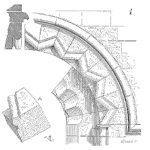
One of the weak areas in designing parts is deciding tolerances of various parts. We have shared a video of statistical tolerancing for assembly of parts. Many viewers have expressed that we should also post a video of application of Monte Carlo Simulation for tolerance design when there is a transfer function that relates the input parameters to an output variable. We therefore present in this video an application example of designing tolerance for a helical spring using Monte Carlo Simulation. The video explains this procedure step-by-step using Simular software. I have used Simular software to demonstrate this with a practical example of spring. Simular is a free software (emailware) which can be downloaded from https://www.simularsoft.com.ar/. However, one can use other software such as Crystal Ball, @Risk etc. for such analysis. Tolerance design is usually an essential step in Design for Six Sigma (DFSS) projects.
[Read more…]