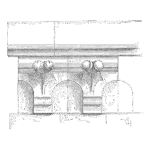
Plan Your Reliability Testing with Intent
I wonder how many product tests have been undertaken and nothing has been done with the results? Maybe development activities have moved on before any results are available? Maybe the test results didn’t provide the answers that were needed? Maybe the test wasn’t focused on the critical issues. In other words, cost, time and resources were wasted.
I will present a better way to ensure value is delivered and test results are acted upon.
Finding the value in testing
Testing is costly, takes time and consumes resources. Therefore, as a starting point, any test has negative value. Not a good place to start!
Instead we should start our test planning with an examination of what we want from the testing. We should consider:
- Need and opportunity for product improvement: e.g. –
- Find performance limits
- Find weak-points
- Need and opportunity to quantify and gain assurance of reliability: e.g. –
- De-risk program
- Satisfy regulatory requirements
And, of course, we need to confirm that testing is likely to be the most cost-effective means to satisfy these objectives.
Remember always to ask “Why test?” – maybe the answer is “don’t test”.
But, assuming that testing is a potentially cost effective approach, we can declare not only what the objectives will be, but also, with some additional discussion, quantify when results need to be delivered, to whom, and even elicit what will be done with those results.
In other words, the start of our test planning process is to examine who wants the results and what they will do with the results.
This is the positive value that reliability testing delivers.
Let’s accentuate the positive!!
Link testing with the positive
So, we now have a clear understanding of our desired outcomes and when they are needed. But these outcomes are not necessarily defined in testing terms. We need to identify what kind of test results would best enable the project outcomes we want.
Which failure modes or environments are linked to the desired outcomes?
Would “nil failures” be a positive outcome, or is “failure generation” a better outcome?
We may be “experts” in reliability testing, but our audience is not. So it would be a great idea to explain, and to include this explanation in the test plan.
Design the test to deliver the positive
Deliver the results in time! Deliver the results with feasible resources! Optimize in order to maximize the positive! And show how this is achieved.
Of course, I hope that you won’t drop a finished test plan on the project manager’s or design engineer’s desk as a “fait accompli.” Remember that we want their buy-in! We should include them in the test planning process.
It’s much better to take a set of alternatives, and to discuss feasibility, strengths and weaknesses. And to then agree the best course of action. This will be the optimized test plan – it is SEEN to be optimized, as well as actually being optimized.
Paying the cost
Every test costs, needs resources, takes time. But, by starting with objectives, discussing how best to achieve those objectives, we have testing that has ownership, is being undertaken with purpose, and has its resources agreed. We no longer have a costly test plan, but a justified cost-benefit.
Action is much more likely from a test plan developed, documented and conducted with this viewpoint. I wish that more test planning were undertaken with this approach.
This approach will help you to get the most from your test plans
What is your experience?
I would like to hear from you. How have you accentuated the positive? How have you gained buy-in and ensured positive usage of test results? What is your test planning process?
I believe a test plan should be more than a definition of the test environment, duty cycles, sample size, etc. It is a project document, and I believe it should exhibit project leadership.
Please contact me via my Contacts page or my website www.lwcreliability.com. I have a template that gives further definition of what I believe should be included in test plan document.
Leave a Reply