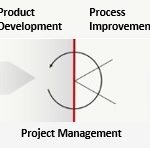
A complex production process requires a mixture of leadership, governance and management. In this article, we’ll discuss a tiered meetings structure that can effectively enable this. Empowerment, escalation paths, accountability and responsibility are included as some key ingredients. We’ll start with the following diagram:
Production Floor Team Meeting (Tier 1): the production supervisor (or manager) holds a daily meeting to resolve production issues (ideally) within the “shop floor” reporting structure. Production issues are resolved directly by team members to the maximum extent possible. Complex issues can be escalated to the production support core team. Generally, the meeting would be held at the start of each shift (or during shift changes) with the goal of resolving issues in preparation for the day (or shift).
Production Core Team Meeting (Tier 2): the production core team meeting is called by the operations project manager (Ops PM), but is primarily lead by core team leaders (CTLs) for their respective areas of expertise. The Ops PM is responsible for keeping KPIs up-to-date, collecting information from production supervisors, facilitating the meetings, documenting action items or assisting with project schedules for more involved root-cause corrective action projects. CTLs are the (functional) technical leads depending on the production problem that needs to be resolved (quality, engineering, manufacturing process, etc.). Extended team members are expected to be responsive to the needs of the CTLs, and provide the expected deliverables required to resolve the issue(s).
The CTL and Ops PM also communicate the demand for functional resources to functional managers. The functional managers may have constraints and communicate these constraints back to the core team. If additional resources or skillsets are required, the escalation path is to the (Tier 3) steering committee meeting.
Production Steering Committee Meeting (Tier 3): The Ops PM facilitates the weekly meeting and presents production key performance indicators to a committee of functional managers and the chairperson. The CTLs present the status of production issues which they are responsible. The steering committee chairperson keeps meetings efficient and effective, resolves issues and has the ultimate accountability for production performance. The goal of the meeting is to provide the CTLs the support they need to be successful, the primary levers being cost/resources, scope or schedule. The overall focus is on functional excellence.
Let’s use the example of supplier part shortages, a common problem for a production process:
Production Floor Team Meeting: supplier part shortages are identified and addressed ‘real-time’ by a shop floor expeditor to the extent possible. Supplier part shortages that need to be escalated are added to a list and provided to the production core team meeting CTL responsible supplier order fulfillment. The CTL may communicate status through an expeditor or may provide status directly by attending production floor meetings.
Production Core Team Meeting: the CTL responsible for supplier order fulfillment summarizes actions planned, or being taken, to ensure supplier parts are provided. He or she may need an order scheduler, other procurement personnel, or supplier quality as team members and enlist the help of the OPS PM and functional managers to obtain this. The “supplier order fulfillment CTL” also summarizes systemic issues or problematic suppliers in preparation for the production steerco meeting. If escalation is required, the CTL and/or the Ops PM negotiates for skillsets with the functional manager.
Production Steering Committee Meeting: the supplier order fulfillment CTL summarizes status, actions taken, projects and where he or she needs help. Since the primary levers are cost/resources, scope or schedule, actions enabled by the production steerco might include enabling supplier visits, paying expedite fees, deferring engineering changes, etc. Also, the production steerco might enable project resources to address systemic issues, such as scheduling inaccuracies. A benefit of the steering committee is the VP or Director visibility across all the functions and/or with respect to specific cross-functional issues affecting production. The Ops PM also has this visibility and can work closely with the VP or director to facilitate awareness of functional excellence.
Note several features listed as follows:
- Production supervisor is responsible and accountable on the shop floor within his span of control
- CTLs are functionally-based to address problems related to their area of expertise
- CTLs may also lead special project teams outside of the production meetings
- CTLs can be reassigned issues if, for example, a production issue is better addressed by engineering or vice-versa
- Each tier has an escalation path
- Escalation is primarily based on adding more resources or skillsets (supporting existing functional expertise and not necessarily “second-guessing” the solution path)
- Escalation is through the core team efforts first, and with the functional managers concurrence to bring it to the steering committee
- Functional managers focus on providing skillsets or experience in their area of discipline
- Ops PMs are responsible and accountable for effectively facilitating meetings, escalating issues, project and program management
- Ops PMs are not responsible or accountable for technical decision-making
- CTLs are responsible, Functional Managers are accountable at the Tier 2 level
- Meeting chairperson (director or VP) is accountable functional managers are responsible, at the Tier 3 level
- Tier 3 should be asking how Tier 2 could be empowered without escalating issues…same is true for Tier 2 / 1.
Your production process might require an additional layer (tier), or might require clarification of roles and responsibilities. At the very least, consider empowerment, escalation paths, accountability, responsibility and meeting effectiveness as some fundamentals of a continuous robust production support process.
Leave a Reply