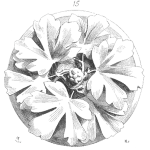
If you have attended any Maintenance and Reliability conference in the last several years, chances are you have seen a presentation on the struggles of RCM implementation. Most present that over 70% of companies who attempt to get started with Reliability Centered Maintenance fail to implement the recommended mitigating tasks identified in their analysis.
While I don’t dispute these numbers, I can tell you the reason most companies fail to implement, is they have never used a methodology and tool that was designed to simplify RCM Implementation. In my first years working as an RCM Practitioner, Trainer and Consultant, I tried to address this issue by creating a contract for the team and managers to sign that clearly stated who would be responsible for implementation. While this improved the number of our RCM’s that got implemented to just over 50%, several RCM’s were not being implemented.
To understand why our customers would leave the opportunity of improvement sitting in a computer waiting for someone to take the initiative to act, we went back to talk with those who had failed to implement. While those who failed to implement had a number of excuses as to why they had failed to act, the specific causes associated with failing to implement were;
· They didn’t know where to begin (No one had showed them how)
· RCM Analysis data did not align with their CMMS
Addressing these causes, we revised our process and program to simplify the implementation phase of Reliability Centered Maintenance. As a result, our customers implementation rate is now 95%.
How did we accomplish this? We started by listening to our customers and by doing the following;
1. We developed an RCM Database/Program that allows our customers to use their CMMS hierarchy to build the component registry. Matching hierarchy simplifies the transfer of tasks form the RCM Database back into the CMMS.
2. We developed an implementation report that clearly organizes RCM tasks by task type, required trade and interval simplifying the process of building PM, PdM, Failure Finding and Operator Care Tasks.
3. We built an interactive implementation report that allows customers to assign, track and report implementation progress.
As a result of our actions has cut the time it takes to implement the PM, PdM, Failure Finding and Operator care tasks from an average of 3 weeks (120 hours) to just over 1 week, (52 hours). In this year alone, we have worked with 9 different companies and 20 of the 21 RCM’s completed to date have implemented.
Being successful with RCM isn’t difficult when you work with a company that got its start by working to make RCM easy. If you’re interested in learning how to introduce as successful RCM program, please feel free to give us a call!
Douglas Plucknette is the President of Reliability Solutions Inc. and creator of RCM Blitz™. The author of Reliability Centered Maintenance using RCM Blitz™ and Clean, Green and Reliable a best-selling book on how to reduce energy consumption in manufacturing plants through equipment reliability. Doug has published over 100 articles on Maintenance & Reliability and has been a featured Speaker as well as Keynote Speaker at a countless number of conferences around the world. 585-329-7040
Leave a Reply