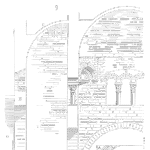
This article discusses the use of vee-belt drives. It covers some basic theory of friction drives and lists 11 factors to be considered when using vee-belt drives.
Friction Drives
A friction drive connects two shafts by a belt that is drawn taut enough to grip each shaft and turn them. Each shaft has a pulley attached to it. The belt is pulled tight to create friction with the pulleys. As the drive pulley turns, the belt moves the connected driven pulley. Figure 1 show elevation and plan views of a twin belt drive arrangement.
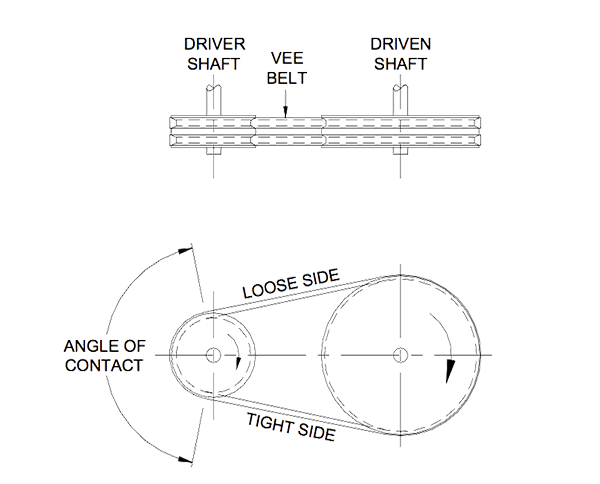
The success of the drive depends on maintaining frictional contact between belt and pulleys. Vee-belt drive friction is dependent on several factors. These are –
- Tight side and loose side belt tensions.
- The coefficient of friction between the belt material and the pulley material.
- The total angle of contact around the pulley, which depends on the pulley diameters and their distance apart.
- The centrifugal force lifting the belt off the pulley
produced by the rotation of the pulley. - The angle of the vee in the pulley which acts to wedge
the belt in place. It is usually between 17o and 19o.
THE ADVANTAGES OF VEE-BELTS
Vee-belts offer a number of advantages in their use.
- Easy, flexible equipment design, as tolerances are not
critical. - Reduce shock and vibration transmission.
- Changing pulley sizes changes the driven shaft speed.
- They require no lubrication.
- Maintenance is easy provided unrestricted access is
available to the drive arrangement. - The pulley alignment is quickly done with a straight
edge or a string line spanning across both pulley faces. - Setting the belt tension is readily achieved by jacking the pulleys apart and measuring the transverse distance
the belt can move. - Higher shaft torsional loads are handled by using
multiple belt pulleys. - In an overload situation the belts slip and the equipment
is protected. - A jockey pulley can be installed to increase the angle of
contact and allow transfer of more power. It can be mounted on either the tight or loose belt side and adjusted inwards to provide more angle of contact.
The Belt
Conventional vee-belts are made of rubber reinforced with imbedded plastic, fibreglass or steel cords. The cross- sectional area of the belt depends on the power to be transmitted through the belt. Multiple belts are used in combination to transmit large amounts of power.
The Pulley
Pulleys can be cast iron or steel. The vee groves are machined into the solid billet. The pulley is usually keyed to the shaft. They must be balanced.
Issues to Consider When Using Vee-Belt Drives
When using vee-belt drives there a number issues to address.
- Belts in multiple belt drives may need to be a matched set. A matched set of belts means each belt is of equal length so they all take equal loads. In an unmatched set the shorter belt is more heavily loaded and fails soonest.
- Rubber has a limited life. Oxygen in the air, heat, dirt and oil deteriorate it while tight bends and the loads carried through the fibres of the belt stress the rubber.
- Dirty, dusty conditions destroy both belt and pulley. Dust settles on the pulley and imbeds into the rubber. Eventually the belt starts to slip thereby polishing the pulley and reducing the friction between belt and pulley. It may be necessary to install a ventilated, dust proof enclosure around the equipment. This is often the case for belt driven air compressors in dusty locations.
- Belt life is limited and they will fail by stretching, snapping or slipping when their working life limit is reached. Drive belts and pulleys should be inspected on a preventative maintenance routine or replaced prior the likely end of their working life. Replace a stretched, cracked or shiny belt immediately.
- Provide pulleys of generous diameter so the belts are not excessively flexed. Flexing around a small pulley produces high stress gradients across the belt.
- • Determine the optimum number of belts for a drive so they are loaded to the manufacturer’s recommendations.
- The separation distance of the pulleys determines the angle of contact the belt makes with each pulley. If the separation distance is too close the driven pulley will not have enough belt in contact with it to develop the required driving friction.
- When the pulley vee faces become polished the pulley must be replaced. It is possible reclaim the pulley by lightly machining the groove.
- As more belts are added to the drive and tensioned to the required load the driven and driver shaft bending loads increase. This will raise the radial loads on the shaft bearings nearest the pulley and act to reduce their working life. Insure the shaft bearing type selected can accommodate high radial loads.
- For safety reasons the belts and pulleys require a guard over them. The guard must be well ventilated and not allow heat from the motor or working equipment to be trapped and overheat the belts. Provide plentiful access and make removal of the guard easy.
- Belt tensioning testers are available to check the amount of tension applied to the belt meets manufacturer’s recommendations.
Mike Sondalini – Maintenance Engineer
If you found this interesting, you may like the ebook Process Control Essentials.
thank you for the information