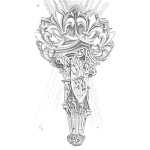
Once upon a time in my former life, I served as the Quality Manager for a $300M tier-one automotive manufacturing plant that provided components and assemblies to OEM vehicle assembly plants. You would recognize our customers – most of the big names. This assignment was a departure from my previous roles in product development and testing. To say that the job was eye-opening is an understatement. Years later, I described this three-year experience to friends as my “tour of duty on the front lines.” Anyone who has spent any time in manufacturing can certainly relate!
Anyhow, when asked by outsiders what the job of a Quality Engineer was, I would say that it is to protect customers from quality problems coming out of the plant. This includes internal manufacturing quality as well as supplier quality and material defects. Nothing should leave the plant that doesn’t meet spec.
Fast forward a few years and I found myself back in product development but this time as a Validation Manager. The validation engineers (VE’s) on my team were responsible for coming up with the verification test plans (think informal sandbox testing) and design (DV) and product (PV) validation test plans for their assigned product lines. They would follow the execution of testing until formal validation requirements were met.
So what is the job of a Validation Engineer? To put it in terms similar to what I used above, I would say that it is to protect customers from product design problems coming out of engineering. For sure, there are more thorough definitions of these roles, but I always thought it made sense to describe them this way.
But how else might you describe the job of a validation engineer? How about giving our parts a chance to fail on test before they get into customer’s hands? Also, over simplistic for sure since it doesn’t address all the activities involving risk identification and risk reduction that don’t occur in the test lab. Still, I like that one a lot. A more complete statement of this thought is that a VE would like to give design- and manufacturing-representative parts a chance to fail on field-relevant laboratory tests before production parts are released. Or, more simply, in validation we want to test meaningful parts on meaningful tests.
And while we’re at it, let’s do this with sample sizes and test strategies that allow us to statistically demonstrate that we meet reliability (with confidence) at one life!
Leave a Reply