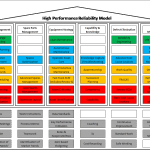
During a recent business trip, I had the opportunity to attend a sister plant in another part of the world. I had been told how good the plant was in Planning & Scheduling. When I attended the weekly planning meeting, I was shocked. It was chaos and confusion, with the planner writing notifications to be put on next week’s schedule, which started the next day. They thought this was good practice.
Often, we don’t know, what we don’t know. This leads the belief that an operation is not world class when it is and vice versa. Below is a brief summary of what a world class Reliability & Maintenance looks like
- Work Management: There is a locked in schedule for the upcoming week, identifying when the production equipment will be made available, and who will be doing the work. There is also a 4 week rolling schedule visible that is align with the production schedule.
- Spare Parts Management: All upcoming planned corrective and preventative work has a bin in the storeroom. These bins are clearly labeled with the appropriate work order, contents and scheduled date. The bins are kept in a designated area for kitting, away from the quarantine and receiving areas.
- Equipment Strategy: The Proactive work on the schedule is a mix of preventative, predictive, and proactive root cause analysis work. But not all equipment has proactive work identified, the business has evaluated and determine that some equipment is only run to fail.
- Capability & Knowledge Management: As work is completed, the craft updates the job plan with as much information as possible. This serves as a means to communicate and capture their experience to share with the apprentice. The operation has a defined apprenticeship program in place, to address the upcoming retirement of some senior mechanics and electricians.
- Defect Elimination: According to Ledet from the Manufacturing Game (Turner), implementing Planning, Scheduling and an Equipment Strategy will only get you an increase of 5% uptime. In order to breakthrough and achieve world class uptime, you must work to eliminate defects. This does not mean putting more PMs in place, but to identify the root cause of the defect and eliminate it. This can be done via redesign, material changes, or upskilling.
These first five signs are often what you see and experience on a daily basis and should give you a feel for where you are at. Next time we will explore the remaining five signs.
Remember, to find success, you must first solve the problem, then achieve the implementation of the solution, and finally sustain winning results. Focusing on these five signs, what is your plant doing to be world class? Where are your gaps? Tell me about them and what you are or will be doing to close them.
I’m James Kovacevic
HP RELIABILITY
Solve, Achieve, Sustain
Leave a Reply