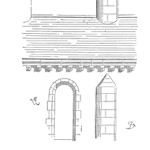
The Plant and Equipment Wellness Way was designed to quickly create Operational Excellence success. You can only get the Plant Wellness Way from LRS Operational Excellence Consultants.
The Plant Wellness Way (PWW) puts into companies the reliability processes, skills, paradigm and culture that creates world class reliability and operational excellence. Since 1985 all that is needed for operation excellence success has been known. What was not available until the Plant Wellness Way methodology, was a solution to design and build a business system with the optimal processes needed for operational excellence.
LRS Operational Excellence Consultants form a working partnership with clients when they adopt PWW. We bring you the expertise that puts your operation into the top decile of performance. You’ll have a world class operation in the top 10% of your industry. But it won’t stop there—it’ll get continually better until you are the most profitable and the rest are left way behind you.
The new operating profits you get come from:
1. PWW generates extra plant availability through the standardized use of optimum reliability, operating and maintenance practices, a big reduction in human errors, and the paradigm shift to a reliability and operating risk adverse mentality. You have shorter turnarounds delivering properly cared for equipment that operates better for longer between shutdowns. Over a year you can expect PWW practices to reduce planned outages by at least 25%, with each one of lesser duration, than without using PWW. (If your operation is running at about or below 85% Uptime we expect to get you to 90%. When you become a very good PWW operation you’ll get even higher availability.)
2. Unexpected breakdowns caused by wrong paradigms and practices will fall 90%. 9 out of 10 breakdowns you now suffer will either not happen again, or will be planned and scheduled work. For 9 of every 10 breakdowns now happening your can expect to recover some ten times their direct maintenance costs as more operating profit.
3. Less people are needed in your operation since far fewer production and plant problems happen. The work crews are smaller, and you need fewer supervisory and technical support staff, because the team work structure you use brings powerful operational research, engineering and reliability knowledge and skill synergies. For every 10 people in standard plant manning you can expect only 8 with PWW.
4. On top of the breakdowns you won’t have any more, our reliability strategy and tactics approach will bring an additional 20% less annual maintenance cost for the life of the plant compared to using RCM techniques and the usual organisational structure and procedural practices. Every year you’ll keep this in-built 20% less maintenance cost, plus get extra production, from your reliability creating organisational structure, methods and personal behaviours of the PWW methodology.
5. There will be a lower total inventory of spare parts to hold in your store. What spares are carried will be specifically matched to the equipment wear rates so spares are only kept for high maintenance equipment and highly critical plant. Your people will monitor plant and equipment stress and wear and forecast when parts need to be replaced so they can put orders on suppliers in good time and not need to keep those parts yourself. Parts inventory savings of 15% would be expected compared to an operation not using PWW methodologies.
6. Through the use of PWW imbedded stress reduction operating practices the degradation rate of equipment will be minimised and be more predictable. Production plans are far more certain to be achieved because equipment is not overstressed since PWW reliability creation methods and predictive monitoring are built into all the standard operating practices used company-wide. With PWW methods your production throughput will continually meet design specification and planned deliveries will be highly certain, thereby building a great reputation with Customers.
7. Less management time is used to run the operation because PWW standard operating practices greatly reduce day-to-day problems. Substantially fewer management hours need to be spent in a PWW culture operation—in the order of half the management time of non-PWW sites, since the workplace teams self-manage and have the capability to make excellent business decisions.
8. The imbedded PWW reliability methods, culture and paradigms ensure your people proactively seek and adopt advantageous technologies and practices to simplify and hasten what they do so you rapidly move ahead of your competition and create ever growing operating profits.
9. With PWW working brilliantly for you at your first site it will be easy and quick to roll the Plant Wellness Way methods everywhere across your company. You will have a sure operational excellence solution to world class reliability, operations and maintenance performance that is consistently being improved. You might even want to buy-out your competition with all the extra money you make from PWW and take over their operating plants and market share.
To get those benefits the PWW solutions need to be used in your operation and not left on the design and modelling pages and spread sheets. Training your managers, engineers, maintenance, and operations people in PWW methods has to be part of our deliverable if you want all the operating profits that PWW can produce. If we design the world’s highest availability production plant and operation excellence solution for you on paper, but the design is never put into actual practice in your company, then you cannot get the full benefits of PWW because it’s not actually in use.
How long it will take LRS Operational Excellence Consultants to design, review, prepare, train and implement PWW in your operation depends on the type and size of the operation you want to make into a world class decile site. The process we follow needs a minimum of three specialists from LRS Consultants. It can take from 2 to 6 months, as we only progress to the training phase once both you and we are sure your implementation will be a great success. The duration can be shortened by bringing more specialists into the LRS Consultants Team and making your people more available during the design and review phase works.
I’m sure that putting the Plant Wellness Way into any of your operations will translate into a very good ROI for you in the 12 months following implementation. After that it only gets better.
If you have questions about the above, simply contact your nearest LRS Operational Excellence Consultants office for answers.
All the very best to you and your company’s future,
Mike Sondalini
Director
LRS Operational Excellence Consultants
Leave a Reply