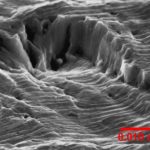
Fatigue is a common degradation and failure mechanism. It involves localized, permanent damage to metals exposed to cyclic stress. The stress can be uniaxial, bending, or torsional resulting from a variety of sources including an applied force, vibration, acceleration and deceleration, and differences in thermal expansion between mating components exposed to heating and cooling cycles. Localized means the damage is confined to a small portion of a component or joint.