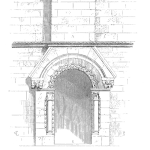
Co-authored by Mike Vella and Ray Harkins
How many times have we heard that we must tolerate poor process performance because it’s “the nature of the beast” or its excess variability is considered “normal”? How much does financial performance suffer due to allowances for alarming levels of scrap, low yields, or losses considered “best practice” for the industry? Improving these situations requires a great team, supportive management, and cooperative suppliers. Beyond the support, operations and quality leaders must know a systematic method of problem-solving and have access to statistical tools to drive the data through to a solution.
Those in manufacturing operations and quality are likely familiar with structured problem-solving methods such as the 8D method or DMAIC (Define, Measure, Analyze, Improve, and Control). No matter the method, the intent is to address “cause-unknown” problems and drive continuous improvement. A well-led and well-trained team will discover the root cause of a problem, contain defectives, take action for permanent corrective actions, verify changes as effective, and implement systemic process controls for meaningful improvement.
Statistical analysis is often seen as a set of mathematical tools and techniques used by specialists for maintaining process control, making data-driven decisions, and improving quality and productivity through experiments. Combining Structured Problem Solving and Statistical Analysis forms a powerful duo for problem solvers. In 8D/DMAIC, team members define the problem, measure its parameters, discover its source, and permanently fix the issue. Just as a good mechanic needs diagnostic tools and methods to collect vehicle performance data, industrial problem solvers need statistical tools to identify process variables that have shifted or determine the proper level of a critical process variable. These statistical tools fall into three groups: Diagnostic, Process Control, and Experimental, all providing the statistical power to get the job done.
Diagnostic Tools
Diagnostic Tools help determine the cause of a quality or performance problem. The objective is to identify the root cause: “the single, verifiable reason for the problem, which if corrected, prevents its recurrence.”
- Flow Charts are pictorial representations of process flow, describing all steps, including receipts and storage of materials. Especially useful in team settings, Flow Charts document the process and often reveal non-standard or alternate steps that may add unwanted cost and variability.
- Check Sheets are forms used to collect process information, answering the question “how often is a certain event occurring.” Data from Check Sheets is often used in other problem-solving tools.
- Pareto Charts follow the 80/20 rule, using vertical bar graphs to show categories of interest. They lead problem solvers to pursue the most promising categories, often using data from Check Sheets.
- Cause and Effects Diagrams, also known as Fishbone or Ishikawa diagrams, help teams brainstorm potential causes of a problem. The “bones” of the diagram, often categorized into the “5 M’s”: Manpower, Material, Methods, Machinery, and Mother Nature (environment), help identify and test potential causes.
- Run Charts visually describe process data over time, such as yield or scrap rate. They illustrate important changes in a process, providing insights into shifts in process center or swings of variability.
- Histograms graphically represent process data in bar graph format, showing measurement data and illustrating a static view of the process. They indicate central tendency and distribution width, useful for understanding variability.
- Scatter Diagrams study potential relationships between variables, plotting data points to show the strength of relationships. If a pattern shows promise, further analysis can be done using Regression Analysis.
Process Control Tools
Process Control Tools monitor and control processes on an ongoing basis. Before use, gauge error should be assessed using Measurement Systems Analysis (MSA) to ensure accurate data collection.
- Statistical Process Control (SPC), developed in the 1920s, is widely used in industry. Average and Range Control charts help understand and control variables, while Fraction Defective control charts are used for attribute measures. Process data is collected over time, and statistically derived control limits are applied. A state of statistical control exists if variation falls within certain limits, indicating the process operates with only random variation.
- Quality System Control Plans describe methods for controlling and evaluating process performance, including measurement methods, frequency, documentation, limits, and appropriate reactions if limits are exceeded.
Experimental Tools
Experimental Tools allow Research and Development, Engineering, Quality, and Operations to make statistically valid decisions about process variables and optimal settings.
- Hypothesis Testing determines if data supports a predetermined hypothesis. Depending on data type, a test statistic is calculated and compared to critical values. Common tests include the Z-test and t-test, and Analysis of Variance (ANOVA) for evaluating group mean differences.
- Regression Analysis estimates parameters of an equation relating variables. The resulting regression equation helps understand relationships, typically plotted on a graph with a line of best fit.
- Correlation Analysis discovers relationships between variables, indicating the strength and direction of the relationship. Positive correlation means variables increase together, while negative correlation means one increases as the other decreases.
- Contingency Analysis evaluates relationships in attribute data, determining if observed responses match theoretical expectations.
- Designed Experiments (DOE) determine relationships between factors affecting process output. Full Factorial designs test all possible combinations of factor levels but can be expensive. Fractional Factorial designs, simplified by R.A. Fisher and popularized by Genichi Taguchi, reduce experimentation costs while maintaining effectiveness.
Leaders Solve Problems
Operations and quality leaders solve problems, reduce costs, and improve quality by engaging well-trained teams using structured problem solving and supported by statistical tools.
By integrating structured problem-solving methods with robust statistical tools, operations and quality leaders can systematically address process issues, drive continuous improvement, and achieve significant cost savings. This synergy not only enhances product quality but also ensures a more efficient and reliable production process. In today’s competitive market, mastering these techniques is essential for any organization striving to excel in manufacturing excellence and operational efficiency. Through the dedication of well-trained teams and the strategic application of these powerful tools, organizations can transform variability into opportunity and turn process challenges into pathways for success.
Ray Harkins is the General Manager of Lexington Technologies in Lexington, North Carolina. He earned his Master of Science from Rochester Institute of Technology and his Master of Business Administration from Youngstown State University. He also teaches manufacturing and business-related skills such as Quality Engineering Statistics,Reliability Engineering Statistics, Failure Modes and Effects Analysis (FMEA), and Root Cause Analysis and the 8D Corrective Action Process through the online learning platform, Udemy. He can be reached via LinkedIn at linkedin.com/in/ray-harkins or by email at the.mfg.acad@gmail.com.
Mike Vella is a retired quality and operations leader, most recently serving as Senior VP Operations at the Suter Company and prior, Vice President and General Manager of TI Automotive’s Brake and Fuel Group in North America. Mike was with TI Automotive for 30 years. Mike received his MBA from Wayne State University and his BS from Western Michigan University. His contributions to the Manufacturing Academy include training courses focused on leadership, quality, problem solving and statical analysis.
Leave a Reply