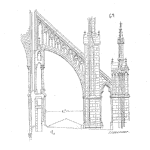
There are two basic approaches when addressing product reliability: Reactive or Proactive. Neither is right or wrong.
The reactive approach has the limitation of responding to failures that occur during prototyping, production and customer use.
The proactive approach focuses on preventing product design, assembly, and use issues before they have the opportunity to create a product failure.
1. Reactive approach
The reactive approach focuses on identifying failures, conducting root cause analysis and implementing the appropriate corrective action.
This may include a redesign of the product or a change in suppliers. Designers often find having a concrete product failure essential to solving reliability issues.
This approach does have the limitation of waiting till something goes wrong before taking action.
Reactive management
The reactive management style is characterized by the only time senior management pays attention to product reliability is when there is a major field failure problem. The basic message from management is to focus on time to market, bill of material cost or product functions and not reliability.
In some cases, the individuals that are particularly adept at solving field failure issues are rewarded and considered heroes. This culture quickly devolves to one where field issues regularly occur pulling engineering talent from new product design tasks.
Creating a culture
A culture of responding to reliability failures may require significant engineering resources to address field issues.
An estimated [Fred’s experience with reliability program assessments] 25% of engineering talent may be committed to addressing design and manufacturing errors related to reliability.
Some organizations create entire departments, i.e. sustaining engineering, to ‘shield’ the product design teams from the re-engineering of products failing in the field.
2. Proactive approach
The proactive approach focuses on preventing failures.
No design is perfect, yet some are better than others especially concerning product returns or lost sales. A product that does what it is expected to do and does it over time is considered reliable. The HP calculator had that reputation and associated very low field failure rate.
The investment into creating a robust and durable design requires informed design practices, the discovery of failure modes and mechanisms, and resources to permit essential design evaluations and improvements.
Set a goal, measure progress
It is the combination of setting a goal and measuring progress toward that goal that enables the design team to knowingly create a reliable product. Measuring reliable both in terms of failure rate and in money enables the entire design team to make informed decisions that consider the impact of cost, time to market and reliability.
The proactive approach uses a range of tools prior to failures occurring to understand and design to avoid a wide range of possible failure mechanisms.
This requires an understanding of materials, design performance, product use and the environment.
The proactive design for reliability approach attempts to fully understand the full range of stresses and incidents that may occur to the product and then to design a product that will continue to function within that environment.
It may not be feasible to create a product that will work across every set of possible stresses the future individual products may experience, yet making informed decision’s that minimize the field failure rate and customer experience is possible.
Related:
Leave a Reply