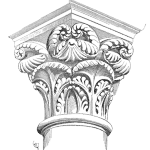
Do you want a PM program that really works
Reliability Centered Maintenance – Re-engineered (RCM-R®)…
… is the world’s leading method for identifying maintenance and other activities required to sustain reliable performance of physical assets. Previously I discussed the various maintenance approaches you can use. This method (RCM-R®) is a structured approach to making those choices. If you want a proactive maintenance program that really works, then Reliability Centered Maintenance is the most thorough approach you can take to get there.Since the 1970’s RCM (generic) has been responsible for huge improvements in airline flight safety – crash rates today are 1 / 120th of what they were before RCM, and the costs of aircraft maintenance programs are way down. We are all comfortable flying in safety. That would not be the case had RCM not come along.
Elsewhere, like nuclear power and military systems, where high reliability is needed it has produced similarly impressive improvements. With more dependable uptime (availability) we get more production and revenues, lower costs, improved safety and environmental compliance. There’s nothing bad about any of those!
RCM was initially developed by Stan Nowlan and Howard Heap building on a decision logic already being used in the aircraft industry. They published their studies of aircraft failures in a paper entitled, “Reliability Centered Maintenance” in 1978. Since then a number of RCM variations have arisen, John Moubray’s RCM2 is one of the best known and his book (from 1991) marked the start of RCM in other industrial applications. John “industrialized” Nowlan and Heap’s work and the focus initially was on keep costs down by specifying only the maintenance activities that were needed, eliminating a lot of “over-maintenance”. In time, other methods sprung up with various claims (cheaper, faster, more effective, etc.). Knowing their own standards for RCM were “gold plated”, the US DoD wanted a non-military standard, approached the Society of Automotive Engineers, and standard SAE JA-1011 was created. If you had a method you wanted to call RCM, you now have a standard to meet. It cleared up market confusion and raised the bar on what was becoming a race to the bottom (price wise). Today, a few methods remain compliant to JA-1011. In 2017, our version of RCM, “Reliability Centered Maintenace – Re-Engineered”, RCM-R®. by Jesus Sifonte and I enhances the basic JA-1011 compliant method, include more technical rigor, process rigor, aligns with various International Standards, and adopts a training approach that is less costly and quicker to implement than the other methods. Since introducing it in 2017, we have seen all of those objectives achieved!
Like other JA-1011 compliant methods, it is team-based. It utilizes a combination of knowledge and expertise from maintainers, engineers and operators. The team (usually 3 to 5 people) analyses one system at a time. The system can be a piece of process or mobile equipment, a manufacturing or factory process, building systems, linear assets (pipeline, electrical utility) or even small processing plants (like you find in upstream oil and gas operations). Complexity drives the duration of the analysis, not system size. I’ve analyzed physically large systems in just a few days, while complex assets like an engine can take longer. The analysis is carried out in a series of meetings scheduled to fit into your day-too-day operations. A trained facilitator asks the RCM-R® questions, gets answers from his team of “experts” (you the users), and records the analysis. During that process they make decisions on future actions that are both technically sound and “worth it” from the perspectives of cost and risk.
The seven questions as required by the SAE standard are:
- What are the functions of the asset and their desired levels of performance?
- What are the failed states associated with each function (i.e.: functional failures)?
- What are the failure modes that lead to those failed states?
- What are the effects of those failure modes? (i.e.: what happens if we do nothing to prevent them from occurring?)
- How do those failure modes matter? (i.e.: safety, hidden, operational, non-operational?)
- Can we do anything proactive to predict or prevent the failure?
- If not, then what can we do? (i.e.: run-to-failure, failure finding, re-design or some other one-time change?)
On the surface, those questions appear easy enough to answer but there is a great deal of knowledge behind each of them. For instance, the very first question asks about functions. The functions are the things the system does for us. They are NOT merely a description of what the system “is”. A valve, for example, allows, impedes (restricts) or closes off a flow, while containing the fluid in the system. There is usually a primary function (i.e.: the main reason we have the system) as well as a number (sometimes many) secondary functions (e.g.: environmental, safety, control, containment, appearance, protective, economy, efficiency and sometimes even functions we really don’t want, but they are part of the design). All functions are listed along with the standards of performance required of them. The standards define what the operators “want” (or need) from the system, not what it is capable of doing. Engineering specs are helpful to provide us with a sanity check to ensure we are not asking more of the system than it was designed for.
Many technical people are so used to dealing with “what” a system is that they forget what it does. For instance a single function like, “to contain the pumped liquid” implies an absolute standard (i.e.: it cannot leak at all) and it applies to all components that have a containment function (e.g.: housings, pipes, gaskets, valves, seals, etc.). It is not necessary to list all the components at all. Operations people grasp this right away because it fits so well with their perceptions, but technical people often struggle with this different perspective. Engineers who have performed FMEA (Failure Modes and Effects Analysis) are often used to listing failure modes for each component, not each function. They end up with much longer lists of failure modes with a great deal of repetition within those lists. By addressing functions we deal with what is important, and do it only once! It’s very efficient once the team gets the hang of it.
RCM questions cannot be answered without truly understanding what is behind the question. I’ve seen many attempts to read a book (often Moubray’s because it is a very good one) and then attempt to perform RCM without any other training or facilitation. Those almost always turn out poorly.
The first four questions are the equivalent of performing a Failure Modes and Effects Analysis (FMEA), but focused on functions, not components. The last three questions of the standard, take the user through a decision logic (a diagram is used for this) to help arrive at technically feasible decisions that are also worth-while from the perspective of costs and risks being controlled.
The diagram is structured so that the most likely answers are reached early – again to make the method efficient. Once a technical decision is reached, the team then carries out a brief analysis of risk or costs, depending on the nature of the consequences from each failure mode. If risk is reduced or costs are lowered, then the decision is “worth it” to implement. If not, then the team continues to look at technical options until they are exhausted and it must accept run-to-failure or some sort of redesign (or other one-time change) as a default solution.
Implementing RCM_R®
Once the analysis is completed its decisions must be put into practice, or the effort is wasted. Decisions result in actions (tasks) at frequencies (also determined in the analysis), along with assignment of who (which trade) does the work. That must all make its way into your maintenance management work order system for automated triggering and issue of work orders. Sometimes tasks by the same trade that occur at the same frequencies are combined into a single work order in that process of converting from analysis to PM program. If there are decisions about technical redesigns, then those recommendations must be sent to engineering for work. If the decisions require training (e.g.: new skills or knowledge to obviate human errors), rewrites of procedures or some other one-time changes, then those too must be carried out by the appropriate responsible authority (e.g.: technical standards group, engineering group, training group, etc.).
This step of implementing, which is actually not part of what the standard describes, is where most other RCM initiatives fail. Often, the analysis is completed, the team is disbanded back to their normal jobs, no one takes ownership of this final phase of the project and the effort produces no results other than documented effort and reports. In RCM-R® we emphasize the importance of this phase and make sure that our customers include it in their plans.
Doing an RCM-R® analysis requires collaboration among maintenance, operations and engineering departments. Getting the outcomes implemented requires those, as well as training, human resources, finance and possibly other departments. It is a “whole organization” process, not, as the name suggests, a “maintenance only” initiative.
Getting Started
Organizations usually go through some sort of decision process before committing to an RCM® program. Often some training is delivered to familiarize employees with the method. Then they decide if they feel it can work. The answer is usually “yes”, so then they set up a pilot project, to be facilitated by the trainer. The pilot is carried out (usually on a known to troublesome system or equipment) and the results put into place. If it is a success or shows promise, then the decision is made to continue with the initiative. That leads to more training, more projects, training of in-house facilitators, and increasingly greater success.
Anyone participating in the analyses needs to have the basic analyst training (2 day RCM-R® course). A few pilot projects provide experience and confidence in the method. Initially an experienced facilitator leads those analyses. The concept is proven, results are obtained, and the standard is set for future (in-house) facilitators. Results can be very quick. In fact it is not uncommon to identify changes in operating practices, or excessive maintenance, that are implemented even before the analysis is completed.
Facilitator training is not onerous. RCM-R® uses a 3-day facilitation skills course. That qualifies your facilitators, and then they are ready to gain experience. Mentoring of the facilitators through their first 2 or 3 analyses achieves that. In the first analysis we actively co-facilitate, then we step back and let the new facilitator run the show. After that one final analysis (solo) is carried out without external help. That analysis is reviewed and any flaws pointed out. It’s a bit like learning to fly a plane: ground school, initial flight training while instructor holds onto a dual control, more flying where the instructor has hands off the controls, and finally a solo.
RCM-R® includes some mathematics to ensure it is technically rigorous. The JA-1011 standard does not require this, so most RCM methods do not go this far. Most of the math is fairly easy, and engineers have no trouble with it. However, we do find some analysts (often operators and trades) are not comfortable with the math. Facilitators need to know where to use the basic formulas and to ensure the calculations are done. They can rely on a team member with the technical training and skills or they can do it themselves. The two day RCM-R® course covers the most basic (and most common situations). We offer advanced reliability training to cover the more complex situations. The more mathematically inclined facilitators and engineers are usually the ones to get this advanced training.
RCM-R® consultants are highly trained and experienced. They teach the courses and mentor newly trained facilitators. Companies and government departments that have used our services have all demonstrated excellent results from their RCM-R® work.
A final word – don’t cheap out. Once you have had the training, carried out pilot projects and begun to analyze your own systems you are ready to go solo without the outside help. Without those steps beyond just “reading” the book, you are highly likely to fail. Make sure anyone participating in your analyses has had the training. Without they will slow the effort down considerably. If they have strong personalities and opinions, and do not understand the technical underpinnings of RCM, they may sway the analysis off course. Don’t expect a facilitator who is not highly familiar with RCM-R® to be able to lead your analysis meetings. This is not a typical facilitation effort where subject matter knowledge can come entirely from the team being facilitated. While the basic facilitation skills are the same, they can be easily side-tracked if they are not familiar with RCM-R®’s nuances.
Leave a Reply