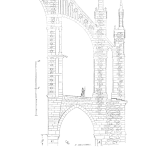
Favorite Questions and Answers from my Course “Statistical Process Control (SPC) Using Microsoft Excel”, Pt 3
In this third and final installment in this series, I continue my review of questions I’ve received from students of my online course titled, “Statistical Process Control (SPC) Using Microsoft Excel.
The length of the course is just under 11 hours, and covers a wide range of topics under four major chapters: Pareto Analysis, Control Charting, Process Capability Analysis, and Linear Regression. In it, I draw numerous case studies and examples from my career in quality management and manufacturing engineering. These real-life examples, I believe, are what spark the most questions. As the statistical approaches are placed in the context of plausible scenarios – scenarios the students routinely see themselves – the content takes a better grip and leads the student toward a greater desire to learn.
So please enjoy this last set of questions. Maybe they will inspire you as well.
Question:
“Hello Ray,
I appreciate the knowledge and experience you have shared in this classic! Well done.
You covered the foundation of linear regression and multiple regression as well in a very simple understandable way!
I would like to ask a question here. I have a new machine and I need to know the best settings for that machine and the best target, given that, I have 3 independents (variables) and 1 dependent (response). Is this experiment best done using multiple regression or DOE?
Thank you”
Thank you for your kind words, Adam. I am so glad to hear you’re enjoying the SPC class.
This sounds like a classic application for a DOE where your 3 independent variable (or factors) are given two levels (high and low) and you end up with 8 experiments (or treatments).
Multiple regression is great for establishing quantitative relationships between variables. But regression alone isn’t good at picking up the effect of independent variables interacting to create a unique effect in your dependent variable, nor does it provide guidance how to design your tests that create the data for regression.
Hope that points you in the right directions. Take care,
Question:
How do you calculate a global Cpk when you have many Cpks of the same part/piece?
Alexis
Answer:
Hello Alexis,
Thank you for reaching out. I think I understand your question.
Cpk applies to a feature, not an entire part. In other words, if a part has 5 features, then you could generate 5 different Cpk’s for that given part. And because of processing methods and print tolerances, you might have some Cpk’s that are very high and others that are very low. In fact, this is a common scenario. But there is no global Cpk for a part.
I hope this helps. And feel free to reach out again if you’d like to discuss this in more detail.
Question:
Hello Ray! You’ve mentioned that we can use the SPC tools to analyze product outputs and process outputs. So, can we analyze the process inputs too? if not, can you please explain why?
Ahmed
Answer:
Hello Ahmed,
I usually refer to applying the various methods of SPC to process outputs because they are dependent on the process inputs. For instance, the size of an injection molded part is dependent on the combination of many inputs like tooling, material properties, process temperatures, ambient conditions, etc. These inputs, while they can and do vary, are regarded as fixed in a process design. Yet they combine in various ways to create the process output.
A typical process input is a machine setting. In metal cutting for instance, inputs include material feed rates and spindle speed. Again, while these may vary slightly in the machine itself, they are fixed in the process design.
One scenario in which you might apply SPC methods to an input is in analyzing the raw material you feed into your process. For instance, you may have a receiving inspection process where you sample a thermoplastic resin upon receipt by measuring its melt flow rate. Of course, you can chart MFR over time, analyze it in various ways, and perhaps even optimize your injection molding process around that MFR. And while this would an SPC analysis of a process input, it’s also the output of some other process.
So generally speaking, you set inputs and analyze outputs.
Thought provoking question.
Question:
“Hello Ray! First thing I want to tell you is that I love your course :). Secondly, I was asked in an interview, if your Cpk is 1, what is your sigma? I got confused since I don’t get the exact connection since Cpk involves sigma hat, which depends on the R and d2.
The interviewer did not give me USL/LSL values also. Can you please tell me how to approach this question or if the question makes sense to you?” – Varun M.
Answer:
Great hearing from you, Varun.
First, don’t get hung up on the difference between sigma and sigma-hat. Both are measures of dispersion. Sigma is the same as standard deviation, and sigma-hat is an estimate, or your best guess of standard deviation given the available data.
Next, all capability indices (Cp, Cpk, Pp and Ppk) are essentially ratios between the Specification Range and the Process Range. In other words, Capability = Spec Range / Process Range. So if the capability index = 1, then you know that your numerator and denominator are equal.
The Process Range in manufacturing is generally defined as the width of 6 sigmas (or sigma-hats, doesn’t matter). A range of 6 sigmas in a normally distributed process accounts for 99.7% of the population.
So if your Cp (or Pp) were equal to 1, its means that your process range is the same width as the spec range. However, these indices do not account for the centeredness of the process like Cpk and Ppk do.
Cpk and Ppk consider the centeredness of the process by looking only the specification limit closest to the process mean. For example, if your process range is shifted toward the USL, then Cpk (and Ppk) uses only the USL in its calculation.
So since Cpk and Ppk use only the spec limit closest to the process mean, the formulas only considers half the process range, or the 3 sigmas on the side of the curve closest to a specification limit.
One of the main purposes of capability analysis is to estimate the probability of a defective part. So if a curve is shifted to one side, surely the process is more likely transgress the closer of the two specification limits.
So, to calculate the Cpk of a process shifted toward the USL, you use the formula:
Cpk = (USL – Process Mean) / 3 sigma.
If a process has a Cpk of 1, it means that one of the process limits is just barely touching one of the specification limit (i.e. exactly 3 sigmas away).
Therefore, since the normal curve is symmetrical by definition, the opposite side is 3 sigmas wide as well, resulting in a process range +/- 3 sigmas wide, or a total width of 6 sigmas.
I know that’s a lot of information is a dense spot, but there is your answer. And in the Process Capability section of my SPC class, I slow down a bit and explain this concept in greater detail with plenty of examples.
Thanks so much for the tough question. Best wishes to you on your job hunt.
Ray Harkins is the General Manager of Lexington Technologies in Lexington, North Carolina. He earned his Master of Science from Rochester Institute of Technology and his Master of Business Administration from Youngstown State University. He also teaches manufacturing and business-related skills such as Quality Engineering Statistics, Reliability Engineering Statistics, Failure Modes and Effects Analysis (FMEA), and Root Cause Analysis and the 8D Corrective Action Process through the online learning platform, Udemy. He can be reached via LinkedIn at linkedin.com/in/ray-harkins or by email at the.mfg.acad@gmail.com.
Leave a Reply