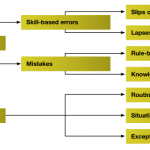
Equipment is described as reliable when it functions as designed without failure. Admittedly, equipment failure of any kind is quite inconvenient especially in fast-paced environments like the manufacturing sector. However, the consequences of failure – if it were to occur – go just beyond the usual inconveniences of unplanned downtime, lost productivity, lost revenue, etc. All these are bad enough, but should equipment failure cause injury or fatality, recovering from the consequences could become an uphill task.
Definitely, there is a valid connection between safety and reliability and optimized reliability and maintenance programs improve safety performance. But, the greater danger here is that a machine can function as designed yet be extremely unsafe to its operators and users under certain conditions. Especially in high-hazard environments like power and nuclear generation, employees can relate all too well with such situations.
So, what would cause a reliable asset to become so unsafe? For one thing, human error. Statistics indicate that in every 10 accidents, up to 9 of them could be due to human error. The same source shows that in both civil and military aviation, almost 70 percent of accidents result from human error.
Coming back to the industrial workplace, our concern here is how to reduce your exposure to this risk. We believe that automating safety management in an organization will go a long way to close gaps in monitoring safety.
Below, we discuss one such automation resource – computerized maintenance management system (CMMS) – and some ways that it helps to create an injury-free environment by guarding against the conditions that release hazards.
1) Adequate and Timely Maintenance
Poorly executed maintenance and maintenance that is deferred for whatever reasons contribute to safety hazards, accidents, and the subsequent reputation damage that affected organizations will face.
Funding issues aside, there are several reasons why maintenance may be delayed or poorly done. Most commonly they include:
- a variety of scheduling mistakes
- there are several clashes in the maintenance schedule
- the required spare parts are out of stock
- instructions were not clear or were misinterpreted by the technician
In each of the situations mentioned above, if the required information for the maintenance activities had been logged in beforehand in a CMMS, it would eliminate many of these issues.
A CMMS serves to centralize data around all of the assets in an organization, it organizes any related work requests and allows users to input step-by-step details and special work instructions, thereby leaving minimal room for confusion.
This advantage is critical for speeding up maintenance and for better maintenance scheduling.
2) Tracking Safety Risks
If your facility is very busy or your operations span across several locations, it is not advisable to track safety risks manually.
Let’s paint a picture of what your workload would look like if you tried manual risk tracking:
- hours, days, maybe even months spent sifting through historical health and safety-related reports
- field service personnel would be out of sight and out of mind since you have little or no way to monitor their behavior at remote locations
- no early warning alerts about high-risk equipment
But using a best-in-class CMMS will give you access to its exceptional safety monitoring abilities. For instance, you can access its reporting modules in seconds and get vital historical information about high-risk machines. With this information, it’s easier to pinpoint areas of improvement and preempt future occurrences.
In addition, when CMMS is integrated with predictive maintenance, it allows you to track unsafe conditions in machines and then generate early warning alerts so you conduct timely corrective maintenance.
These alerts will give you some time to take action before the hazard is released. This benefit is invaluable in dangerous work environments as it often makes the difference between a near miss and a disastrous incident.
3) Standardizing Safety Policies and Procedures
The U.K. Safety Regulatory Board, for instance, recognizes two main kinds of human failure:
- Human error – an unintentional action or decision. This includes skill-based errors (such as memory lapses) and mistakes (rule-based and knowledge-based mistakes).
- Violations – intentional failures. Deliberately doing the wrong thing. These can be routine, situational, or exceptional.
But intentional or not, it doesn’t reduce the potential impact that any of these situations will have on the system and other workers. In this regard, an area that safety managers and other unit heads tend to struggle with is in the training of staff and being able to consistently give workers clear instructions for assigned tasks. The challenge is compounded where there is no standardization of instructions and procedures.
You will find that even after several training sessions, workers will forget the exact details of what they learned or they may have difficulties with executing certain steps. Unfortunately, it often happens that rather than getting clarification, a technician may proceed to do what they “think” is right and cause major problems.
With a CMMS, you can reduce training time as well as improve workers’ access to information. It serves as a digital center where different kinds of documentation can be loaded, accessed, and updated even from remote locations. For example, you can upload generalized operating procedures and policies as well as specific instructions for particular assets along with safety requirements in the form of how-to videos, pictures, charts, etc.
This helps to establish and strengthen your processes as it makes information easier to understand and reduces your exposure to human error.
4) Automating Safety Audits
Now that procedures have been standardized and everybody has access to information, it would be somewhat shortsighted to assume that this is enough for safety performance to improve. Remember that when your business has been running for long without any safety issue, the likelihood for complacency sets in.
The responsibility for sustaining a safe workplace or plant rests with every staff from the management to the plant floor and one of the best ways to confirm that people are working safely is through routine safety audits.
Safety audits help to monitor compliance by serving as a reminder of the regulations. They are also useful for noticing any deviations so as to catch them in time. By combining audits with a CMMS, you get the following:
- Safety Checklists. With a CMMS you can easily create and update checklists for any kind of equipment. The checklists allow you to input as much details as required and by using them , technicians can record any observations, update the records, and communicate any issues for further action.
- Evidence for Safety Compliance Inspections. Because CMMS captures extensive historical data, you can use it to record safety related issues such as interventions and procedures over time and present these records as evidence of compliance to regulatory bodies if need be.
- Scheduled Prompts for Physical inspections. You can schedule physical audits of the facility and what workers are doing and get reminders from the CMMS.
In Conclusion
Injuries to machine operators and technicians are quite common in manufacturing plants so it makes sense to update your maintenance and reliability programs with modern tools that deliver multiple benefits. Such tools, like a CMMS, ensure that while workers are protected, your physical assets are protected as well.
Your business’s operations will be better off if you approach both safety and reliability as priorities. It’s a win-win situation for everyone.
Leave a Reply