And for a process output that displays an underlying normal distribution, 99.99999998% of the observed values will fall within 6 sigmas of the mean.
One of the ideal goals of a Six Sigma Practitioner is to narrow the variation of a process (i.e. the standard deviation) such that +/- 6 sigmas from the process mean would fall within the specification limits. With a true Six Sigma Process, you would expect that about 2 parts per billion produced would be out of specification and the process would have a resultant Cpk of 2.0.
I sure hope this helps … best wishes to you in your studies. And let me know if I can be of any further assistance.
Question:
Hello Ray,
I want to carry out an MSA study on an automated measurement machine. This machine takes a finished brake discs, makes some measurements, and then it decides whether the disc is accepted or rejected. There is no human interaction with the machine and its feed comes from the line. Does this study differ than the normal R&R study where there is an inspector using a measuring device to measure the needed feature?
Answer:
Hello Ramy,
A R&R is not run on automated measurement systems. Without an operator, there is no reproducibility term to measure.
Nonetheless, you can study your equipment in other ways to determine the quality of its measurement output. Since it sounds like you work in the automotive or closely related industry, I would recommend you get a copy of AIAG’s “Measurement Systems Analysis” book. In it, they show you how to perform linearity, stability and bias studies.
Linearity is accuracy over the span of the gage. Stability is accuracy over time. And bias is a systematic shift.
I’ve seen people assign a “phantom” operator to automated gage R&R studies. But that’s a bad idea. Some amount of the error will be assigned to reproducibility even though there’s no logical basis for it.
I hope this helps. The book is a great resource for any quality engineer.
Question:
Hello Ray
I wanted to use control charting to analyze data for my wife’s store. The store is 4 months old and has a 10 – 15 % growth per month. I wanted to find out the UCL and LCL for the sales per month and if these are statistically within limit. Which chart should I apply to this case? Please suggest and let me know some tips to analyze this type of data. Thanks” – Bhuvanesh S.
Answer:
Hello Bhuvanesh … So glad to hear you’re looking for applications for control charting.
Here’s a point that’s important to remember whether you’re applying this to a manufacturing process or your personal finances:
You should only establish control limits for a process that is believed to be in control. In manufacturing, this means that the process settings are correct, the measurement system is adequate, the correct tools are in place, etc. After all, a control chart is designed to separate the “noise” common to any process from a change that occurs because of a specific cause. So if you know that a process is not stable, you’re not ready to establish control limits for it yet.
Now it sounds like your wife has a wonderful business going. But it is not stable since it is growing so rapidly. So a control chart is not quite the right tool for the job.
I don’t teach demand forecasting in this class because it’s not used much in quality. But in supply chain analytics, they talk a lot about “time series analysis” as a tool for forecasting sales. They usually break up demand into a few components: level, trend, seasonality and error. There’s a lot that goes into this, but the basic tool used to evaluate trend (such as growth in your case) is regression analysis. To get started with regression analysis, take a look at the last portion of this class where I teach the basics of linear and multiple regression.
Hope that helps.
Ray Harkins is the General Manager of Lexington Technologies in Lexington, North Carolina. He earned his Master of Science from Rochester Institute of Technology and his Master of Business Administration from Youngstown State University. He also teaches manufacturing and business-related skills such as Quality Engineering Statistics, Reliability Engineering Statistics, Failure Modes and Effects Analysis (FMEA), and Root Cause Analysis and the 8D Corrective Action Process through the online learning platform, Udemy. He can be reached via LinkedIn at linkedin.com/in/ray-harkins or by email at the.mfg.acad@gmail.com.
A few comments about the replies. On the first question, you did mention “assuming a normal distribution” but this really has to be stressed when equating “process range” to 6 sigmas as much industrial data is not normally distributed. Also, process range should reflect sampling uncertainty – so the concept of tolerance intervals should be used imo to provide a range along with a confidence interval that the range traps the stated percentage of the process. Also, equating Cpk of 1 to a process that consumes 6 std deviations and Cpk of 2 to a process that consumes 12 standard deviations only is correct if the process happens to be centered between the specification limits. This is often not true. Cpk does not correlate with the spread of the process because it depends on only the worse side of the process. On the 3rd question, trending processes can be used with SPC if the (predictable or expected) trend is modeled and then the center line and control limits follow that trend as well. These “trending” charts are commonly used in manufacturing to account for predictable changes due to tool wear, filter clogging, and other similar predictible changes over time on the process characteristic being monitored. The 15% expected growth rate in the example could be reflected into the center line and control limits – and then the chart would detect a sales growth that is more or less than expected.
Hello Steven, Thank you for your response. I’ve long admired your work in SPC.
I agree with everything you said regarding the first question. The challenge in answering these questions is in meeting the student where they’re at. The first student is trying to understand what “6 sigma” means. So I try to answer the question and give them a step or two ahead. But I try not to overwhelm them.
Regarding your comments on the third question, the context is demand forecasting not process monitoring. While I agree that traditional control charting could be adapted to his sales forecasting problem, there are time series analysis tools that are better suited to measure base, trend, seasonality and error. It felt like teaching him how to adapt quality engineering tools to fit his forecasting problem would circumvent where he needs to be.
Thank you again for your comments. All the best to you. Ray