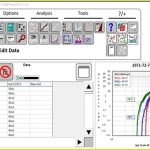
Barringer Process Reliability (BPR) is a production analysis methodology quantifying the performance of a plant or operating unit on a strategic level. Invented by Paul Barringer, it is also known as “the factory on a single page” analysis. His objective was to provide busy managers with a visual tool to assess and quantify the performance of their production plant with simple graphics and a set of key performance indicators. Without getting them to read tedious reports or get bogged down into details relating to performance issues. Once the strategic overview established, the manager would assign his team to “get down in the weeds” and address poor performance.
The underlying mathematical concept for BPR is the Weibull Statistical Distribution. Daily Production data randomness can be modeled by a Weibull distribution. The Weibull distribution allows for straight lines in logarithmic plots, leading to easy performance evaluation and loss quantification.
BPR is not intended to go into the details of the losses or low production capabilities. It remains at a high level (the 10,000ft view). However, it is still able to benchmark, quantify production losses as well as opportunities for improvement. It also has the unique ability to measure quite precisely the variability in production output.
One of the biggest advantages of BPR is that the only input required is daily production values. Such as the daily widget production values in a widget manufacturing plant. Or daily crude oil barrels processed in a refinery. This makes BPR easier to perform compared to traditional reliability analysis which requires specific and not always readily available records.
BPR plot example
Course Navigation Instructions Video
Thanks for creating this training, hope I can learn and implement the learnings.
Regards,
George Revello
You are very welcome George and thanks for your interest in my work. Let me know if there is any ways I can assist. If you have data you want to share I’d be happy to look at it. In the training I provide a technique to share data so that the confidentiality is not impacted.