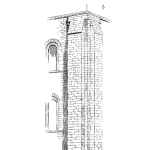
End-of-life definition
Operators need to estimate when in the future their equipment will attain their end-of-life state. Obsolescence is another word for equipment end-of life. Once they reach this stage, equipment replacement often leads to significant budgetary expenditures. In addition, if the operation has a large number of a particular equipment types, they could all reach their end-of life at the same time leading to even greater financial impact. In industry jargon, this is known as the “Tsunami” effect. Operators need to aware and prepared in order to avoid this “wave” of consequences. Managing future cash inflow and outflows happens to be crucial financial exercise in any organization. Therefore, end-of-life management in an important financial accounting exercise. However, estimating end of life this is not always as straightforward as it seems.
End-of-life estimation methods
Various factors influence equipment end-of-life. The common thread would be an economical one. In other words, there is a business continuity or operational cost associated with the end-of-life of an asset. Typically, the equipment life characteristics will define the end-of-life interval or timing. But not always as the purchase contract terms can also dictate this interval. Below is a set of 3 common approaches to defining the end-of-life stage of an asset.
1) Using Equipment life characteristics – Optimal Replacement Time technique
From an analytical standpoint, end of life would be when the equipment starts costing the operation more than it is contributing in terms of revenue. It starts failing more frequently and the cumulative maintenance costs become uneconomical. The Optimal Replacement Time technique can estimate the end-of-life time post installation. Graph 1 illustrates this technique. The more often we replace the equipment, the higher the cost.
The green curve related to replacement frequency goes up if we move to the left. Conversely the less often we replace the equipment, the higher the probability of failure thus the cost to the operation. The red curve goes up if we move to the right. Adding the cost value of those two above mentioned curves provides us with the total cost curve in blue. The minimum value on this total cost curve ultimately provides us with the optimal time to replace the equipment. This timing signals the end of the economical life of the equipment. In the Graph 1 example, replacing the equipment every 12 years leads to the lowest incurred total cost.
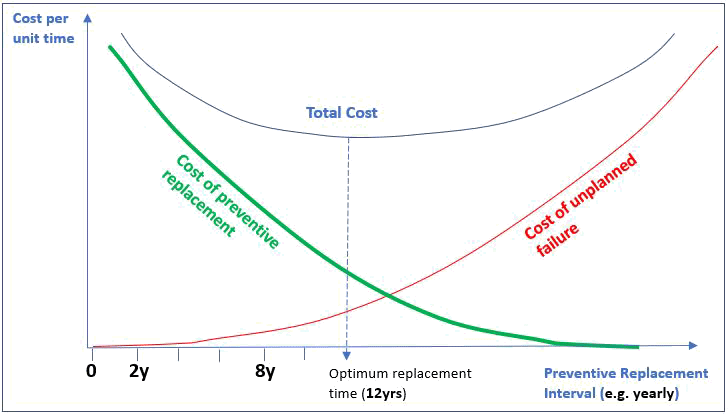
2) Using Equipment life characteristics – Failure rate curve inflection
Using life characteristics would also indicate the end of life through an inflection and rapid increase in the failure rate. Graph 2 below illustrates this be it in an exaggerated manner to enhance reader comprehension. The sudden and sharp inflection in the failure rate curve indicates that a catastrophic failure is imminent. This suggests urgent action be taken; most likely replacing the equipment.
Graph 2 – Failure rate curve indicating a sharp increase in the failure rate suggesting asset end-of-life
3) Obsolescence through contractual terms
When equipment manufacturers sell equipment, they typically commit to providing spare parts during the life of the equipment. Manufacturer spare parts are also known as Original Equipment Manufacturer (OEM) spare parts. They are of high quality as opposed to most aftermarket or non-OEM parts. Operators will choose to buy OEM spares to comply with the warranty. Choosing to use non-OEM parts could increase the risk of premature failures impacting personal safety hence operator liability for example.
However, the purchase contract often sets a lifetime limit on the supply of spares parts. The manufacturer’s business model might not allow the sale of parts beyond a certain time interval. After this time, even if the equipment has been well maintained and functioning satisfactorily, there could be no supply of OEM spare parts. Parts can be manufactured on demand or non-OEM parts used. However, those options can be both costly and risky. Advanced purchase or over stocking also comes with risks as spare parts would typically have a set shelf life. In this case, the contractual terms dictate the equipment end-of-life contrary to the equipment performance as shown in section 1) and 2) above.
Planning for equipment end-of-life
It is important for any organization to plan for the end-of life stage. This avoids the above mentioned “tsunami” effect. It also avoids end of life related catastrophic events that could jeopardize personnel, assets or business continuity. Therefore, end-of-life management should be considered in the early design stages of an operation. End-of-life is after all, part of the natural life cycle of any asset. Some elementary questions to ask at the design or commissioning stages are:
– What is my asset management strategy for equipment end-of-life?
– Can I calculate the end of life of my equipment? Or is it contractually dictated?
– Am I at risk of a tsunami wave of failures? If yes, how do I manage this?
Leave a Reply