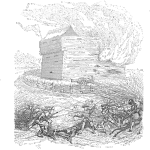
Once you decide to monitor a process and after you determine using an $- \bar{X} -$ & R chart is appropriate, you have to construct the charts.
This is not difficult and by following the 8 steps below you will have a robust way to monitor the stability of your process.
1. Determine Sample Plan
Determine the sample size, n, and frequency of sampling. Consider the cost of sampling, required resources, and balance with minimizing time (and produced units) between measurements. Of course, more samples and more frequent measurements is better statistically.
2. Collect initial set of samples
Shewhart recommended 100 individual units in 25 samples of 4 each. Basically, we want enough samples to create reasonable estimates of the mean values of $- \bar{X} -$ and R. Keep the data in time sequence following the time of the sample selection, which should be in the same order of manufacture.
3. Calculate $- \bar{X} -$
Calculate the average for each set of samples. This is the $- \bar{X} -$ for each sample.
4. Calculate R
Calculate the range of each set of samples. This is the difference between the largest and smallest value in the sample.
5. Calculate $- \bar{\bar{X}} -$
Calculate the average of the $- \bar{X} -$’s. This is the centerline of the $- \bar{X} -$ control chart.
6. Calculate $- \bar{R} -$
Calculate the average of the R values. This is the centerline of the R control chart.
7. Calculate Control Limits
First, calculate the R chart limits.
$$ \large\displaystyle UC{{L} _{R}}={{D} _{4}}\bar{R}$$
$$ \large\displaystyle LC{{L} _{R}}={{D} _{3}}\bar{R}$$
Note: for a sample size, n, of less than 7 the lower limit is zero.
The $- {{D} _{3}} -$ and $- {{D} _{4}} -$ constants are found in tables or calculated with the following formulas.
$$ \large\displaystyle {{D} _{3}}=1-\frac{3{{d} _{3}}}{{{d} _{2}}}$$
$$ \large\displaystyle {{D} _{4}}=1+\frac{3{{d} _{3}}}{{{d} _{2}}}$$
where,
$$ \large\displaystyle {{d} _{2}}=\int _{-\infty }^{\infty }{\left[ 1-{{\left( 1-{{\alpha } _{l}} \right)}^{n}} \right]}d{{x} _{l}}$$
$$ \large\displaystyle {{d} _{3}}=\sqrt{2\int _{-\infty }^{\infty }{\int _{-\infty }^{{{x} _{l}}}{\left[ 1-\alpha _{l}^{n}-{{\left( 1-{{\alpha } _{n}} \right)}^{n}}+{{\left( {{\alpha } _{l}}-{{\alpha } _{n}} \right)}^{n}} \right]}}d{{x} _{n}}d{{x} _{l}}-d _{2}^{2}}$$
and,
$$ \large\displaystyle {{\alpha } _{l}}=\frac{1}{\sqrt{2\pi }}\int _{-\infty }^{{{x} _{l}}}{{{e}^{-\left( \frac{{{x}^{2}}}{2}\ \right)}}}dx$$
$$ \large\displaystyle {{\alpha } _{n}}=\frac{1}{\sqrt{2\pi }}\int _{-\infty }^{{{x} _{n}}}{{{e}^{-\left( \frac{{{x}^{2}}}{2}\ \right)}}}dx$$
n = sample size
A Table of Constants speeds up the calculations.
n | A2 | D3 | D4 |
---|---|---|---|
2 | 1.880 | 0 | 3.267 |
3 | 1.023 | 0 | 2.575 |
4 | 0.729 | 0 | 2.282 |
5 | 0.577 | 0 | 2.114 |
6 | 0.483 | 0 | 2.004 |
7 | 0.419 | 0.076 | 1.924 |
8 | 0.373 | 0.136 | 1.864 |
9 | 0.337 | 0.184 | 1.816 |
10 | 0.308 | 0.223 | 1.777 |
Be sure to plot the data on the R chart and if not in control, before continuing with building the control chart, work to bring the variability of the process under control.
For the $- \bar{X} -$ chart limits use
$$ \large\displaystyle UCL=\bar{\bar{X}}+{{A} _{2}}\bar{R}$$
$$ \large\displaystyle LCL=\bar{\bar{X}}-{{A} _{2}}\bar{R}$$
where,
$$ \large\displaystyle {{A} _{2}}=\frac{3}{{{d} _{2}}\sqrt{n}}$$
8. Plot the data
With the control limits in place, gather samples, and plot the data. Look for special or assignable causes and adjust the process as necessary to maintain a stable and in control process.
formulas from 2002, Manual on presentation of data and control chart analysis, ASTM International, West Conshohocken, PA.
Related:
8 Steps to creating an X-bar and s control chart (article)
Chance of Catching a Shift in a Control Chart (article)
Selecting Control Charts (article)
Fred, nice summary. Merry Christmas!
Thanks Dan,
And, Happy Holiday to you!
Cheers,
Fred
Nice job on the step-by-step for the X-Bar and R-Chart calculations. They follow exactly the same steps and procedures as my Master Black Belt study notes. I learned how to do this in college using paper, pen, and a calculator; no software was allowed.
If I do use software, the answers are wrong anyway so I just use pen, paper, and my calculator at work.
Thanks – the steps are pretty common and I think it goes back to the early descriptions of control charts. Like you I learned much of this without computers, and tend to work out the math by hand before turning to a computer for the repetitive work. cheers, Fred