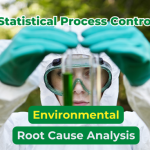
We often jump to the wrong conclusions when non-compliance occurs. Non-compliance occurs when the standards and regulations designed to protect public health and the environment are unmet. Obviously, we must reduce immediate risks. However, these measures often address the symptoms and not the root causes. This leads to further delays or doubling down on the wrong things as we move through mitigation that misses the mark. Using statistical process control in environmental root cause analysis is one way to make sure you’re getting it right!
A Classic Example
A large manufacturing plant had problems with elevated wastewater parameters that exceeded regulatory levels. After much investigation and a formal root cause analysis, several mitigation strategies were implemented to address the primary causes of failure.
The issue came not from our analysis but from the corporate level, which insisted that the mitigation be formalized in a written document with state regulators. The system changes to re-establish compliance were not tested adequately themselves, resulting in more failing tests and intense finger-pointing. In the end, changes in monitoring, additives, and supervisory control just needed time to get fine-tuned.
Making sure statistical process control is established before finalizing mitigation avoids a second crisis during implementation.
Overview of SPC
Statistical Process Control (SPC) is a powerful tool for monitoring and controlling system processes. Its main goal is to verify that processes produce conforming products with minimal variation. While SPC is commonly associated with manufacturing, its principles and techniques can equally apply to environmental root cause analysis.
What is SPC?
SPC involves using statistical methods to monitor and control a process. By collecting and analyzing data from the process, organizations can identify variations that may indicate problems. SPC helps distinguish between common cause variation (inherent to the process) and special cause variation (arising from specific, identifiable sources). This differentiation is crucial for effective problem-solving and process improvement.
The Seven Rules of SPC
SPC is governed by several rules that guide its implementation. These rules help identify non-random patterns that may indicate underlying issues in the process.
Rule 1: Points Beyond Control Limits
Any data point outside the control limits indicates a significant shift in the process.
Rule 2: A Run of Seven Points on One Side of the Mean
Seven consecutive points on one side of the mean suggest a non-random pattern.
Rule 3: A Trend of Seven Points Continuously Increasing or Decreasing
Seven points continuously increasing or decreasing indicates a systematic change in the process.
Rule 4: Two Out of Three Points in the Outer Third
Two out of three consecutive points in the outer third of the control chart signal a potential process shift.
Rule 5: Four Out of Five Points in the Outer Two-Thirds
Four out of five consecutive points in the outer two-thirds of the chart also indicate a process shift.
Rule 6: Fifteen Points in the Inner Third
Fifteen consecutive points in the inner third suggest reduced variability.
Rule 7: Eight Points with No Points in the Inner Third
Indicates a pattern that deviates from randomness.
Applying SPC in Environmental Root Cause Analysis
Identifying Environmental Issues
Environmental root cause analysis involves identifying the underlying causes of environmental problems. Organizations collect data on various environmental parameters such as air quality, water quality, emissions, and waste generation. Control charts, a fundamental tool in SPC, can be used to monitor these parameters over time. Any deviations from the norm, as highlighted by the seven rules, can indicate potential environmental issues.
Analyzing Data for Root Causes
Once potential issues are identified, the next step is to analyze the data to determine the root causes. This involves looking for patterns and correlations in the data. For instance, a sudden increase in emissions might correlate with a change in raw materials or a new production process. These correlations help organizations pinpoint the specific causes of environmental problems.
Developing Mitigation Strategies
Mitigation strategies should aim to eliminate or reduce the root causes. For example, suppose a specific process is found to be a cause of increased emissions. In that case, the organization might consider optimizing the process, changing the raw materials, or installing pollution control equipment. In other cases, monitoring or feedback loops must be shorter to achieve higher control.
Tracking Mitigation Performance
SPC is also used to track the performance of mitigation strategies. In fact, this may be its most valuable application in environmental issues. By continuously monitoring the relevant environmental parameters using control charts, organizations can assess the effectiveness of their mitigation efforts. Any improvements or regressions can be quickly identified, allowing for timely strategy adjustments.
Continuous Improvement
Environmental root cause analysis is an ongoing process. As new data is collected, it should be continually analyzed using SPC methods to ensure the processes remain controlled and compliant with environmental regulations. This continuous improvement cycle maintains sustainable practices and minimizes environmental impact.
Using SPC in Environmental Root Cause Analysis
Statistical Process Control (SPC) is a valuable tool in environmental root cause analysis. By using SPC techniques, organizations can effectively identify, analyze, and address environmental issues. The seven rules of SPC provide a structured approach to monitoring and controlling processes, ensuring that any deviations are correctly identified and rectified. Continuous monitoring and improvement are essential for maintaining environmental sustainability and regulatory compliance.
This article first appeared on www.jdsolomonsolutions.com
JD Solomon Inc provides solutions for facilitation, asset management, and program development at the nexus of facilities, infrastructure, and the environment.
Founded by JD Solomon, Communicating with FINESSE is a not-for-profit community of technical professionals dedicated to being highly communicators as trusted advisors to senior management. Learn more about our publications, webinars, and workshops. Join the community for free.
Leave a Reply