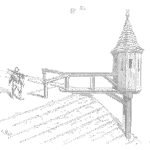
What readers will learn from this article.
- Basic theory of reciprocating compressor operation.
- Introduction into work and power calculations for a compressor.
- Explanation of Free Air Deliver (FAD).
- Issues with using rotary screw compressors.
- Issues with using reciprocating compressors.
Compressed air is one of the most used service fluids in industry. This article introduces the basic design concepts of an air compressor and discusses some of the common problems and solutions found in both reciprocating (piston goes up and down) and rotary screw (twin, meshed, rotating, helix) air compressors.
Air Compressor Theory
An air compressor takes air from the atmosphere, squeezes it into a smaller space and then ejects it into the air distribution network. The only input to the process of compressing the air is the work done by the motor to squash the air into the smaller space. Since work was done to compress the air it means that energy was used to power the work. Some of this energy is transferred into the compressed air, which being at a higher pressure than it was before compression, now has stored-up energy to be released. The rest of the energy is lost as heat into the atmosphere and into the compressed air itself. A working compressor radiates heat and the compressed air is hot at the compressor discharge.
A graph of the compression process for a reciprocating compressor can be plotted on pressure-volume (P-V) graph. Figure No. 1 shows such a plot. Point ‘d’ is the starting point of the induction stroke where the inlet valve opens and air is just being drawn into the cylinder. At point ‘a’ the piston is at the bottom of its stroke and the air has been drawn into the chamber at near atmospheric pressure and temperature and the inlet valve shuts. The volume at the bottom of the stroke is the maximum possible volume. The air is then squeezed to point ‘b’, which is near the top of the stroke and is the maximum pressure reached. At ‘b’ the outlet valve opens and the compressed air starts to flow to the receiver. Point ‘c’ is the end of the delivery stroke and all the compressed air has been ejected and the outlet valve closes. The cycle then repeats.
The area inside the envelope ‘abcd’ represents the work needing to be done on the air to raise it to the discharge pressure. The energy input to perform the work produces a temperature rise and the discharge air temperature is raised. The discharge temperature of the air depends on the compression ratio (it can easily be 150oC). Once the cylinder size and stroke are known formulas are available to calculate the work, the temperature rise and the amount of compressed air delivered into the receiver.
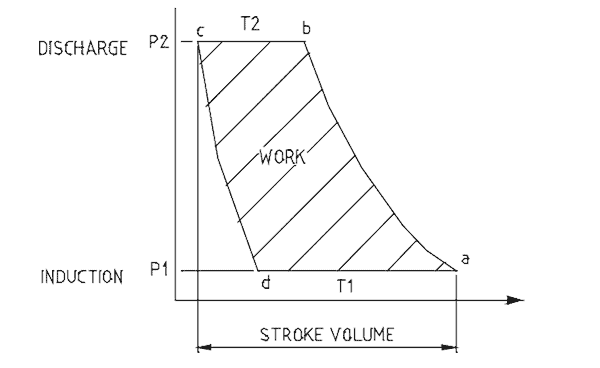
Air compressors are sized on the amount of air delivered calculated at free-air-delivery (FAD) capacity and the motor kilowatts needed to do the work. FAD is the volume of compressed air calculated back to an equivalent volume at standard atmospheric conditions of one bar (101 kPa) and 20oC. This allows comparisons between compressors as all are now measured the same way. You want the most efficient machine with maximum FAD at least power.
Rotary Screw Compressor Issues
Rotary screw compressors produce large volumes of air (FAD’s of 100’s of cubic feet per minute, CFM) at low pressures, typically 4 bar to 13 bar. In the compressor air end two long helical screws mesh together at high speed. The space between the housing and the edge of the screws is sealed with oil pumped into the air end. As the screws come around to the inlet port air is drawn into the cavity between the meshing screws. The screws continue to rotate but the gap between the meshed helical threads gets smaller and the air is compressed. As the screws complete their rotation the compressed air and oil mist is ejected into an oil separator. The oil is collected and the air continues into the receiver or accumulator.
Right away you can see that one of the problems with screw compressors is going to be oil carry-over and it is necessary to provide additional filtration at the outlet of the compressor discharge to minimise this problem. The air end is a very fine tolerance machine, typically the clearance between rotor and housing is 0.03 mm (0.0015”). Anything solid that falls into the air end will destroy it. The seal oil and air cleaning systems must be kept meticulously clean.
Because the air comes out hot and the delivered air volumes are so large it is common to install a water-cooled after-cooler or refrigerated air dryer. The secondary benefit of a refrigerated air dryer is that it condenses the water vapour present in the hot air (from the initial atmospheric intake) back to liquid and discharges it and makes the air dryer. Other forms of dryers, like the desiccant (activated carbon) type, are also available. If instrument quality air is needed then a dryer capable of removing the water vapour to the required amount of dryness must be used.
Other operational issues with rotary screw compressors have been rotor shaft end seal leaks from poor manufacturing tolerances; on vee-belt driven machines the belts can slip either from stretch or from dust settling onto the pulleys and reducing the coefficient of friction. In a dusty location the entire machine cabinet internals must be sealed from the dust and additional filtration added to the air intake grill. When things go wrong with these machines they are costly to fix. Regularly service them, provide quality air and oil filtration and condition monitor to get the longest, trouble free life.
Reciprocating Compressor Issues
A reciprocating compressor uses a piston and cylinder to squeeze a small volume of air into a tight space in the cylinder head before releasing it. Multiple pistons can be used. These machines produce low volumes of air, measured in 10’s of CFM, and up to very high pressure in the 100’s of bar. The pressures are adjustable by a pressure switch that signals when the outlet valve opens.
Operating issues with these machines include the need to control the vibration induced by the reciprocating piston. Insuring the unit is solidly bolted down onto a thick concrete surface is usually sufficient but on light floors it may be necessary to put it on vibration dampening mounts. Most units are vee-belt driven and these require periodic replacement or tightening as they stretch. Usually a 3-month preventative maintenance (PM) routine covers this problem. The smaller models come as a ‘packaged unit’ with their own air receiver. In that case the air receiver requires an automatic drain installed on the bottom drain point to prevent water building up in the receiver. Receivers can filled up with water following the failure of the auto-drain. Again a 3-monthly PM to test the auto drain operation will pick up this problem.
Mike Sondalini – Maintenance Engineer
If you found this interesting, you may like the ebook Bulk Materials Handling Introduction.
I want to get an air compressor for my workshop. It makes sense that proper maintenance would be important! That way, I don’t have to worry about it breaking or anything.
What do you think about a single-stage air compressor? Does it usable for painting cars?
As I know, for painting cars, its too important to have high CFM?
What your thoughts?
Anyway, Thanks for your detailed guides.