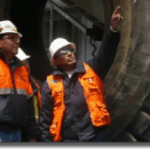
Welcome to part nine of my 10-part series of blogs called “Uptime Insights”, where we explore a journey of excellence in maintenance. To stay on top, managers must implement strategies that keep operations performing at high levels. In these articles I will show you how to achieve excellence in maintenance – a critical business process in any capital intensive industry.
Uptime Insights Part Nine:
Teamwork Produces Superior Results
There’s an old saying that, “two heads are better than one”. Teamwork has been proven time and again to produce superior results. It is the basis for many successful methods like RCM, PMO, RCFA, Total Productive Maintenance (TPM) and various quality improvement programs like Six Sigma. The importance of your people has already been stressed part 2. Choosing excellence goes beyond that – the use of self organized teams brings the best out of your people, delivers enhanced productivity and superior results.
Smaller teams tend to be more effective than larger ones provided they have sufficient breadth of depth of knowledge within the team for its various tasks. When teams grow into large groups or departments they begin to need more formal management structures and processes in order to remain effective. If you’ve got a group that’s larger than 150 people you’ll find formalized approaches necessary but below that number a degree of informality works well. Some organizations are even based on this figure, keeping the number of people in an operational unit (e.g.: a plant) below that number. One of the reasons for success of small teams and less formal organizations is that they don’t rely on “command and control” to get things done. Command and control tends to stifle initiative and creativity and that can harm productivity.
Total Productive Maintenance (TPM) is a team-based approach to organizing and working that has proven highly successful in a variety of industrial environments. Similar to quality approaches, it emphasizes teams of operators and maintainers working together and caring about their job so that they are committed to the team’s success. From that flows overall success of the organization. The use of small teams is one of the distinct features of TPM. Operators and maintainers work together towards the same goals having common performance measures and methods. The traditional work boundaries tend to blur between them and extensive training is used to help maximize flexibility and capability while remaining safe. The teams are allowed to operate autonomously, responsible for their own decisions and results in support of overall plant or operational goals.
To optimize the value of your employees’ input to your company, use teams. TPM is an excellent approach that works well in the production environment blending maintenance and operations into autonomous self-directed teams achieving superior results. TPM provides a framework for those teams to really achieve.
In our next blog we’ll explore the final part of our 10 part series “Uptime Insights: Process Optimization.”
To learn more visit Conscious Asset where you will find training, workshops, books, and resources.
Leave a Reply