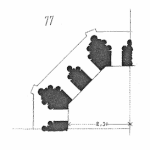
As we all have learned, eliminating defects is the key to a safe and profitable plant. But how do we know where our ‘bugs” are hiding? There are certainly many ways to uncover where the bugs are, but one place in particular is your computerized maintenance management system (CMMS) or enterprise asset management system (EAM), as it is commonly referred.
First of all, what is the purpose of a CMMS/EAM? Most companies implement these systems to help manage the process of doing maintenance in their plants. It is typically the central registry of all their plant asset and location information. It offers tools to help plan and schedule maintenance work and allows for the purchasing of replacement parts. In addition to all these functions, it is a terrific tool to document all of the events related to our plant assets. For example, when we go to a centrifugal pump to replace the mechanical seal we should come back to the CMMS/EAM to record that event. This extra step in the maintenance management process will allow us to “mine” the data to see where repeat problems (aka “bugs”) are hiding.
Unfortunately, most plants do a poor job of documenting history in their CMMS/EAM. There are many reasons for this but below are some of the more common issues related to poor data collection.
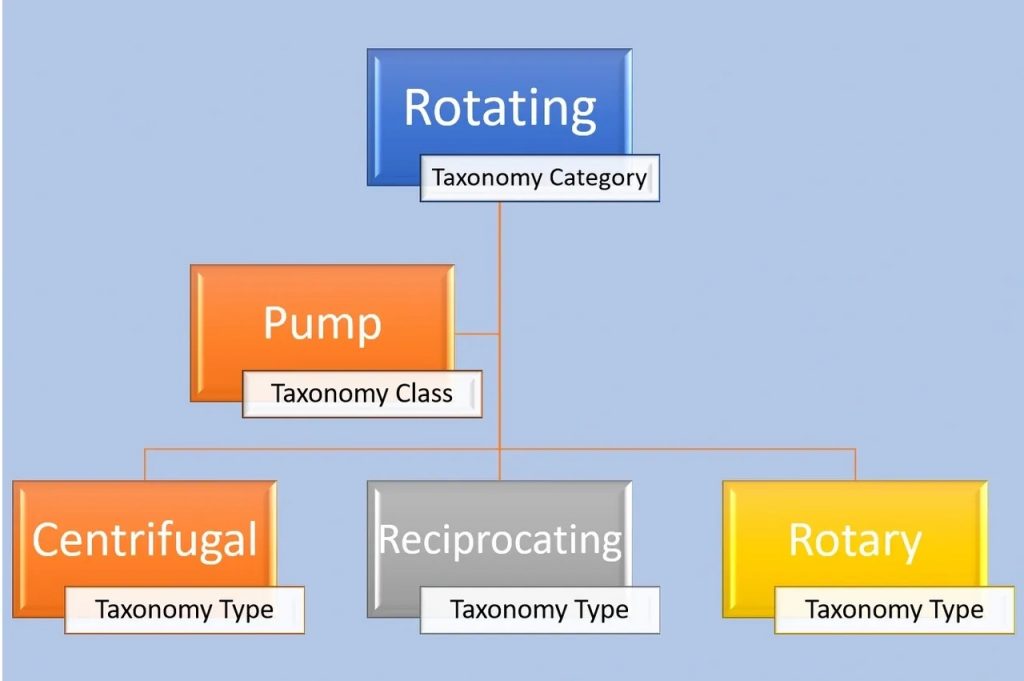
- They lack a comprehensive hierarchy of their assets and locations. This is sometimes referred to as equipment taxonomy. A taxonomy is a collection of all the different equipment categories (e.g., fixed, rotating), equipment classes (e.g., pumps, heat exchangers) and equipment types (e.g. shell and tube heat exchangers, air cooled heat exchangers). In addition to the hierarchy there are technical characteristics for each class of equipment as well as equipment specific codes associated with problems, detection methods, components, damage, causes and activities. Without a comprehensive taxonomy, it is very difficult to document maintenance history.
- Insufficient definitions and training with regards to the collection of data. Users of the system end up using certain fields improperly or not at all. For example, SAP-PM offers a field to determine if a maintenance event was a “breakdown”. The problem, however, is that people have different ideas and definitions as to what signifies a breakdown. Therefore, the field is used inconsistently, and it is difficult to use it for reliability analysis. Simple definitions and explanations of these fields will be a big help in the consistency of the data collected.
- Work orders are written against the wrong equipment. Many times, the originator of a work request is not sure which piece of equipment is the problem (e.g., sometimes a motor problem might be wrongly diagnosed as a pump problem). If the work is written against the wrong piece of equipment, then there is little chance of getting the proper history recorded. Not to mention how it causes headaches for the planner who has to actually plan the work!
- There is no work process related to the closure of work orders. In many places, there is no process to verify work order history. For example, there is no review of the work order to make sure that all the work was properly documented, and necessary codes were filled in. Complicating the issue is when work orders are automatically closed not allowing for a technical review and editing of the work event.
Although these issues and many like them are very common, they are not insurmountable to resolve. In fact, with a few changes to the system configuration and a practical data collection work process it is quite reasonable to expect good quality data coming from our CMMS/EAM.
I would recommend doing a review of your existing CMMS/EAM data to determine where the data gaps are. Are codes being filled in consistently, are important dates updated and accurate, is the proper piece of equipment specified, etc. Once the gaps are identified, it is important to determine the root causes for the gaps. For instance, is it do to insufficient codes (e.g., taxonomy issues) in the system configuration or is there a lack of work processes around the collection of this data? Once the issues are identified a path forward can be formulated to resolve the issues. Many companies employ metrics to measure the quality of the data being collected. For example, they will track how many work orders had the codes filled out in each time period.
So, what can be done with this data? Well, for many it becomes a system for evaluating areas for improvement (aka “Defect Elimination”). It can provide the essential data for developing “Bad Actor” reports, metrics, key performance indicators (KPI). Many companies track reliability metrics like Mean Time Between Failure (MTBF), Mean Time to Restore (MTTR), Reliability, Availability and many others. Most of these measures can be calculated with the data collected in our CMMS/EAM.
So, to help identify the “bugs” within your facility, consider using your existing maintenance system. This data coupled with the knowledge and experience of your action teams can become a winning formula in your defect elimination efforts.
I would like to thank Michelle Ledet Hensley and the entire Ledet family for their many contributions to the field of reliability through their amazing workshop, “The Manufacturing Game”! The workshop experience is incredible and more importantly is a driver for getting action teams to actually resolve the many defects (aka “Bugs”) in our facilities. If you are not familiar with the Manufacturing Game, check them out at http://manufacturinggame.com.
Leave a Reply