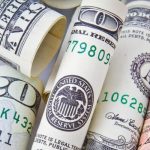
Companies are constantly looking for ways to identify and implement cost-saving measures. Computerized maintenance management software is used to record, manage, and communicate day-to-day operations in your maintenance department. It’s possible to use CMMS to save money in a number of ways. The following are areas in which large cost savings can result through the implementation of equipment maintenance software
- Labor costs
- Rework
- Spare parts
- Customer turnover
- Equipment replacement
- Equipment downtime
With a CMMS, you can immediately lower operational costs by minimizing downtime, reducing inventory, and eliminating overtime and contractor costs. Better work planning and scheduling also increase employee productivity. To put it simply, properly implemented equipment maintenance software can save your company time and money.
Moving from Reactive to Proactive Mode
Too often, a certain piece of equipment or component will break down over and over again and maintenance technicians will go off to repair it without really looking into the problem or determining what caused it. The problem may have occurred so many times that technicians know exactly what to do and how to fix it. Even if the required parts are on hand and the repairs are completed quickly, these recurring repairs require manpower, material resources, and production time.
The goal of any organization using CMMS software should be to move from a reactive approach to a proactive approach to maintenance. When a breakdown occurs, it is important to analyze the situation, verify the probable cause of the breakdown, and document your findings and solutions. Your CMMS can help you find the root cause of the problem by providing you with vital information, such as records of repairs, modifications, parts used, preventive maintenance tasks, and failures. That’s why it’s so important to record not only the preventive maintenance tasks you perform, but also any repairs or modifications to equipment that are carried out.
Uncovering Cost-Saving Opportunities and Solutions
In order to use CMMS to save money, follow the dollars and identify where they went, looking at parts costs, inventory holding costs, labor/overtime costs, shipping costs, downtime costs, costs of quality issues, etc. By evaluating where money is being spent, you can determine the relative size of your cost-saving opportunities and develop a plan of attack.
In order to come up with solutions for achieving cost savings, brainstorm ideas with those on your team who are the most familiar with the problem. You should also include people who don’t know anything about the problem, so they can provide you with out-of-the-box thinking and ideas.
Steering Maintenance Performance with Your CMMS
As your business evolves, your CMMS system should be adjusted to deliver a competitive edge. This can only be accomplished through impeccable record keeping and ongoing data analysis. In order to set up a successful continuous improvement program, you should also have well-defined objectives and performance targets. The key drivers of process improvement are time, quality, and cost.
Involve your maintenance technicians in the improvement process so they can supply you with the data needed to continuously improve your maintenance management process. Tailor the reporting function of your equipment maintenance software to ensure that the reports are providing you with the information required to monitor short-term and long-term trends in your maintenance department.
The goal of CMMS software implementation is to increase the reliability of assets, improve processes, and ultimately, maximize return-on-investment. Schedule a free demo if you’d like to learn more about how to use CMMS to save money and take your equipment maintenance software to the next level.
Leave a Reply