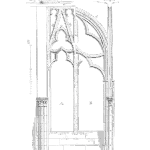
This topic is provided by – Graphic Products, Inc. Contact
info@graphicproducts.com
Copyright © 2000, 2001 All rights reserved.
Abstract
The 5 s method of operation – A Five S program focuses on having visual order, organization, cleanliness and standardization throughout the workplace and the operation. It is a structured method to put operators and maintainers in control of what they do.
Keywords: sort, systemize, standardise, self-discipline
Sort – Systematize – Sweep – Standardize – Self-Discipline “Sorting” means to sort through everything in each work area. Keep only what is necessary. Materials, tools, equipment and supplies that are not frequently used should be moved to a separate, common storage area. Items that are not used should be discarded.
Don’t keep things around just because they might be used, someday.
FIVE S – Step One: Sorting is the first step in making a work area tidy. It makes it easier to find the things you need and frees up additional space.
As a result of the sorting process you will eliminate (or repair) broken equipment and tools. Obsolete fixtures, molds, jigs, scrap material, waste and other unused items and materials are disposed of.
FIVE S – Step Two: Organize, arrange and identify everything in a work area for the most efficient and effective retrieval and return to its proper place.
Commonly used tools should be readily available. Storage areas, cabinets and shelves should be properly labeled. Clean and paint floors to make it easier to spot dirt, waste materials and dropped parts and tools. Outline areas on the floor to identify work areas, movement lanes, storage areas, finished product areas, etc. Put shadows on tool boards, making it easy to quickly see where each tool belongs.
In an office, provide bookshelves for frequently used manuals, books and catalogs. Labels the shelves and books so that they are easy to identify and return to their proper place.
The objective in this step is: A place for everything and everything in it’s place, with everything properly identified and labeled.
This means there are two important parts to Systematic Organization – putting everything in its proper place and setting up a system so that it is easy to return each item to its proper place. The second part is where good labeling and identification practices are important. Both the equipment/tools and materials you use, as well as their proper storage locations, need to be clearly identified and labeled.
Systematic organization not only refers to individual work areas. Your overall facility should also be systematically organized, including the proper placement of easy-to- understand labels and signs. Piping, valves, control panels, major equipment, doorways, minor equipment, instruments, storage areas, offices and files should all be clearly identified.
FIVE S – Step Three: Once you have everything, from each individual work area up to your entire facility, sorted (cleaned up) and organized, you need to keep it that way. This requires regular cleaning, or to go along with our third S, “shining” things up.
Regular, usually daily, cleaning is needed or everything will return to the way it was. This could also be thought of as inspecting. While cleaning it’s easy to also inspect the machines, tools, equipment and supplies you work with.
Regular cleaning and inspection makes it easy to spot lubricant leaks, equipment misalignment, breakage, missing tools and low levels of supplies. Problems can be identified and fixed when they are small. If these minor problems are not addressed while small, they could lead to equipment failure, unplanned outages or long – unproductive – waits while new supplies are delivered.
When done on a regular, frequent basis, cleaning and inspecting generally will not take a lot of time, and in the long run will most likely save time.
FIVE S – Step Four: To ensure that the first three steps in your Five S program continue to be effective, the fourth step is to simplify and standardize.
The good practices developed in steps 1 through 3 should be standardized and made easy to accomplish. Develop a work structure that will support the new practices and make them into habits. As you learn more, update and modify the standards to make the process simpler and easier.
One of the hardest steps is avoiding old work habits. It’s easy to slip back into what you’ve been doing for years. That’s what everyone is familiar with. It feels comfortable.
Use standards to help people work into new habits that are a part of your Five S program.
Any easy way to make people aware of, and remind them about the standards is to use labels, signs, posters and banners.
Five S – Step 5: The final step is to continue training and maintaining the standards.
Have a formal system for monitoring the results of your Five S program.
Don’t expect that you can clean up, get things organized and labeled, and ask people to clean and inspect their areas every day — and then have everything continue to happen without any follow-up.
Continue to educate people about maintaining standards. What there are changes – such as new equipment, new products, new work rules – that will effect your Five S program and adjustments to accommodate those changes.
Think of this step as sustaining the benefits you are getting from your Five S program.
If you found this interesting, you may like the ebook Process Control Essentials.
Leave a Reply