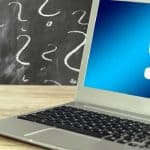
At its core, maintenance software is a tool that allows you to generate and schedule work orders and get the right people to do each job. Maintenance software automates paper processes by enabling people to create requests for maintenance work. Maintenance workers then enter the requests into the computerized maintenance management system software (CMMS), which generates the work orders. However, when it comes to the functions of a CMMS, work order generation is only the tip of the iceberg.
Today’s CMMS systems offer powerful features that earlier systems didn’t have and help you manage a wealth of data. Modern CMMS systems are capable of accommodating hundreds of users across multiple sites. They can be used to manage purchasing and budgeting activities as well as labor and equipment. Some of the benefits of preventive maintenance software include the following:
- Gather data for certifications or to meet regulatory guidelines
- Keep tight control of your spare parts inventory
- Determine the value of your preventive maintenance program
- Make equipment repair/replacement decisions
- Implement a predictive maintenance program for your most critical assets
Obtaining Meaningful Information from Your Maintenance Software
Organizations that only use their CMMS as an electronic work order system are missing out on the true benefits of the software. Maintenance software allows you to capture and analyze important data, impacting key business decisions that involve maintenance. Data can be extracted by a CMMS and measured with user-defined metrics to manage assets and resources more effectively. Metrics can reveal things like whether your maintenance strategy is effective, the number of hours spent on reactive maintenance versus proactive maintenance, and the costs of equipment failure.
The first step in obtaining meaningful information from a CMMS is to define your organization’s objectives. Then you can configure the CMMS and implement data-entry requirements to provide important data that reflects progress toward your goals. Some attributes you can use to organize your data with maintenance software include the following:
- Work priority
- Asset type
- Asset group
- Failure codes
- Work type
When configured in a manner that supports your objectives, a CMMS can be used to document and analyze your organization’s work history, helping you identify and understand the causes of equipment failure. The data you gather can have a major influence on your maintenance strategy and aid you in making more informed decisions. A business intelligence dashboard may be used to deliver timely information about key performance indicators (KPIs), and KPI reports can be created and shared with all levels of decision makers.
Whether you’re investigating why a particular piece of equipment failed or you want to measure, analyze, and improve your maintenance strategy, you need access to data. Properly implementing and using maintenance software can provide you with the information needed to make key business decisions, improve the effectiveness of your preventive maintenance activities, and cut costs.
Sign up for a free trial of DPSI’s maintenance software to discover how it can increase the efficiency of your maintenance and reliability program.
Leave a Reply