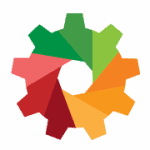
In many manufacturing plants, managing equipment breakdowns and can seem like an overwhelming task. Machine failures occur without warning, production lines go down, managers and supervisors point fingers, and maintenance personnel continually chase parts and problems.
It’s often the case that these plants do not use a CMMS to gather data, plan preventative maintenance, or schedule repairs. This lack of planning contributes to a reactive maintenance environment where personnel is constantly trying to ‘keep up’ with production line problems.
Improving plant capacity utilization is one of the best ways to both lower maintenance costs and reduce production line losses. A few percentage points of improvement in capacity utilization can more than pay for the costs of a CMMS and an improvement program. Implementing a CMMS provides both a systematic approach to maintenance data collection and analysis as well as methods for developing effective reliability programs.
Metrics and Measures
As you probably know, production capacity refers to how much (or how many) units of product a plant or piece of equipment is capable of producing in a given timeframe.
Utilization, on the other hand, refers to the amount of something that is used, such as percent of the time a piece of equipment is producing good parts. One measure that is handy for gauging the effectiveness of a preventative maintenance program is OEE (Overall equipment effectiveness). OEE is a measure that compares actual production to scheduled production and is useful for tracking changes in both capacity utilization and production losses.
Data used in the OEE include (equipment) availability, performance, and quality. When undertaking a capacity utilization improvement program, the OEE value can help identify what is working and what is not. It offers a good starting point measure for analysis and shows the benefits of improved capacity utilization.
OEE is calculated by multiplying ‘availability’ times ‘performance’ times ‘quality’ for a piece of equipment, production line, or a process.
Essentially, this metric reflects the amount of time a process is making good parts as compared to the amount of time available to make good parts. It takes into account all loss factors such as machine stops, bad parts, slow running equipment, etc. and is an excellent method of tracking improvements in capacity utilization.
How CMMS Works to Reduce Costs and Improve Utilization
Once a metric (OEE) is established for tracking progress, a CMMS can be used to develop action items for improving machine uptime and product quality. A preventative maintenance program should be in place using equipment vendor maintenance recommendations as the basis for the PM maintenance schedule.
This schedule can be changed later based on actual performance and analysis. Many times, when work is just beginning on utilization and process improvements, a plant will be operating with a low OEE. Just as a point of reference, OEE benchmark study from SageClarity shows you average values for overall equipment effectiveness:
A low OEE generally indicates that there is too much downtime and too many defective parts. As a result, maintenance personnel are continually reacting to problems making it difficult to adhere to the formal preventative maintenance schedule. As time passes and improvements are implemented, however, this situation will be corrected.
As the improvement program gets underway, you can apply principles of the theory of constraints to help identify a good place to begin. Data from the CMMS such as types of repairs required, length of time needed to complete these repairs, and availability of replacement parts, etc., provide a picture of those areas promising the most benefits. This plus OEE data should be collected and used as work progresses.
Then, you can use lean manufacturing techniques to begin the analysis of the most critical areas first. You can apply root cause analysis, fishbone analysis, single minute exchange of dies, and other tools to develop implementable solutions for correcting process losses. These solutions should be applied to the process as soon as practicable.
As progress is made and improvement is realized, it is likely that other process steps replace the initially identified constraint and become the new constraint. These new areas then become the focus of study, and the improvement program can turn its attention to developing improvements for the next most troubling piece of equipment. Apply the concept of continuous improvement to maintain the project’s momentum.
The CMMS provides raw data for much of the improvement analysis. For example, repair orders should report, among other information:
- Amount of downtime
- Repairs needed
- Parts affected and/or used
- Cause of failure (if known)
- Amount of labor and craft required
- Problems encountered
- Whether the order is a scheduled or an emergency order (planned vs unplanned work)
Much of this and other information can be used to identify the precise source of each problem which will support the development of improvements. Once the analysis is underway, data can be used to ‘drill-down’ to specific causes for inefficiencies.
Using root cause analysis techniques, for instance, can help identify the most fundamental cause for production line problems. Identifying the root cause of a bearing that fails too frequently may involve collecting data on installation practices, lubrication schedules, environment, feeds and speeds, and proper bearing selection. Although several of these factors may contribute to bearing failure, the highest level cause or root cause in this example, may be improper lubrication. Assuming this to be the case, once this issue is resolved, attention should be turned to the next most important factor contributing to the problem. This process of analysis, problem identification, correction, and further analysis continues until the bearing is functioning at or above specifications.
As progress is achieved and the plant begins to run smoother, the OEE value increases, and the maintenance department preventative maintenance program begins to replace the continuous departmental reaction to equipment breakdowns. There are many other positive results as well; reduced costs, improved production schedule attainment, improved quality, and better management of parts inventory.
Final thoughts
A CMMS not only supports a program of continuous improvement designed to minimize production losses and maintenance costs but also provides operating functionality for:
- Preventative maintenance
- Labor tracking
- Scheduling and planning of maintenance tasks
- Improved spare parts management
- Asset tracking
- Budgeting
As with any tool, its effectiveness depends on the skill of the user. Nevertheless, results can be almost universality achieved in improved productivity (both plant-wide and within the maintenance department), reduced equipment downtime and repair costs, improved quality, and improved plant safety.
Leave a Reply