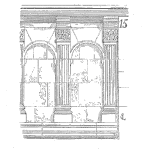
In line with the RAM acronym sequence, we often start and go no further than the “R” in Reliability. In doing so, we forget about the “M”. The question often asked is: “what is the reliability of the system?” But rarely asked is: “what is the maintainability of the same system?” Myself, am guilty of this omission. Hence this article to remind myself and you the reader, of the importance of Maintainability in industry.
Reliability, Availability, and Maintainability (RAM) modeling overview
The fundamental purpose of Reliability, Availability, and Maintainability (RAM) modeling is quantifying system performance, typically in a future interval of time. A system is a collection of items whose coordinated operation leads to a numerical output, generally a production value. The collection of items includes subsystems, components, software, human operations, etc. An automobile, for example, can be a system. Its sub-components are the drivetrain, engine, gearbox, etc. In RAM models, it is crucial to account for relationships between items to determine the final output of the system. RAM models have proven to be effective cost-avoidance or decision-making tools in various industries.
Definition of Reliability
Reliability is a probability. It is the probability that a system will perform its intended function. This is in a specified mission time and within specific process conditions. Reliability (R) is related to the Probability of Success as opposed to the Probability of Failure (F). The relation between R and F is:
R = 1 – F (for mission time t)
In the above context, a reliability example would be: What is the probability that a centrifugal pump in a sheltered enclosure will pump 3,000m3/day of sweet crude oil without unplanned failures for a period of 8,760 running hours?
Definition of Availability
In the simplest terms, Availability (A) is the amount of time that a system will be running versus the total available time or time interval considered. It is a measure of a system’s uptime.
Academically, it is a little bit more complex. It is equally a probability. The probability that the system is operating properly or not failed when needed.
Availability is a versatile metric and can have multiple sub-definitions. The diagram below highlights the difference between Reliability and Availability. It is overly simplified and shows that we can have high availability coupled with low reliability. Note that Reliability is zero because the system failed at least once during its required mission time.

So, what about Maintainability?
Maintainability is also a probability. It is the probability of performing a successful repair action within a given time. In other words, it measures how fast a maintenance crew can restore a system after a failure occurs.
Maintainability is based on time to repair which tends to vary. No task is simple and clockwork-like in the maintenance world. Maybe that what keeps us all in a job. Hence, the repair time is usually a random variable and a statistical distribution used to model Maintainability.
In reference to statistical models, the recommended distribution for repair time is lognormal. But like every model construction, one must ensure that the distribution type is correct. When dealing with poor CMMS records in the past, I have defaulted to triangular distributions using three values: minimum, maximum and mean repair time.
What typically affects Maintainability is resources, logistics but more importantly the design of the equipment. Regarding resources or logistics, they influence repair time in the following manner.
- The time taken to diagnose the cause of the failure and set up a repair plan.
- Maintenance technician experience and proficiency will obviously influence the repair time. For example, new equipment where no previous maintenance experience is available will no doubt increase repair time.
- The spare parts logistics or time to get required spare parts on site.
- The time it takes to get maintenance resources to the equipment. Or to get a vendor onsite in the event of a highly specialized repair.
- The time it takes to gain access to the failed parts and replace them. Often known as the wrench time.
- The re-commissioning and start up time of the repaired equipment.
There could be more to this list as every equipment or repair situation is unique.
Maintainability in the original design.
As much as we should design for high reliability or availability, we often tend to overlook designing for Maintainability. This comes at a cost initially as designs and blueprints may need modifications. But the payback is significant later. To quote Fred Schenkelberg, “in order to increase Availability and minimize the cost of maintenance, we have to deliberately design the system to accommodate the needs of maintenance”. In his Accendo article he provides a comprehensive list of steps to increase Maintainability in design. James Kovacevic also provides a detailed and practical overview of same topic in one of his podcasts.
Maintainability can be improved at every stage of a system’s life cycle. It just gets more expensive over time. Therefore, it is more cost effective to get it right at the start of the life cycle.
Improving Maintainability using a RAM model.
Having defined the three concepts, there is a clear relation between them. The table below illustrates this.
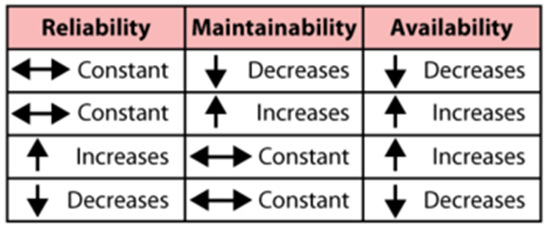
In addition to Fred’s comments above, the need for improved Maintainability often needs to be justified. The RAM model is a great tool for this. It allows us to quantify the net benefit of the changes required. For example, if the Maintainability constraint is clearly defined, different RAM scenarios can help quantify the benefits. In other words, a “before Maintainability improvement” and “after Maintainability improvement” RAM case can be run. The benefit is the difference gained in revenue or repair time. Obviously, time is always related to money so it inevitably comes down to revenue gained. Changes are not cheap and always need to be justified to senior management.
Last and by no way least, Maintainability significantly impacts the work lives of field workers. Ergonomics, stress reduction, job satisfaction, safety are a few of the many welcome Maintainability related benefits offered to those colleagues who work hard at keeping our equipment running.
What are the key components of maintainability in RAM (Reliability, Availability, Maintainability) systems, and why is the “M” (Maintainability) crucial in ensuring optimal performance and longevity?
Thanks for your question. By key components I suppose you mean elements that will influence Maintainability. These are highlighted in the third section; i.e. design, available resources and logistics.
In simple terms, Maintainability relates to the “ease” of doing maintenance. It is easier thus the equipment gets repaired “quicker”. As shown in Diagram 2, it increases availability. Less time spend on maintenance means more uptime or “optimal performance” as you might state. I am not quite sure “M” impacts longevity though it is great you raise this point. In my opinion longevity, would be influenced more by the reliability element. Remember, reliability is the probability of not failing. Longevity relates to the highest possible reliability. To increase longevity, we should focus on the “design for reliability” aspect. How do we design the equipment so that the probability of failure(s) is at its lowest.