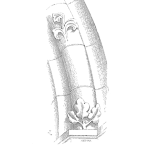
Your engineering team tells you the new deep-water product is ready for field trials because it has passed an API validation test in the lab. But as the OEM engineering manager overseeing product development, how do you know that passing just the validation test is sufficient?
When designing downhole products, there can be a perception that the guidance in a product standard is sufficient for engineering due diligence. One reason is that most product standards are prescriptive. They typically are written by teams of industry SMEs and contain the best practices available at the time of publication. The intent is to enable an OEM to develop a product to meet a minimum acceptable standard.
TRUTH #1: Product standards provide the minimum acceptable due diligence requirements for the product being developed.

However, each OEM designs its product to meet additional requirements unique to its organization. And there are differences among OEMs in how sub-assemblies are validated and third-party components are vetted, to name a few. So, in some cases a product standard provides sufficient due diligence, but in others it should be used as a building block in a system of due diligence. The other building blocks are OEM-controlled and include, but are not limited to:
- Design procedures
- Analysis and simulation procedures.
- Laboratory testing acceptance criteria (components)
- Procedures for selection of materials, coatings, etc.
- Requirements for system integration test (SIT)
- DfR procedures such as FMEA and Root Cause Analysis (RCA)
For the OEM engineering manager, the answer to the question is that passing the product validation test alone may or may not be sufficient. The validation test may need to be preceded by materials tests (e.g. to verify or generate temperature deration factors), simulations, and sub-assembly validations, and then supplemented with SIT and additional DfR activities.
TRUTH #2: Product standards at times are only one part of a due diligence system.
This is the 7th in a series of 10 articles on critical equipment design for offshore completions.
- Critical Equipment Fundamentals
- Technology Readiness Level (TRL)
- Materials and Design Risk
- Temperature Deration
- Design for Reliability (DfR)
- Factors of Safety and Load Factors
- Using Industry Standards in Design
- Modelling and Simulation
- FMEA Improves the Bottom Line
- Lab Testing Programs
Leave a Reply