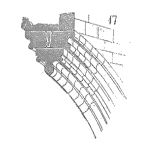
Now SFAIRP is the Criterion to Judge If You have Sufficiently Controlled Your Workplace Hazards
Risk Assessment Used to be Based on ALARP to Decide if Workplace Hazards were Sufficiently Controlled, But Today You Need to Use SFAIRP
The original OHS risk assessment process, procedures and techniques identified hazards; assessed risk; established risk controls; reduced and managed risks to ‘as low as reasonably practicable’ (ALARP), but safety laws are now changing to ‘so far as is reasonably practicable’ (SFAIRP)
Have risk, safety and reliability solutions proactively put in place, which are effective strategies to manage and control your hazards no matter where they are—inside your machinery or within your workspaces
more
Risk assessment methods address the risks in your production facility, operating equipment, business processes and employee workplaces. Discover how to use effective visual management principles and concepts to “see the risk” in your business operation and maintenance practices and procedures. You’ll cut-out dangers and hazards and get a safer, productive, more reliable site.
Often business and production situations are charged with risk and high danger that company managers don’t even realize exist. They unknowingly carry the added burden of suffering a catastrophic event which they and their people were not aware of and had not prepared for. For example, an equipment failure event occurs with a massive knock-on business consequence that they were unknowingly living with. No matter if the risk is in the workplace, or in your plant and equipment, you must have in place dependable, efficient, effective risk assessment methods to detect them, make them visually observable, categorize them, manage them, and control them.
Your business, production and operating processes are designed around things going right; just as planned. Most times that is what happens. But from time to time, usually more often than expected, things do go wrong. You need to identify those situations and plan for, prepared for, and know exactly what to do during those times! Risks and consequences, causes and effects are continuously with you. You must recognize all hazards about your company for what they are.
What response do you make when an employer says, “We have not had an injury in our company in 5 years. Why would I need to spend money on an event that may never occur, and given our history, it has not?”
This question is one that company managers ask all the time. The intent in asking it is reasonable, but by asking it they show great misunderstanding of safety risk, a severe lack in their knowledge of the Occupational Safety and Health Laws and Regulations, and also raise doubts about their duty-of-care morality.
In order to build the case for the correct response it needs the full risk equation. Usually you see the risk equation written in the form:
Risk = Consequence x Likelihood
The full risk equation for an incident would show Likelihood fully expanded, and the complete risk equation actually is:
Risk = Consequence of the Event x (Frequency of Opportunities x Chance of Failure at each Opportunity)
Only when one of the components in the equation is zero will Risk truly be zero.
What our Employer means is they have not suffered the event consequence in 5 years. That statement does not actually prove there are no opportunities to have the event, or that there is no chance of an opportunity progressing to failure. Until we know the Frequency of the Opportunities, and the Chance of each Opportunity becoming an unwanted Failure Event, the Employer cannot know their real risks.
Workplace OHS Risk Assessment: How to Protect Yourself in a Minefield of Errors!
My comment to an Employer who has not suffered a disastrous event for five years is, “Most likely you have been lucky. You’re probably still carrying a very serious risk that you cannot see!”
Here are some more thoughts in response to the question.
- If the last injury was 5 years ago we can show them on the risk matrix they sit between ‘likely’ and ‘possible’. It is not until 30 years pass since the last incident before the event is rated ‘unlikely’ (but it still can happen).
- Has he counted the Number of Opportunities for injury in the operation? Has he gauged the Chance each type of Opportunity will progress to an injury? What range of Consequences could each Opportunity become—from nil to what maximum cost? How often are the precursors happening, which up until now have not become a worst possible event? If there has been no injuries, it is worth asking what other unwanted events are happening in the Operation that are forerunners to an injury and count their historical frequency? Big problems grow from small problems that are not properly addressed in time.What is not being done in the Company as often as it ought to be done to protect the Employer’s operation and people? Has the Employer simply been lucky for 5 years, or is their success an effect of using the right protection methods? We suggest you get safety professionals in and audit your occupational health and safety (OHS) system to find out how good it really is performing.
- An accident or injury is a probabilistic situation—it can happen, but it may not happen as well. Risk comes from situations that occurred in the past and from situations that will happen in the future. No one knows the future—you cannot predict it, you can only make a forecast. If you want to help the Employer understand the full risk implications they carry, they must ‘see’ the changing effect of the full Risk Equation. It is best to use a visual representation marked on a risk matrix (as shown in the image below) so they can get an understanding of the whole range of risks they carry. The other ‘risk visualisation tool’ is to use a Risk Cost Calculator.
- Has the Employer considered the Event risk over a 10 year period? (Five years is far too short to think an OHS Management System is performing well.) What about over a 20 year time frame—does the Employer believe an injury will never happen in the next 20 years? Would they be willing to guarantee there will be no injuries for the business’ entire remaining lifetime?
- It’s certain that the Employer gets their car serviced. Why do they ensure to service their car? Because they don’t want a failure when they need the car! They know that a car never serviced will eventually lead to a state where a breakdown will happen. What they don’t know is when the failure will happen, but they know it will occur if the service is never done. To say there has been no injuries for 5 years in a company is meaningless, until you also know the capability of their OHS Management System to keep the business workplaces safe.
- Everyone has their own risk boundary. Some managers are risk averse and others are risk takers. If you get an Employer who is also a base jumper on the weekends, or is a rock climber, they are great risk takers by nature. They will probably also take greater risks with their business and the health and safety of the people in their workplace.We all have a risk boundary we work within. If you drive a car there is a chance you will die—we have road deaths regularly, and it could be you next. But the level of risk from road death is well under our risk boundary and so we all do what may kill us. Managers make risky decisions all the time and do not even know the risk they have taken. A manager that says, “I have not had an injury within our company in 5 years. Why would I need to spend money on an event that may never occur and given our history, it has not?” probably does not know what level of risk they carry! They need to be educated more on the ways to fail at doing risk assessment and management, and the seriousness of their duty of care to the organization and its people.
Until our Employer says – “I have not had an injury within our company in 5 years. I never want such an event to occur for the rest of our company’s history. How can I accomplish that?” – they have not understood their duty of care responsibility to their workforce and to Humanity.
Risk Assessment from ALARP to SFAIRP
The workplace risk assessment process is to determine the most practicable risk control strategies to fully address all hazards. At every stage of the risk assessment process it is necessary to balance the two principles that now apply to risk mitigation selection – the old ‘as low as reasonably practicable’ (ALARP) and, the newer ‘so far as is reasonably practicable’ (SFAIRP) acceptable risk levels.
All workplace OHS risk must be as ‘as low as reasonably practicable’ (ALARP). That level of risk control has been found to allow high consequence, low likelihood situations to remain after the risk assessment was done. Requirements are now changing to ‘so far as is reasonably practicable’ (SFAIRP). SFAIRP risk control concepts were developed as the result of common law court judgments and go further than ALARP. (Don’t ever be in the situation where a judge say, “You may have assessed the risk as negligable, but now seven people are dead!”)
ALARP risk control strategies are those selected to reduce workplace OHS risk to a reasonably practicable level giving consideration to the risk rating, the estimated cost of corrective actions, and the chance of real health and safety risk reduction success. SFAIRP risk control strategies go further than ALARP and require you to apply all risk mitigations that need to be implemented to get the required risk level, regardless of cost. Whereas ALARP risk assessment lets you argue that you have done sufficient to get the risk level low enough, SFAIRP risk assessment says that until the risk level is low enough, you have not yet done sufficient to mitigate the risk.
ALARP risk control delivers workplace safety risk at a ‘reasonably practicable’ level taking into consideration the risk rating, the cost of corrective actions, and the odds you will get successful OHS risk reduction. SFAIRP requires you to continue implementing risk mitigations until you are sure to get the required risk level, no matter the cost. ALARP lets you stop when you think the risk level is low enough, SFAIRP makes you continue until the risk is clearly mitigated low enough.
Develop a visual way of explaining ALARP and SFAIRP risk assesment levels to your employees, engineers and managers using the modified risk matrix shown above. To explain to an Employer what is really happening with their equipment risks, you need to make the hazard changes visual by mapping the progression of an event across the risk matrix. In the risk assessment plot image above, the conveyor belt roller risk progresses from being maintained properly for $1,000/year, to the complete burning of the conveyor system in a $2,000,000 event. It’s easy to see the business risk change. And if the worst event occurs, then it’s clear that the operation will suffer a total disaster.
If you are the manager of that operating site, do you say, “A once in 30 year event will not happen on my watch.” Or do say, “Keep the maintenance up on those conveyor rollers and replace any siezed rollers while the operation is under my watch?”
The risk assessment and risk progression mapping for workplace injury or production disasters in your company can be just as clearly done for every activity you do on your site.
All the best to you,
Mike Sondalini
Director
Lifetime Reliability Solutions HQ
Leave a Reply