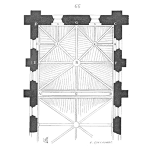
by Alan Ross, first posted November 30, 2016
A title like this is supposed to make you curious about two things: First is whether you are aware of these myths and second is if you are aware of them but wrongly believe them. They are myths after all.
Working in the reliability field with a focus on electrical systems, I have become increasingly aware of how many people believe in one or more of these myths and, more strikingly, stake their production uptime and even their career on them. I am not over-exaggerating. It is a big problem we seldom hear about because following these myths has led to a significant increase in the number of transformer failures with a corresponding dramatic increase in the cost of those failures.
So let’s get started. Be honest about it. If you know these are myths and are thinking the right way, then you will no doubt have just verified your prowess. On the other hand, if you believe some or all of these myths, then now is the time to recalibrate and set the record straight.
Myth #1 – Replacing an older transformer will eliminate the risk associated with a failure and potential downtime.
While this is one of the myths that sounds logical, it also leads to false assumptions that impacts the credibility (and quite possibly career path) of the electrical reliability professional who relies on it.
As a mechanical engineering student at Georgia Tech in the late 1960s and early 70s (am I dating myself?), we used slide rules for doing calculations and executed designs on drafting tables with expensive mechanical pencils. Then along came Texas Instruments, and soon we gave up our slide rules for the TI 1000 or whatever was the latest update available. Today, transformers are designed with the aid of computer modeling and a heavy emphasis on reducing costs while building in compliance to the nameplate rating.
Several years ago, SDMyers was commissioned to manage the installation of a large GSU. The crane rating of the new transformer, built to the same nameplate rating as the old unit, was 10,000 pounds lighter than the crane rating of the unit we were replacing. What was removed to reduce the weight by 5 tons? Mostly it was oil, paper, copper and maybe some steel. In reality, that particular older transformer was overbuilt, something we have come to rely on throughout industry and something that is beginning to create consequences beyond what technicians typically have planned for.
I am not saying that the quality of the new units is compromised. I am saying that we have become complacent with and reliant on older assets that were significantly more reliable than expected. From a reliability standpoint, we are seeing this throughout our productive systems. But given how poorly most professionals have maintained the current fleet of assets, practicing the same PdM or PM practices with newer units is nothing short of a recipe for failure.
Myth #2 – Transformers have no moving parts, so there is little you can do other than test the oil for gases.
This myth has two problems. Although conducting a dissolve gas analysis is valid, it is not your only issue. Manufacturers of DGA monitors tell us that their industry is expected to double every year for the foreseeable future. Why? Because if it is good to conduct a DGA oil test once a year—or even once a quarter—then daily monitoring is even better, right? While that may be right, it also masks a more serious issue.
Sampling transformer oil is the gold standard for understanding what is happening inside the transformer, but much more is at stake than just DGA. Oil quality is connected to paper quality and paper quality determines the life of the unit.
A transformer with little or no fault gases may have high moisture or high acid build up. The Liquid Screen Test and Karl Fisher are just as important as the DGA, yet our decades of data point to the reality that a majority of industrial transformer owners do not process that oil to remove acids or do anything about remediating moisture.
A recent study of over 1,500 failed transformers over 500kVa provided the following evidence for Predictive Maintenance (PdM) on transformers:
This is quite telling and should be convincing to those in charge of maintenance budgets who may be “penny wise but pound foolish.” It is never too late—or never too early, for that matter—to use the diagnostics and recommendations from your oil testing to employ good PdM principles. Most professionals do it automatically for all other production equipment yet seldom do it for transformers. That is until we have a failure that shuts down a plant for days or weeks and gets the C-level attention that we would all rather avoid.
The number of significant losses from transformer failures is hard to quantify since most are reported only to the insurance company. Fortunately, we work with insurance carriers and brokers, and we see the amazingly high losses that could have been prevented had proper PdM been applied. Hot oil cleaning a transformer is one of the least expensive and most effective maintenance practices you can make. That leads us to…
Myth #3 – Oil Processing is basically the same from vendor to vendor, so go for the lowest price.
There are four considerations when choosing a vendor to process the oil in your transformer:
- Any lapse in safety while on your site will affect your company. The amount, quality and timeliness of the training required of the crews, coupled with the proper tools and equipment, are primary safety considerations. When implemented through Best Practice processes and documented correctly, you can be assured that Safety First becomes more than a catch phrase. It really does matter.
- Crew competence. The better, more experienced the crew, the better the outcome. The quality of the work depends in large part on the quality of the crews.
- All equipment is not created equal. Is there a difference between a $500 pump and a $1,000 pump? Most likely, and usually the difference is in the quality, reliability and endurance of each pump. In a competitive marketplace with competent procurement departments, equipment manufacturers cannot simply provide the same quality at a higher price. There must be an advantage based on quality. There is no greater evidence of poor quality than a large oil slick near your transformer when a processing rig drives away.
- Clean oil means they cleaned and dried the transformer. Think about it: In the case of moisture, there is usually 99 times more moisture in the paper than in the oil, so drying the oil does not dry the paper. Give it 3 to 6 months and the oil will be wet again because of the natural migration of moisture from the paper to the oil. The same is true of acids. The amount of heat and the number of passes dictate whether the transformer is clean or not.
Myth #4 – Senior management understands the risks from relying on the old installed base and is including that in their capital planning.
If only this were true. In the past three years, as I have focused more and more on the corporate reliability of electrical systems, I assure you that we are just now beginning to grasp the risks.
At one recent planning session where we reviewed all of the critical units for a large metals processing concern, we realized that the average age of their most critical transformers was over 30 years…and that was their average. Some were over 35 years old. Their OEM-suggested lifespan was actually closer to 20 years, and a study by a prominent retired transformer insurance executive predicted failures of this class of transformers happening in approximately 19.8 years after installation. What is wrong with this equation?
It was not until one of these antiques failed, causing millions of dollars in lost production and a lengthy downtime, that senior management made it a priority. Within weeks of this meeting, another major company in the refining industry suffered a loss from a transformer failure that totaled over ten million US dollars. To make matters worse, that transformer was only 13 months old, having recently transcended its warranty period.
These are real problems that are being repeated in every major industry that relies on electrical power. How many smaller companies have only one or two transformers, or those that run data centers where the loss of power, even for hours, could lead to financial losses into the millions of dollars? I hope everyone reading this article forwards it—even anonymously, if needed—to their head of Risk Management or even to their CEO or COO. The risk is real, and the clock is ticking.
Myth #5 – We’ve checked with transformer manufacturers, and replacement lead times for unit replacement is not a problem.
This is a myth with some amount of truth to it, but just enough to make it dangerous. While there is more competition in the world for the supply of transformers, the more unique a unit is, the more likely an extended lead-time will be experienced.
I recently worked with a customer who thought he could replace a rectifier transformer within three months. As he developed the specs for bid based on the nameplate, he found out that this particular type of unit had a lead time closer to 12 months. “Houston, we have a problem.” Thankfully, the current unit, while certainly exhibiting signs of eminent demise, could be strengthened through PdM to last until the new unit arrives. It is still pretty much a roll of the dice, however. And if the unit should fail, a back-up system would be incredibly costly.
Another issue to consider for larger units is transportation. Despite the reduced weight—which is the case among most types and manufacturers—the infrastructure of roads and bridges may be more of a problem now than when the old unit was installed. A recently documented issue reported the difficulty of getting approval to cross a major bridge—which had been categorized as “at risk”—so that the weight limit had been reduced to less than what the new unit weighed. It so happens that this bridge is the only way into the facility without going miles out of the way and possibly suffering the same circumstances. Fortunately in this instance, after a significant delay, special dispensation was given to use the bridge.
Finally, when considering replacement, the physical footprint of the unit is an important factor. In what is likely the worst possible situation I have ever encountered is a series of five transformers—all of them over 30 years old, and all behind a wall and a building that would require significant demolition just to gain access to the units. Somebody clearly messed up along the way in this case, but it is not uncommon to find cabling needs or construction needs that would considerably increase costs and extend the time for replacement. Life cycle management for transformers is very unique given how we have built in and around them over the past decades as production needs changed.
Myth #6 – The Reliability Engineer understands all this and has it covered.
At a recent reliability conference, one of the speakers mentioned in his presentation that he was so impressed with the way one of his maintenance techs performed that he promoted him to the title of Reliability Engineer. Now I don’t mean to be too snooty, but really? When did doing a good job as a technician suddenly make someone an engineer?
Reliability is one of the fastest growing areas of study at major technical universities. What makes a good reliability engineer is years of study and practical application, not simply doing a good job in maintenance. And this is one of the problems we face when implementing a good electrical reliability program. Electrical reliability is not the same as the reliability concerns on the O&M side of the plant.
The diagnostic tools and techniques used in O&M, while similar, are different enough to make electrical reliability something that requires specialized training. Life cycle planning for major assets like transformers must be approached differently. After all, how often do we replace power transformers in facilities? Usually it is in terms of decades, if not half centuries.
I can only wish the O&M reliability practices were applied to the electrical side, but unfortunately that is rarely the case. Until a unit fails and catches the attention of senior management, most of us simply drive by the substation and hope the transformer that has hummed along nicely for 30 years continues to do so.
There are well established PdM tools that, when properly used, can create transformer reliability programs. Companies in metals production, independent power producers, refineries and chemical processing are beginning to take these issues seriously by developing and implementing robust reliability programs. Corporate focus on reliability and increased pressure from the insurance industry is shining a light on the problems while creating awareness that will translate into success.
Myth #7 – Installing fault gas (DGA) monitors on my critical units will reduce the risk of transformer failures.
This is another myth that has just enough truth at the core to make it sound reasonable. While adding DGA monitors to your critical units certainly adds a level of reliability, there is so much more that can be done that will actually reduce the risk. Nothing can eliminate risk, but if we are after the highest level of assurance, then monitors are only a part of it.
First, a DGA monitor does not reduce the risk of failure; it merely let’s you know in advance that there is some sort of electrical fault taking place inside the transformer. Bushing and breaker monitors do the same thing. They don’t eliminate the failure, they just might give you more time to act before you must react.
Good oil analysis and maintenance, visual field inspection, IR at the time of the chemical test, time-based electrical testing and good training of electrical maintenance and management personnel are all practical, cost-effective and proven steps you can take to actually reduce the risk of transformer failure as well as trend the health of the unit. Monitors are just more tools in that arsenal.
The biggest caveat that comes with monitors is something we learned from an 18-month, industry-wide fault gas monitoring study conducted by SDMyers. The good news was that monitors from companies that make up more than 95% of the market worked effectively. However, there were two pieces of bad news: False positives and too much data.
Imagine 18 months of extensive, detailed data rather than just for a few days, and imagine this data from multiple monitors. Trying to store this data in the same place where you keep data for chemical testing, IR or electrical testing is short of impossible unless you have a powerful data management system. And most CMMSs are not capable of handling these volumes of input.
What happens when we have too much data, knowing that some of it is potentially false positives? Data chaos! As a result, our confidence level in that data diminishes and, even worse, we act on it only to shut down a unit that is perfectly fine. Then what happens when we don’t act on it the unit fails? When a Root Cause Failure Analysis (RCFA) is conducted on such a unit, too often—in hindsight—the unit did not exhibit any sign that it was going to fail until it actually did.
Since most failures of transformers without tap changers are due to faults down-line from the transformer, it is easy to throw up our hands and say we could not have avoided it anyway. That is much like saying that I won’t take care of my heart, and then blame my run up the staircase for my death, when I might have survived that run had I taken care of my heart in the first place. The down-line fault is only the precipitating factor to the failure; poor reliability practices were the actual cause.
Conclusion
Hopefully you did not believe in these 7 myths in the first place. Taking a closer look at electrical reliability as we maximize the productivity of our plants and facilities is just good business. Destroying these myths and replacing them with a sound and robust reliability program for our electrical system will require the same things it requires on the O&M side of the business: A commitment from upper management, sound and timely life-cycle planning, a dynamic data management system, a culture that works together to solve problems and finally, having best practices in testing, maintenance and monitoring in place that will lead to reliability.
Alan Ross is the President of the Electric Power Reliability Alliance (EPRA). He is responsible for leading the alliance to build electric system reliability in the industrial and commercial marketplace. Formerly, Alan was the Vice President of Reliability at SD Myers.
Worth reading and very practical!
Thank you, Gladson. We hope to bring you more helpful articles in the future.