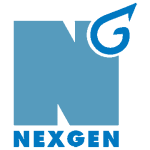
For conscientious plant managers and production leaders, achieving successful and sustainable Total Productive Maintenance (TPM) is a top priority. TPM is the key to reducing downtime, preventing breakdowns, and ensuring top-notch product quality during the process of manufacturing maintenance. But how do you put a TPM plan into action, and what steps should you follow to seamlessly integrate it into your existing operations and maintenance procedures? Keep reading, and we’ll break down what TPM is, how to implement it step by step, and why it matters.
Understanding Total Productive Maintenance
TPM has its roots in the Japanese industry and focuses on maintaining and improving production systems. It encompasses all employees, regardless of their role, in the maintenance and servicing of an organization’s equipment and machinery. TPM aims to minimize equipment failures, boost productivity, and foster a sense of ownership among employees for the technology, safety, and environment they work with daily.
How Does a CMMS Support TPM (Total Productive Maintenance)?
A CMMS (Computerized Maintenance Management System) is a powerful tool that can significantly support your TPM (Total Productive Maintenance) implementation. Here’s how:
Supporting the TPM Pillars:
Autonomous Maintenance:
- CMMS enables operators to access maintenance procedures, checklists, and training materials easily.
- It tracks completed tasks, providing operators with ownership and responsibility.
- Data on minor issues helps identify equipment deterioration and improve autonomous tasks.
Focused Improvement:
- CMMS captures data on breakdowns, allowing root cause analysis and targeted improvement efforts.
- It tracks the effectiveness of improvement initiatives and measures progress towards goals.
Planned Maintenance:
- CMMS schedules preventive maintenance tasks based on equipment history and manufacturer recommendations.
- It automates reminders and work order generation, ensuring timely intervention.
- Inventory management within CMMS ensures parts are available for planned maintenance.
Quality Management:
- CMMS integrates with quality control systems, providing insights into maintenance’s impact on quality.
- It helps track trends and identify maintenance-related quality issues.
Equipment Management:
- CMMS stores equipment history, manuals, and spare parts information in one central location.
- It tracks equipment lifecycle and depreciation, facilitating informed replacement decisions.
Education & Training:
- CMMS can house training materials and track employee maintenance certifications.
- It can be used to assign and monitor training based on individual needs and equipment expertise.
Administrative & Office:
- CMMS automates workflows, reducing paperwork and administrative burden.
- It provides reports and dashboards for performance monitoring and decision-making.
Safety, Health & Environment:
- CMMS can manage safety checklists and track safety incidents.
- It can be used to schedule and track environmental compliance activities.
Additional Benefits:
- Improved communication and collaboration: CMMS provides a shared platform for maintenance teams, production, and management.
- Increased data-driven decision-making: CMMS provides historical data and analytics for informed action.
- Reduced downtime and costs: Proactive maintenance reduces breakdowns and associated costs.
- Improved equipment lifespan and performance: Optimized maintenance extends equipment life and productivity.
How to Implement Total Productive Maintenance?
Implementing TPM requires a structured approach and commitment from all levels. Start by building awareness, assembling a cross-functional team, and identifying a pilot area. Measure OEE and define maintenance standards. Train operators and improve equipment conditions. Next, move to continuous improvement. Empower operators through autonomous maintenance, identify and address major loss categories, and standardize best practices. Document lessons learned and refine procedures. Finally, expand TPM to other areas, integrate with existing systems, and maintain a culture of continuous improvement. Remember, communication, participation, and long-term commitment are key to success.
Final Thoughts
TPM is a powerful strategy for enhancing productivity and equipment reliability while fostering a sense of ownership among employees. By following these steps, you can successfully implement TPM and reap its benefits for your organization.
Leave a Reply