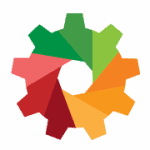
Improving the reliability of performed maintenance work helps in the refinement and improvement of policies that shape a cost-effective maintenance strategy that aims to address dominant causes of asset failure.
Before we continue, we have to define how reliable maintenance looks like. In the context of this article, we will define it as consistently performing adequate maintenance in the required time frame. In other words, it means performing good maintenance work while respecting due dates.
Improving the reliability of maintenance work directly improves the reliability of the asset. After all, assets that are maintained well are less likely to experience failure and produce high levels of defects.
Let’s discuss five different ways in which an organization can improve the quality and consistency of performed maintenance work.
1. Adopt CMMS and Improve Work Accountability
Computerized maintenance management systems aid maintenance programs by developing high-level goals for tracking costs, setting benchmarks, and monitoring efficiency on a day-to-day basis.
CMMS enhances accountability within an organization by maintaining records of the technicians who performed maintenance tasks on an asset, the costs incurred, parts used, and the amount of time spent performing the work. When you have high work accountability, it is easier to spot issues and maintain a high level of maintenance performance.
In addition to that, with a CMMS, technicians have direct access to asset history, maintenance logs, and maintenance checklists, all of which can help them to do a better job.
2. Ensure Proper Training of Maintenance Personnel
Quality maintenance is performed by qualified personnel who need to be wary of the technical functionality of machines. Bigger plants can have a lot of different assets that developed different kinks over time.
Early on, newly hired maintenance mechanics need to be properly trained and have proper oversight to ensure that the quality of performed maintenance work stays consistent. Organizations can leverage on-site training to ensure the maintenance team garners expert skills with the tools and technologies that relate to reliability-based maintenance processes for all assets.
3. Create Balanced Maintenance Schedules
Do you know who performs mistakes? People who are stressed, physically and/or mentally drained, and those who are not given adequate time to finish tasks that have been assigned to them.
Balancing maintenance schedules enhances the reliability of maintenance work and can be used to alleviate some of those potential issues. A well thought out maintenance schedules ensure that the maintenance workload is balanced between shifts and technicians. Modern CMMS solutions offer easy to use maintenance calendars that offer a visual overview of the volume of required maintenance work. This makes it much easier to develop fair and balanced schedules.
Approaching the scheduling from a holistic point of view improves reliability by pairing together more and less experienced technicians and ensuring they have the right tools and enough time to complete scheduled tasks.
4. Standardizing Maintenance Work
Maintenance encompasses a wide range of complex activities, including daily routine checks, repairs, and corrective maintenance. As such, consistent results are hard to achieve without a comprehensive set of maintenance standards embodying technology and best practices.
The most straightforward way to standardize maintenance work is through ISO certifications, writing SOPs, creating detailed maintenance checklists, and clearly outlining safety guidelines.
5. Address the Right Failure Modes
Performing regular preventive maintenance work is great. Ensuring that work is done to a high standard and on time is even better. Unfortunately, all of that work is futile if it does not address the right failure modes.
Besides helping with FMEA and RCM, having a reliability engineer on hand can ensure that the work your maintenance team is doing actually addresses the potential weaknesses of that item. Maintenance teams have limited time and that time is best spent addressing those items that have the highest chance to cause a malfunction.
To ensure you are not doing excessive maintenance, using condition monitoring sensors and equipment can help more accurately track deterioration signs on critical assets. Again, you should focus on tracking those deterioration signs that are most likely to lead to a breakdown (or all if you have enough resources for that).
Managing failure requires an in-depth understanding of failure metrics, including the mean time to failure, mean time between failures, mean time to repair. When done right, this also allows maintenance managers to prioritize preventive and routine work on certain assets.
When you combine everything stated here, you can be confident that the maintenance team is doing quality maintenance work that will be reflected in asset performance and a decreased number of unexpected breakdowns.
Leave a Reply