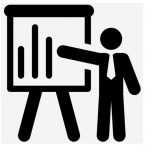
What strategies can be used to reduce severity risk in an FMEA?
“However beautiful the strategy, you should occasionally look at the results.”
Winston Churchill
strategy
The Oxford English dictionary defines “strategy” as “a plan of action or policy designed to achieve a major or overall aim.”
Reference the article Understanding FMEA Severity Risk – Part 1 which discusses how Severity is defined and applied in FMEA.
What are “action strategies to reduce severity risk” and how are they used in an FMEA?
Severity risk is represented by the severity ranking. Using a severity scale of 1 to 10, high severity would typically mean 9s and 10s, at a minimum.
The FMEA team must review and fully understand all the high-severity issues, and address them with effective actions, to ensure those issues do not occur within the life of the product or manufacturing process.
There are at least four types of strategies that can be employed by an FMEA team to address high-severity risk:
- Design for fail-safe
- Design for fault tolerance
- Design for redundancy, and
- Design for early warning
When the FMEA team encounters a failure mode with an effect that is high severity, where possible, the FMEA team should recommend one or more action strategies that reduce the severity. Use of one of these four strategies can accomplish that objective.
As can be seen from the titles of the strategies, all four are design related. It is a fact that that reducing severity risk requires a design modification. Directly below is a definition and example of “Design for fail-safe.”
Design for fail-safe
A fail-safe design is one that, in the event of failure, responds in a way that will cause minimal harm to other devices or danger to personnel. Fail-safe does not mean that failure is improbable; rather that a system’s design mitigates any unsafe consequences of failure. In FMEA language, fail-safe reduces the severity of the effect to a level that is safe.
Example: Laminated safety glass for windshields prevents injury from glass shards. The windshield can fail, but in a safe manner.
Each of the four strategies are defined, with multiple examples, in the book Effective FMEAs.)
Multiple strategies to reduce risk
In most cases, addressing a high-risk issue from an FMEA requires the use of multiple tasks. These tasks are recorded in the Recommended Actions column.
Below is an example of the use of Recommended Actions to reduce severity risk, as well as risk from occurrence and detection. It is an excerpt from a fictional Design FMEA on a projector lamp.
Take a look at the second failure mode “lamp shatters.” This failure mode has an effect with severity 10. The first Recommended Action: “Install additional plastic shield on projector to ensure no injury to user if glass shatters” can potentially reduce severity from 10 (potential for injury) to 8 (complete loss of performance).
[Note the multiple actions to address this high-severity issue.]
FMEA Tip # 1
Tip: Always review high severity issues with management. Both management and the FMEA team must agree that everything possible has been done to prevent safety problems within the design life of the product or during the manufacturing process.
FMEA Tip # 2
Updated FMEA standards will be including a supplemental FMEA called FMEA-MSR. MSR stands for Monitoring and System Response. FMEA-MSR is a supplement to a Design FMEA that provides a way to identify and justify actions to reduce severity ranking, in certain circumstances. This new supplemental FMEA will be the subject of a future article in the “Inside FMEA” series.
Problem
A fault-tolerant design is a design that enables a system to continue operation, possibly at a reduced level, rather than failing completely, when some part of the system fails. In FMEA language, fault-tolerance reduces the severity of the effect to a level that is consistent with performance degradation.
What design feature can be added to vehicle tires that incorporates fault tolerance?
Solution
A passenger car can have “run-flat” tires, each of which contain a solid rubber core, allowing their use even if a tire is punctured. The punctured “run-flat” tire is effective for a limited time at a reduced speed.
Reader’s Question
Perhaps a future “Inside FMEA” article could examine FMEA and FMECA. From my research, it appears FMECA brings in another element of quantitative analysis. Is this correct? What are the true differences?
Answer to Reader’s Question
Simply stated, a FMECA is an FMEA with the added step of Criticality Analysis. Criticality Analysis can take two different forms: quantitative criticality and qualitative criticality.
Quantitative Criticality Analysis is a series of calculations to rank items and failure modes according to a defined formula.
- Calculate the expected failures for each item. [This is the number of failures estimated to occur based on the reliability/unreliability of the item at a given time.]
- Identify the mode ratio of unreliability for each potential failure mode. [This is the portion of the item’s unreliability (in terms of expected failures) attributable to each potential failure mode.]
- Rate the probability of loss that will result from each failure mode that will occur. [This is the probability that a failure of the item under analysis will cause a system failure.]
- Calculate the mode criticality for each potential failure mode. [Mode Criticality = Expected Failures (for the item) × Mode Ratio of Unreliability (for the failure mode) × Probability of Loss (for the failure mode).]
- Calculate the item criticality for each item. [Item Criticality = SUM of Mode Criticalities]
Qualitative Criticality Analysis does not involve the same rigorous calculations as Quantitative Criticality Analysis. To use Qualitative Criticality Analysis to evaluate risk and prioritize corrective actions:
- Rate the severity of the potential effects of failure. The severity ranking is determined using the unique severity scale for FMECA.
- Rate the likelihood of occurrence for each potential failure mode. The occurrence ranking is determined using the unique occurrence scale for FMECA.
- Compare failure modes using a criticality matrix. The criticality matrix identifies severity on the horizontal axis and occurrence on the vertical axis.
The procedure for FMECA, including examples, is covered more thoroughly in chapter 12 of my book, Effective FMEAs.
Next Article
FMEA procedure includes assessing three types of risk: severity, occurrence, and detection. FMEA teams should attempt to reduce all three types of risk. In the next article, action strategies to reduce occurrence risk are discussed.
Leave a Reply