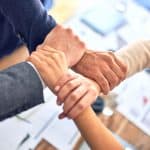
“A thought, even a possibility, can shatter and transform us.” – Friedrich Wilhelm Nietzsche
One of my favorite FMEA facilitation techniques, and one that can significantly enhance meaningful participation from FMEA team members, is called “Asking Thought-starter Questions.”
Merriam-Webster defines “thought” as “the action of process of thinking” and “starter” as “something that is the beginning of a process or activity.”
What are thought-starter questions?
Thought-starter questions are designed to stimulate thinking in the team. Specifically, for each FMEA element, like function, failure mode, effect, etc., the purpose of thought-starter questions is to get the team thinking constructively about that specific element.
What are examples of thought-starter questions in a Design FMEA?
I’ll use a simple example of a Design FMEA on a bicycle brake cable to illustrate this technique. Click Excerpt from All-Terrain Brake Cable Design FMEA to see an excerpt from a fictitious FMEA on brake cable.
Function
In a Design FMEA, a function is what the item is intended to do, usually to a given standard of performance or requirement. The DFMEA focuses on the primary functions.
To use thought-starter questions to determine a function for a bicycle brake cable, rather than saying, “what is the function?” try asking, “what is the purpose of the bicycle brake cable? What is it intended to do?” This will get better discussion and does not require the FMEA team to be experts in FMEA definitions.
Failure Mode
Failure mode in a DFMEA is how the item fails to deliver the intended function and its associated requirements.
If one of the intended functions of a brake cable is “to provide adjustable and calibrated movement between the brake lever and brake caliper,” how should the facilitator ask for failure mode?
Should the facilitator say, “What is the failure mode?” In my experience, this is not the best way to stimulate the right thinking. First, the question presupposes the team understands very well the definition of failure mode. It is better to say, “what is the manner in which the brake cable will not provide adjustable and calibrated movement between the lever and the caliper?” Or, “what could go wrong with the brake cable when it is providing its primary function?” There are countless ways to ask the question, but the key is to elicit discussion around the concept being addressed. This bypasses the need for the team member to understand the definition fully, and goes straight to the concept of the way the cable might fail, and the mode of the failure.
Effect
In a DFMEA, effect is the consequence of the failure taken to the system or end user. It can be a progression at local level, followed by the next level up to the system or end user. However, in all cases, the team does its best job to describe the consequence at the system or end-use level.
Let’s say one of the failure modes is “cable breaks.” How should the FMEA facilitator ask for the effect of this failure mode?
Should the facilitator ask, “what is the effect?” Again, this is not the best way to bring about the right discussion. It would be better to ask, “if the cable breaks, what is the consequence to the bicycle or the rider?” Or, “what could possibly happen when the cable breaks locally and tracing up to the bicycle and rider?”
Cause
Cause in a Design FMEA is the reason for the failure mode, expressed as a potential design deficiency.
For the failure mode “cable breaks,” the facilitator might ask, “why does the cable break?” or “what potential design deficiency would explain the cable breaking?” Or any other variation that explores the concept of the cause.
What are examples of thought-starter questions in Process FMEA?
To illustrate this technique, I’ll use a simple example of a Process FMEA on one of the steps for assembling a bicycle wheel; specifically “Wheel spoke installation.” Click Excerpt from wheel-spoke installation PFMEA to see an excerpt from a fictitious FMEA on wheel spoke installation for a front wheel assembly.
Function (Operation Description)
In a process FMEA, function, or operation description is what the process step is intended to do, usually to a given standard of performance or requirement. Rather than ask the team for a function, you could say, “what is the purpose of the wheel spoke installation process step?” It might be “Orient and place 36 wheel spokes properly in wheel assembly fixture.”
Failure Mode
To ask for a failure mode in the bicycle wheel spoke example, you might ask, “How could the wheel spokes be installed incorrectly?” or “What could go wrong with placing the wheel spokes in the assembly fixture?”
Effect
Similarly, when discussing effects, you could ask, “If there are too few spokes placed in the wheel assembly fixture, what is the consequence to the next operation or the assembly line?” Or “What happens to the bicycle assembly if there are too few spokes placed in the wheel assembly fixture? How does it get remedied?”
Cause
When discussing the cause, you could ask, “what about the bicycle assembly process might be a reason we end up with too few spokes?” Or “What process deficiency might explain why we could have too few spokes?”
Summarizing
When using thought-starter questions, each element of the FMEA is discussed by asking questions that align with the fundamental concepts of the FMEA element rather than merely referring the column heading. Other facilitation skills are also used to elicit deep discussion with the team. Sure, you could say, “what’s the cause?” But you get better results by asking, “what is a potential design deficiency that would result in the failure mode?” Or any variation that is faithful to the concept being discussed.
Thought-starter questions are only just that . . . thought starters and are not meant to limit in any way the skill of the FMEA facilitator and team in establishing the content of the FMEA. They are intended to get the team thinking about the right concepts.
Tips
Thought-starter questions are not rote. They are not canned. Nothing takes the place of fully understanding the FMEA definitions and concepts. If you want to apply thought-starter questions, the best way is to practice, practice, practice the definitions and concepts of FMEA, and use that understanding to craft meaningful questions and fully engage the team.
Next Article
The next article in the FMEA Facilitation series is called Active Listening. Understanding what another person is saying and why they are saying it is key to meaningful and productive discussions.
Leave a Reply