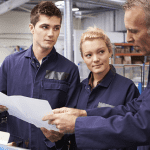
As I work with teams of operators and skilled trades people performing RCM analyses at companies around the world at some point in time as we are discussing the failure modes and effects I might ask the question; how does your company ensure that the skilled trades people working on your assets are actually qualified to work on the equipment?
This question is often met with a look of confusion.
I will then ask, how do we know if a person who calls themselves an electrician is actually qualified to work on a 3 phase, explosion proof electrical circuit? Or, that the next guy who calls himself a mechanic can actually align the motor and gearbox shafts to an alignment specification of +/- .002”?
Having made the question clear, the response I most often hear is “we don’t have a process, we rely on one person teaching the next but if you’re asking about a formal apprentice program, we lost that years ago and it has never come back.”
Interesting, and maybe this is just one of my own personal hang-ups but I have a hard time with someone who calls themselves a Electrician because they helped a friend hook up their cable TV, or the next guy who calls himself a welder because he made two pieces of metal stick together and fixed the loud noise coming from the tail pipe of his K-car.
While apprentice programs seem to be dying all around the United States, the level of talented and certified skilled trades people is shrinking at an alarming rate. More disturbing is the lack of understanding at the executive level regarding the importance of this issue. The reliability of your manufacturing assets is dependent on the ability of your skilled trades people to perform maintenance tasks to a level of precision that exceeds that of a surgeon! (See Examples Below) Yet for some unknown reason we want to believe that all of our tradespeople are created equal because they each have a high school diploma?
Formal Apprentice programs are what build the foundation and understanding regarding the importance of precision maintenance. The reliability and total life cycle of your assets along with the safety of your facility is highly dependent on the ability of your tradespeople and their knowledge of precision maintenance and safe work practices.
The examples below came from internet searches of “Measuring Surgical Precision” and Precision Alignment Standards. Note the that precision of a surgeon performing hip replacement is 4mm and the precision required for rotating shaft alignment is +/- .002” or .0762mm
Regarding the level of precision a Surgeon works to when performing hip replacement surgery;
”Precision surgical guides with 4-mm occlusogingival height may provide adequate accuracy for implant placement. Reducing the occlusogingival height of the guide may ease the use of precision-guided surgery without compromising the accuracy of implant placement.”
Specifying Shaft Alignment Written by Victor Wowk, P.E. Machine Dynamics, Inc. Monday, 01 May 2000 20:02
“After shim changes are made, the above test shall be repeated at all feet until less than 0.002 inch rise is measured at each foot. If shim changes cannot adjust the rise, then the base will need to be ground or machined. See Section D, “Bases and Foundations.”
Having now been exposed to the truth, that your tradespeople need to work to a higher level of precision than a surgeon, can we please bring back the apprentice programs?
The safety and reliability of your equipment and your facility depend on this critical training!
As usual I want to hear your stories and opinions! Have you been through an apprentice program and how did it help your life? Did you company stop its Apprentice training program? What were the effects of doing so? Has your company started Apprentice training again?
Expect to see more on this subject!
Doug Plucknette, Principal & World-Wide RCM Discipline Leader at Allied Reliability Group is a Reliability Engineering Consultant and Published Author of “Reliability Centered Maintenance using RCM Blitz™ and Clean, Green and Reliable. Having created the RCM Blitz™ Methodology he has been an RCM Practitioner and Trainer for over 20 years. Doug resides in Spencerport, NY and can be reached at plucknetted@alliedreliability.com
Yes l also got into the reliability field near the end of my apprenticeship. Lucky for me I had a great mentor Tom Schiff who is now the Global engineering manager for Mobil Exxon Tom allowed go to any school and use my training to further develop my skills