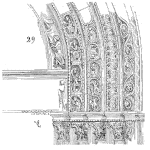
In today’s competitive business landscape, ensuring the reliability of products is paramount for any company aiming to maintain a strong market presence and satisfy customer expectations. One essential tool that plays a pivotal role in achieving this goal is Advanced Product Quality Planning (APQP). Understanding the major components of APQP and how it is intertwined with reliability provides design and engineering professionals with a framework for assuring early success in a product launch.
What is APQP?
Advanced Product Quality Planning, commonly referred to as APQP, is a structured and comprehensive framework used in manufacturing to develop and deliver high-quality products while minimizing risks and ensuring customer satisfaction. It is a systematic approach that assists organizations in planning, designing, and producing products that meet or exceed customer expectations.
APQP consists of several key phases, which include:
- Planning: In this initial phase, organizations define the project scope, objectives, and critical requirements. They establish a cross-functional team to ensure all aspects of the product development process are considered.
- Product Design and Development: During this phase, the focus is on creating a robust product design that aligns with customer needs and regulatory standards. Risk analysis and mitigation strategies are put in place to identify potential issues early on.
- Process Design and Development: Here, organizations develop and validate the manufacturing process required to produce the product. Process control plans and quality control measures are established to ensure consistency and reliability.
- Product and Process Validation: In this phase, prototypes are rigorously tested, and the production process is validated to ensure it can consistently produce products that meet quality standards.
- Feedback, Assessment, and Corrective Action: Continuous improvement is a key aspect of APQP. Organizations gather feedback from the market and internal sources to identify areas for improvement and implement corrective actions.
The link between APQP and product reliability is profound. APQP’s structured approach ensures that the product development process is meticulously planned, monitored, and controlled, leading to higher levels of product reliability.
APQP contributes to product reliability in the following ways:
- Early Identification and Mitigation of Risks: Through risk analysis and mitigation strategies, APQP helps organizations identify potential issues in product design and manufacturing processes. By addressing these issues proactively, the likelihood of product failures or defects is significantly reduced.
- Robust Design: APQP emphasizes designing products that not only meet customer requirements but also have built-in reliability. This includes selecting the right materials, considering environmental factors, and optimizing performance, all of which contribute to product longevity and dependability.
- Consistent Manufacturing Processes: The process design and development phase of APQP ensures that manufacturing processes are well-defined, repeatable, and capable of producing products with consistent quality. This consistency directly impacts product reliability, as variations in the manufacturing process can lead to defects or failures.
- Validation and Testing: APQP mandates rigorous testing and validation of both the product and the manufacturing process. This thorough validation process helps identify and rectify any weaknesses or vulnerabilities before the product reaches the market.
Consider the automotive industry as an example of how APQP and product reliability are closely intertwined. In the automotive sector, safety and reliability are of utmost importance. For the automotive manufacturers proceeding with their new lines electric vehicles (EVs), APQP is one of the major tools that will keep them on track for producing safe, reliable, and full functioning EV’s on a timely and cost-effective basis.
By implementing APQP, manufacturers ensure that every step of the product development process is meticulously planned and executed. During the planning phase, companies define safety and reliability as top priorities. In the design phase, advanced engineering techniques are used to create robust EV platforms with redundant systems for critical functions.
The manufacturing processes are carefully designed and validated to guarantee the consistency and reliability of EV components. Comprehensive testing, including extensive real-world simulations and durability tests, is conducted to identify and address any potential issues. Customer feedback is continually collected and used to improve product quality.
As a result of following APQP principles, automotive manufacturers can successfully launch EV’s or any new product with exceptional reliability, safety, and customer satisfaction. By promoting systematic planning, robust design, consistent manufacturing, and rigorous validation, APQP helps organizations of all types deliver products that not only meet customer expectations but also stand the test of time, ultimately enhancing their reputation and competitiveness in the market.To learn more about APQP, PPAP, Root Cause Analysis or a range of quality, reliability and manufacturing topics, reach out to me on LinkedIn at linkedin.com/in/ray-harkins or by email at the.mfg.acad@gmail.com. I earned my Master of Science from Rochester Institute of Technology and his Master of Business Administration from Youngstown State University, and teach through the online learning platform, Udemy.
Leave a Reply