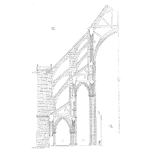
Delivering the best reliability performance within the various constraints imposed.
Without constraints such as budget, time to market, customer expectation, product functional capabilities, and product weight, you certainly could design and deliver a highly reliable product.
There always are constraints.
In the Oliver Wendall Holmes poem, The One Hoss Shay, the deacon procures the strongest oak, the supplest leather, and the best of best materials. Cost was not a constraint. And the shay lasted 100 years to the day.
If the technology permits there may be stronger or more durable components available for a price, yet cost is often a limiting factor.
Balancing cost and reliability is a common discussion.
Knowing the relationship between marginal cost and reliability improvement is essential to make informed decisions. Improving reliability provides a financial benefit, to some extent. It has a diminishing return once the reliability performance is beyond the expected reliability of the customer. And, cost is felt immediately.
Given more time the development team may find a resolve additional faults within the system. Given more time the design and assembly teams can improve reliability. Well, time is money. A product not selling provides no value to customers nor your business.
Solely focused on time to market or the ship date is a problem though. Balancing the risk of field failures at an unacceptable level versus the value of a month’s extra sales is another tradeoff discussion. What is the daily sales rate and what is the cost per percent of failure rate? Then given another month how much lower can the team drive the field failure rate?
Reliability Optimization is finding the right balance for your situation, technology, and customers.
Failure Avoidance and Tolerance
There are two fundamental approaches to improving a system’s reliability performance.
You can create a reliable product that fails less often (failure avoidance). Or, your team may explore adding resilience such that given a failure the system continues to function (fault tolerance).
In both approaches, an understanding of the goals, customer expectations, risks, and constraints permits the appropriate selection of one or the other, or both, approaches to achieve an optimized design.
Tools such as FMEA, HALT, derating, stress – strength analysis, redundancy and reliability modeling all provide tools to identify options and improve reliability within the given constraints.
Related:
Solving a Reliability Optimization Example (article)
Reliability Block Diagrams Overview and Value (article)
Role of Reliability in an Organization (article)
Reliability Allocation and Optimization : During the process of developing a new product, the engineer is often faced with the task of designing a system that conforms to a set of reliability specifications. The engineer is given the goal for the system and must then develop a design that will achieve the desired reliability of the system while performing all of the system’s intended functions at a minimum cost. This involves a “balancing act” of determining how to allocate reliability to the components in the system so the system will meet its reliability goal while at the same time insuring that the system meets all of the other associated performance specifications.
Good subject matter on this topic is available in this Webpage. http://weibull.com/hotwire/issue6/hottopics6.htm
Thanks for the note Hilaire, and the link is useful, too. Cheers, Fred