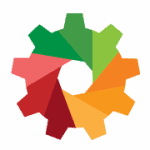
Emergency maintenance is the maintenance required when an asset suffers an unexpected functional failure. Typically, such failures can halt production lines and disrupt business operations until fixed.
Emergencies almost always happen without prior warning, and hence emergency maintenance is not one that can be preemptively scheduled – but it can definitely be planned for and efforts made to reduce its business impact when they do occur.
Examples of emergency maintenance:
Before we review a few examples of emergency maintenance, let’s first clarify some common points of confusion. The notion of emergency maintenance is often confused with other types of unplanned maintenance. Of them, the most common mix-ups happen between emergency maintenance and run to fail maintenance.
Run to failure maintenance is one where asset owners have consciously made the decision to allow a piece of equipment to run until it breaks down. It is a strategy commonly used on non-critical assets that are quick and easy to repair, have short lifespans, are not designed to be repaired, or a conscious decision has been made to wait for failure and replace at that point. In general, this equipment has a lower business impact of failure.
The following are three common scenarios that can trigger emergency maintenance:
- Health and safety risk. When a maintenance issue is observed that threatens worker or public health and safety. Some examples of this include effects of extreme weather effects such as flooding near an electrical system, or failure of major machine guards exposing public or workers to hazardous moving parts.
- Production stoppage. This includes critical equipment failure that can halt production lines or bring a whole plant down. For these types of emergency failures, it is best to reduce the probability of occurring by having multiple barriers to failure.
- Fail-Safe/Safe-State System Failures. This is the case when systems are shut down to prevent the failure of more sensitive connected systems, such as when sections of a power grid is shut down to prevent cascading failure effects across the larger grid.
Effective emergency maintenance management
The best strategy to ensure that your plant and maintenance and operations team are set up for success is by minimizing the probability of emergency maintenance in the first place. This can be achieved through an effective planned and scheduled asset maintenance strategy. It can take the form of preventive maintenance (PM), condition-based maintenance, predictive maintenance, or even prescriptive maintenance. Planned and scheduled maintenance strategies, such as these, proactively address deficiencies through the repair of asset before a catastrophic failure occurs.
The second strategy is to ensure that when and if emergency maintenance is needed, you have a plan in place to respond to it. The top priority should always be ensuring worker and public health and safety. Once that has been ensured, the next courses of action require an easily accessible information repository for the asset as well as a detailed task list that helps maintenance technicians resolve the failure as swiftly, effectively, and safely as possible.
Both these strategies can be effectively implemented by a CMMS platform.
Tackling emergency maintenance with CMMS
Below are some of the ways a CMMS can help your organization in streamlining emergency maintenance through failure prevention as well as maintenance management.
#1) Reducing failure probability
When your organization uses CMMS to schedule and track PMs, you will reduce the probability of emergency equipment failure and unexpected production stoppages. This cuts labour overtime costs for emergency repairs and significantly reduces production losses, giving your business a much-needed bottom-line boost and help hit those key KPIs such as OEE and TEEP. You can also plan equipment maintenance proactively in line with the production plan.
#2) Inventory and spares tracking
One of the biggest contributors to delay in repairs is parts unavailability. Especially, for custom parts that are not off-the-shelf, lead times can range from anywhere between 4 weeks to up to a year for long lead specialized items. A CMMS platform can track critical spares for critical assets and ensure spares are automatically ordered when re-order points are triggered, minimizing purchasing overhead costs as well as reducing the time it takes to repair the asset and return it to service.
#3) Centralized database
A CMMS serves as an integrated and unified source of information for all your plant assets, including previous maintenance history, parts information, as well as reference documents needed for repair. A centralized consolidated system such as this delivers substantial savings in the form of time saved and planning the emergent work when it does occur.
#4) Resource management
Most CMMS platforms can also help plan for emergent repairs by assessing labor hours required based on prior maintenance history or work task details. For mission-critical systems, this helps maintain a minimum compliment staff headcount to ensure that if and when a failure occurs, it can be tackled expeditiously. Additionally, it allows better work management prioritization in terms of knowing what other maintenance work in the plan may have to be delayed when an emergency maintenance work has to be executed in short notice.
Conclusion
Of all the different types of maintenance, emergency maintenance is the one type that you hope to never need. Although a more robust PM program will help your organization minimize the risk of an emergency repair, a CMMS can also help minimize the effects of a shock response when an emergency failure does happen.
Like most successful investments, the benefits of a CMMS compound over time. As your data becomes more comprehensive across your asset fleet, your organization will become more efficient in asset management and that is when the ROI climbs.
Leave a Reply