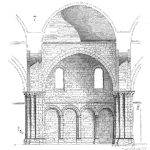
Quality issues have been on my mind a lot lately, specifically some of the more frustrating things that I’ve had to deal with during my career as a quality manager.
In my last job, my team was responsible for managing the discrepant material review (DMR) process for our US-based factory.
The DMR process
For those who are unfamiliar, the DMR process is how most factories deal with raw materials or other inputs that have been identified as possibly defective and unsuitable for use.
Incoming materials that don’t pass visual inspection or other testing are supposed to be sequestered so they can’t go into production.
Later, the DMR process is used to determine what to do with that material. The choices are usually:
- Accept the material (use it in production) because on closer examination it’s not defective after all, or the defect isn’t serious enough to prevent it from being used. There’s a risk to this choice, but maybe the risk of shutting down the factory because of insufficient material, or otherwise missing a production quota is greater.
- Rework or repair the material, then use it. Obviously, this option is limited to fairly minor defects that can be quickly addressed at the factory and assumes that the folks at the factory can make it usable.
- Reject the material and return it to the supplier. Assuming the material wasn’t damaged after transfer of title, the supplier is obligated to take responsibility for defects. At that point, there may be some disagreement with the supplier about whether this really is a defect. Ultimately there’s a discussion about full replacement vs. rework of the defective material at the supplier.
- Scrap it. This is a bad choice, but it basically means it’s not worth the time to repair it or return it to the supplier. Of course, this means additional expense, both to dispose of the defective material and to order and purchase replacement material.
The problem with our DMR process was that it was impossible to make an objective judgment.
All of the functional groups and stakeholders were biased toward one option or another, and the quality team had no power to make the final call or enforce a decision.
The operations folks were usually willing to take a risk with marginally-acceptable material so they wouldn’t slow down production. The procurement folks didn’t want the hassle of returning material to suppliers. Our VP didn’t want to approve the expenses associated with scrap material and basically made it impossible to do so.
The quality team mainly just wanted to be sure the material wasn’t used as-is, and that the supplier implemented some kind of corrective action to prevent future occurrences of the same defect. Unfortunately, we didn’t have the power, or credibility, or respect, or something to get the rest of the organization to support our position.
What typically happened was that either the operations folks used the DMR material, convincing themselves that the defects were minor, or the DMR material piled up in a corner of the receiving area, waiting for somebody to blink.
It got to the point that we were actually considering paying for off-site storage space for this stuff.
I think there are a lot of lessons here, but here are a few:
- Don’t bother setting up a DMR process if you’re not prepared to actually deal with discrepant material and its causes. How bad does the material have to be before it’s returned or scrapped? Are you going to accept everything?
- Quality isn’t absolute. What was a defect yesterday may be acceptable today, especially if the factory is running behind the production schedule. Maybe the customer won’t notice. If they do notice, remember that I told you so.
- If you’re not going to hold your suppliers accountable for quality, then stop pretending that quality is a consideration in selecting suppliers or ordering material.
This wasn’t the way it was supposed to be, but that’s how the DMR process was managed in this business.
I suspect other businesses have similar problems because they’re willing to trade a possibility of failure for expediency and “expense control.”
Related:
Material Selection and Reliability (article)
Purpose of a Reliability Program (article)
Subcontracting Quality (article)
Leave a Reply